MIL-I-46058C: Definitive Guide to Military Standards for PCBAs
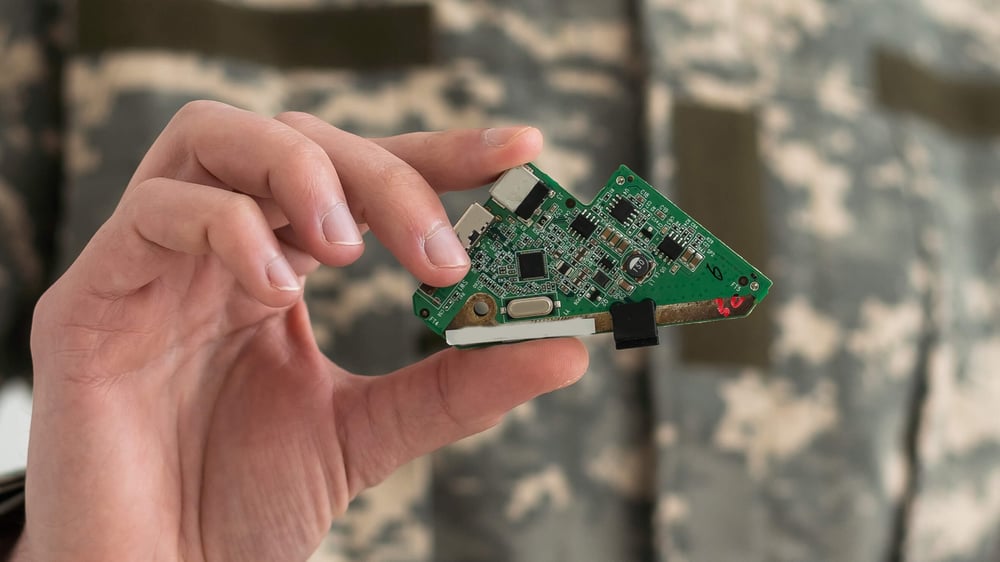
Reliability is a top priority in defense and aerospace electronics in harsh, unforgiving environments. The MIL-I-46058C standard is a guideline for conformal coating materials that helps keep PCBAs safe from military environments, ensuring dependable performance. Although IPC-CC-830 replaced this standard in 1998, understanding MIL-I-46058C is still non-negotiable for industry compliance and mission success.
Even though deemed inactive for new designs since 1998, MIL-I-46058C remains an independent standard for companies who supply conformal coatings for two essential reasons: it is the only published standard that includes a qualified product list used by the DOD, and the standard also requires certification by an independent third party.
The criteria set forth by MIL-I-46058C for conformal coatings are integral in aerospace and defense applications. These coatings must withstand extreme atmospheric conditions, rapid pressure changes, and varying degrees of moisture and chemical exposure. Adherence to such standards ensures operational effectiveness and safety in critical missions.
Importance of MIL-I-46058C
In the realm of military specifications and standards, MIL-I-46058C stands out for its stringent criteria for conformal coatings. It represents a level of assurance for military equipment that non-military standards do not necessarily guarantee. By complying with this specification, manufacturers and defense contractors can affirm the longevity and performance of their electronic components, even in the harshest environments, by using the proper coating materials.
The primary function of conformal coatings is protection: they are a barrier that prevents contamination, such as chemicals, moisture, and humidity, from causing short circuits or corrosion.
Coatings such as acrylics, urethanes, epoxies, silicones, and Parylene also resist corrosive gases and salt sprays, reduce mechanical stress due to handling or thermal expansion, and protect against corrosive gases and salt sprays.
MIL-I-46058C is pivotal in enhancing product longevity and dependability by defining the performance criteria for conformal coatings. Electronics treated with MIL-spec conformal coatings typically showcase better performance over their lifecycle and are less likely to fail due to electrical shorts, interference, or damage from environmental factors.
Examples of criteria include:
- Dielectric Breakdown Resistance: Coatings must not degrade when subjected to high voltages.
- Insulation Resistance: Coatings should maintain high resistance to prevent leakage currents.
- Hydrolytic Stability: Insulation properties must remain intact even when exposed to moisture.
- Thermal Shock Resistance: The insulating capacity must withstand sudden temperature changes.
Military Standards for Humidity and Environmental Protection
MIL-I-46058C establishes clear humidity and environmental protection requirements. Ensuring electronics meet such standards is essential for performance and longevity, especially in military and aerospace applications where failure is not an option.
Electrical Insulating Properties
Conformal coatings possess significant electrical insulating properties essential to preventing electrical leakage and ensuring the current flows only where it is meant to go. This characteristic is particularly valuable in high-density circuitry where electrical components are closely packed, reducing the risk of interference or shorts between conductors.
Coatings under the MIL-I-46058C specification are designed to act as electrical insulators, creating a dielectric layer that safeguards circuitry from shorts and arcing caused by environmental challenges.
Their resistance to electricity contributes significantly to preventing malfunctions and potential damage. With an appropriate application, conformal coatings provide excellent insulation, even under fluctuating electrical loads.
Defining Thermal and Mechanical Standards
The MIL-i-46058C specification is instrumental in defining the thermal and mechanical performance parameters for conformal coatings used in military and aerospace applications. It ensures that coatings are capable of functioning under stringent conditions without degrading performance, encompassing:
- Tensile Strength: The coating's ability to withstand pulling forces without breaking
- Thermal Shock Resistance: The coating's capacity to endure sudden changes in temperature without compromising its structural integrity
- Flexibility: The ability of the coating to flex with the substrate material, which is essential for performance during mechanical or thermal stress
Read More About HZO Coating Properties
Mastering Application Techniques for MIL-I-46058C Conformal Coatings
Whichever application process (dipping, spraying, vacuum deposition, brushing) is used, achieving uniform coating and coverage is the primary concern. Factors such as temperature, humidity, and the geometry of the printed circuit board (PCB) can all influence the outcome. It's essential to follow strict processing guidelines, provide adequate training for operators, and implement inspection procedures to ensure that the conformal coatings delivered meet the high standards set by MIL-I-46058C.
Quality Control, Testing, and Industry Compliance
In the realm of conformal coatings and electronic circuit protection, Quality Control (QC) and rigorous testing are pivotal in ensuring that products meet the stringent requirements of MIL-I-46058C. For manufacturers and service providers in the electronics industry, adherence to recognized standards is a benchmark for quality and a requirement for credibility and trustworthiness in the marketplace.
It's essential to have a well-established process encompassing multiple tests and inspections to comply with the MIL-I-46058C specification. This involves:
- Thorough examination of thickness uniformity and coverage using various measurement techniques
- Stringent electrical testing to ensure that the conformal coating does not impede the intended function of the PCB
- Mechanical and environmental stress testing to verify that the coating can withstand harsh conditions without degrading
Quality control in the application of conformal coatings is multi-faceted, including:
- Visual inspections for surface defects post-application
- Adherence to production protocols that minimize the risk of contamination
- Product batch testing to ensure consistent quality across different manufacturing lots
These QC procedures are integral to maintaining the high standards expected in industries where reliability is paramount.
Read About HZO's Coating Process
Processes for Ensuring Compliance with MIL-I-46058C
Coatings optimized for the MIL-I-46058C specification must undergo tests to affirm that the PCBs meet the rigorous demands of their respective applications. The MIL-I-46058C specification outlines a series of stringent tests to evaluate the corrosion resistance of conformal coatings.
High humidity exposure, salt fog conditions, and immersion trials are methods used to simulate extreme environments and validate a coating's protective capabilities. Adherence to these testing protocols is crucial for manufacturers to certify that their conformal coatings meet the high standards expected for components in critical applications.
- Humidity Exposure: Coatings are tested for their ability to withstand high moisture levels without degrading.
- Salt Fog/Spray Testing: Assesses the coating's resistance to corrosive salt environments mimicking marine conditions.
- Immersion Trials: Ensures that coatings can protect components even when submerged in liquids.
Through rigorous testing and compliance with MIL-I-46058C, electronics manufacturers can ensure that their products stand up against environmental challenges, thereby reducing maintenance costs and extending the operational lifespan of the devices they protect.
See HZO nanocoatings pass in-house testing
Industry Certifications and Compliance
While the MIL-I-46058C provides a comprehensive framework, aligning with broader industry certifications reinforces a commitment to excellence. Relevant certifications might include:
- ISO 9001: For quality management systems
- IPC-A-610: For acceptability of electronic assemblies
- IPC-CC-830B: For electronic circuit protection conformity
Sustaining such certifications ensures that a company's products are compliant with military specifications and meet high-quality standards recognized internationally within the electronics sector.
Differences between MIL-I-46058C and other standards like IPC-CC-830
MIL-I-46058C specifies testing methods and minimum performance requirements, focusing on the suitability for military environments. Meanwhile, IPC-CC-830 is typically utilized within the civilian sector and offers broader guidelines for conformal coating use.
While both set high standards for protecting electronics, MIL-I-46058C is tailored for military applications that often face more extreme operational scenarios.
Understanding the nuances between MIL-I-46058C and standards like IPC-CC-830 is crucial for those supplying electronics to military and commercial markets. Selecting an appropriate conformal coating that adheres to relevant standards is a critical factor that drives the long-term success and dependability of sensitive electronic equipment.
Addressing Obsolescence: Alternatives
As technology evolves, so do the standards that govern it. With MIL-I-46058C now considered obsolete, manufacturers may wonder how to navigate this change effectively. The discontinuation of this military standard has prompted the electronics industry to seek modern alternatives that provide equivalent or superior protection for electronic components.
Manufacturers must comprehend this obsolescence and its implications for production and quality assurance processes. A proactive approach is necessary to adapt to new regulations and maintain compliance.
One of the prominent specifications that have emerged as a successor to MIL-I-46058C is IPC-CC-830. This standard is widely recognized in the industry and is designed to meet the current and future demands of electronic device protection. Manufacturers can confidently transition to IPC-CC-830, knowing it offers a comprehensive framework for ensuring the reliability and longevity of their products.
Tips for Transitioning to New Standards
Moving to contemporary specifications like IPC-CC-830 can be a daunting task. Below are some essential tips to facilitate a smooth transition:
- Conduct a thorough analysis of current processes and how they align with new standards.
- Engage with material suppliers to identify conformal coatings that meet the requirements of IPC-CC-830.
- Schedule training for the production and quality assurance teams on the nuances of the new standard.
- Implement a phased approach to transition, allowing ample time for adjustments and validation.
- Consider consulting with industry experts who can offer insights and guidance on maintaining compliance.
By embracing these modern specifications, manufacturers not only comply with the current standards but also position themselves to adapt more readily to future advancements in technology and regulatory environments.
MIl-I-46058C Coatings With HZO
HZO coatings have passed IPC-CC-830 (widely considered an active alternative to MIL-I-46058C) at 50% of the thickness of conventional coatings, providing the protection required for military applications at a fraction of the mass. HZO is ITAR-registered and ready to partner with you on your military application. Contact one of our engineers to learn more. Stay informed, stay compliant, and, most importantly, remain confident in the quality of your military and aerospace applications.
Biocompatible Coatings - Coating Techniques, Applications, More
UL94 Coating Material - Testing Method, Material Selection
What is the Index of Refraction? Measurement, Definition & More
Mallory is a veteran writer with over a decade of writing experience and has spent over five years at HZO learning about coating technology from the best minds in the industry. Professionally, Mallory is especially interested in the process of problem-solving and watching how the engineering team develops solutions that ensure business requirements are met. Over her years at HZO, Mallory's writing has been cited in industry whitepapers, including "Parabolic Model for Optimum Dry Film Thickness (DFT) of Corrosion Protective Coatings" and "Universal Approach to Integrating Reduced Graphene Oxide into Polymer Electronics." All of Mallory’s blogs are reviewed for accuracy before publication.
Additional Resources
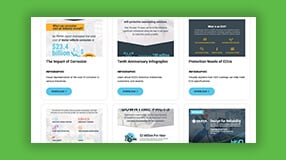
Understand the Capabilities of Thin Film Coatings With Our Resource Page
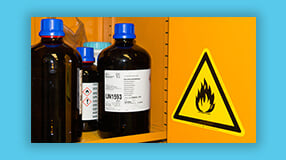
Understand UL94 Rating - Testing, How to Choose a Material, and More
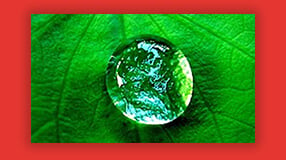
What's the Difference Between Hydrophobic Coatings and Hydrophilic Coatings?
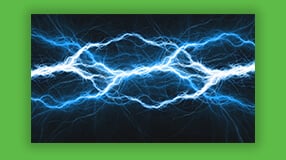
Dielectric Constant of Insulator - Materials, Formula, Table of Values
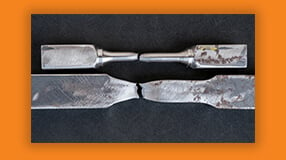
Tensile Strength at Yield - Testing, Definition, Material Selection
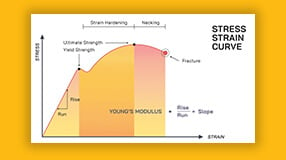
Young's Modulus of Polymers - Measurement, Calculation, Material Selection
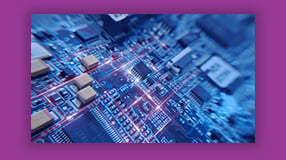
Volume Resistivity - Definition, Measurement, Implications For Product Design
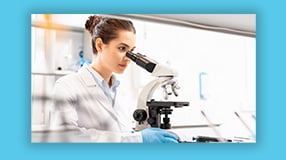
Polymer Glass Transition Temperature – Material Properties, Impact
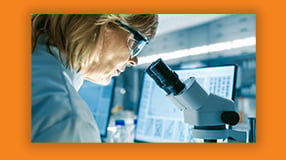
What is Coefficient of Linear Expansion? Formula, Units & More
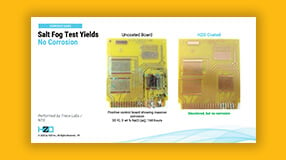
Learn About the Thin Film Coating Properties and Processes In Our Webinar
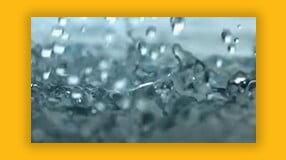
The Difference Between "Hydrophilic and Hydrophobic" Coating Properties
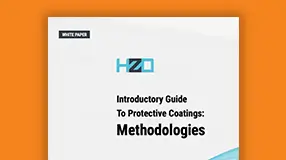
Learn about Protective Coating Methodologies With Our White Paper
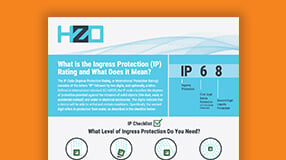