HZO's Turnkey Parylene Coating and Nanocoating Solution
Our ready-to-deploy turnkey coating solution provides our customers with all aspects of the
nanocoating or Parylene process for convenience, consistency, and
peace of mind. People, processes, material science expertise, and equipment are
at the heart of our turnkey solution, no matter the business model you choose.
HZO People
Dedicated engineers and industry subject matter experts guide every project we take on. Our team has virtually seen it all, understands when and how to help, and will help you understand your business’s complex challenges, offering useful feedback that can avoid complications.
As a highly collaborative organization, we believe that while individual knowledge is good, collective wisdom drives the best results. Our combined experiences and insight drive our innovative thinking, resulting in the quick resolution of problems and out-of-the-box solutions, and a streamlined, convenient experience for our customers.
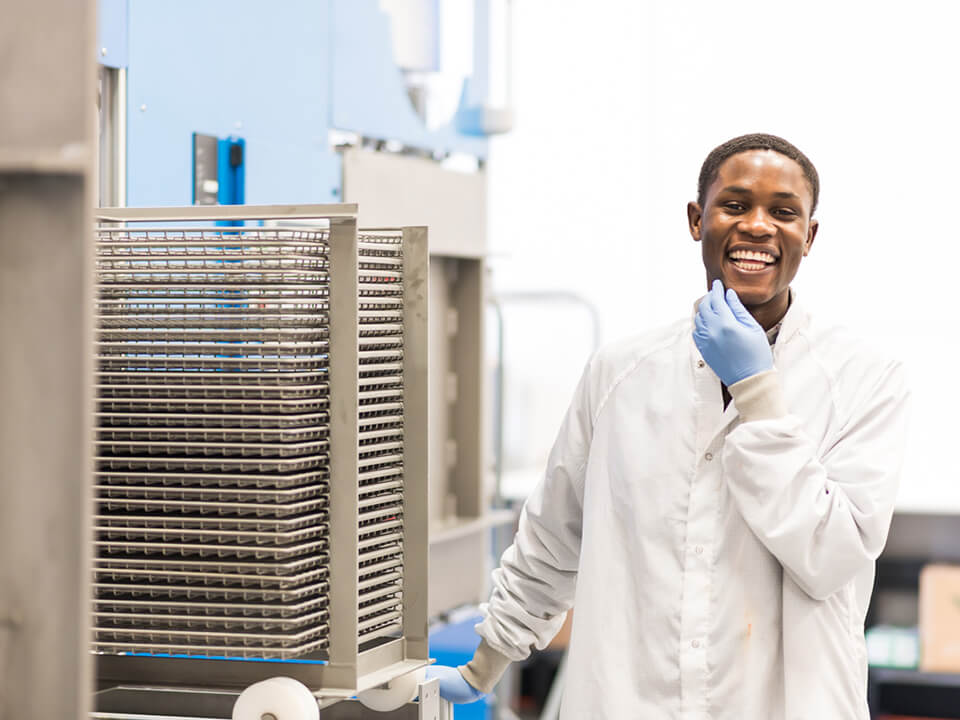
What This Means for HZO Customers
-
You can always expect us to streamline your processes and make tweaks to increase efficiency or cost.
-
When we work with you, it is a constructive partnership.
-
Our team has the capacity and incentive to be proactive about potential problems.
-
Dedicated customer-facing engineers will explain all aspects of our process and understand yours, providing clear timelines, issue resolution, and guidance for future designs.
-
We understand how to obtain and secure the best materials at the best cost and collaborate to suggest design changes accordingly.
HZO Processes
We have been in business for more than a decade, and after coating millions of HZO-protected components with no product returns due to coating issues, we firmly believe that process makes perfect.
Our processes were developed to yield quality, efficiency, throughput, and scale from the first day of development until the last day of production, including before and aftermarket services such as cleaning, inspections, and troubleshooting.
More About Our Industry-Leading Processes
Although many of our methods are trade secrets, here are some of the proprietary strengths
we bring to nanocoating and Parylene our coating processes:
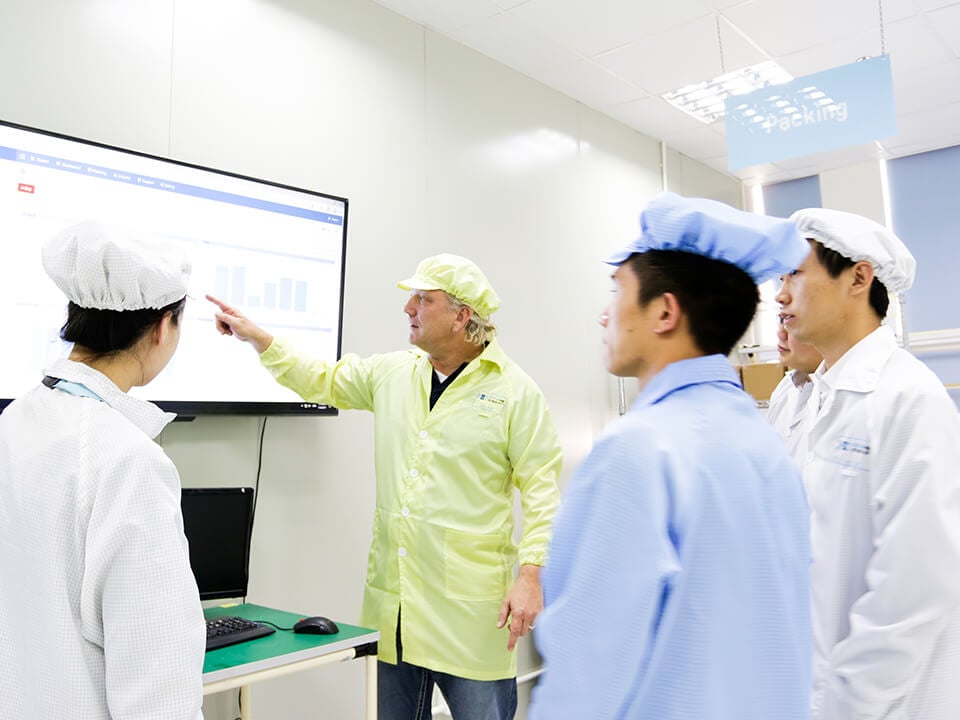
Training and Handling
Our employees are our most valuable asset, so we do all we can to empower team members with the skillsets required to meet our standards of excellence. We regularly define training programs and only release operators and processes with proven performance levels to the production environment. Our staff has extensive experience with scalable workforces, a valuable asset for mass production.
All HZO facilities are ESD compliant, and all operators and engineers are fully trained in the importance of ESD protection and how to handle electronics safely.
Inspection
HZO inspects products for “critical to quality items” and component damage at both the incoming and outgoing stages and conducts interim inspections for placement and completion to ensure good masking performance. Additionally, we utilize 100% inspection at the sampling and preproduction stages before moving to an AQL sampling as determined between HZO and the customer.
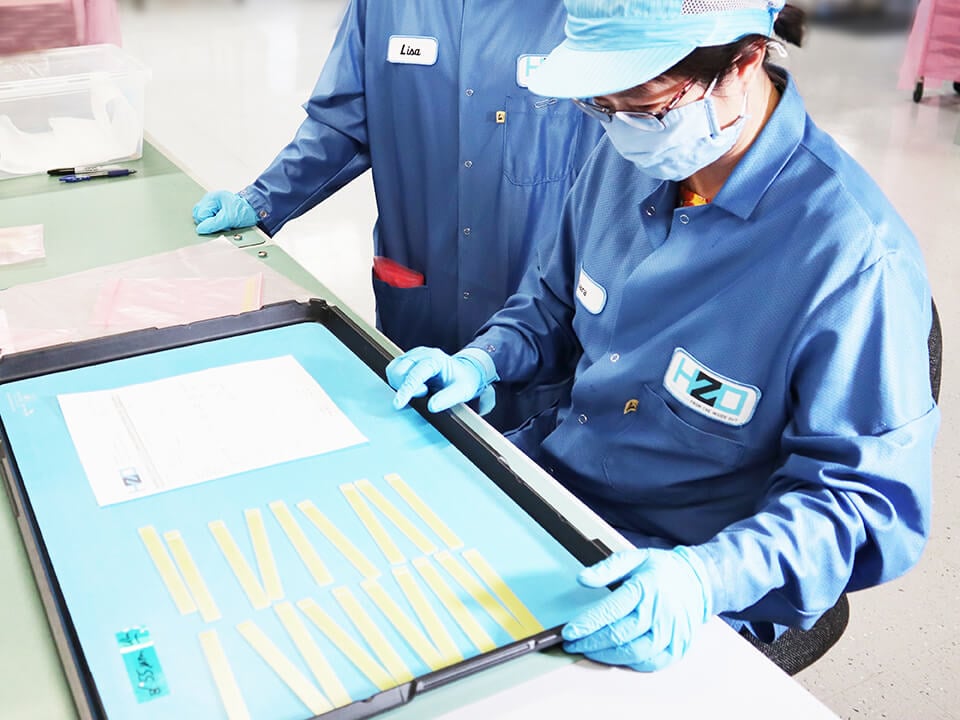
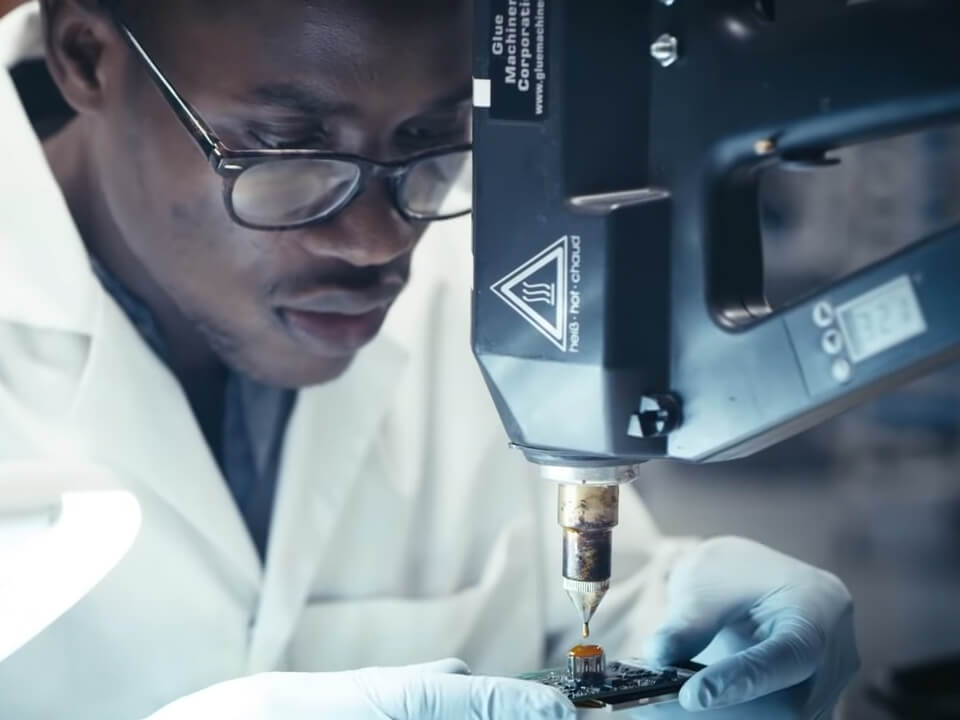
Masking
When masking is required, we work closely with customers to ensure that we both clearly understand and communicate areas needing masked, potential risks, and opportunities for DFM guidance. HZO has a variety of well-characterized materials for all masking tasks, each with strengths around component types and situations.
We use masking fixtures to mitigate risks and increase efficiency, and if required, the masking process is scalable through semi-auto and automated masking equipment.
Loading
Individual products require individual solutions. We have designed racking and trays in the coating chamber to minimize touch points, avoid component damage, and increase loading efficiency. HZO utilizes a combination of custom and universal racking solutions to maximize the efficacy of the chamber loading process and the overall return on investment.
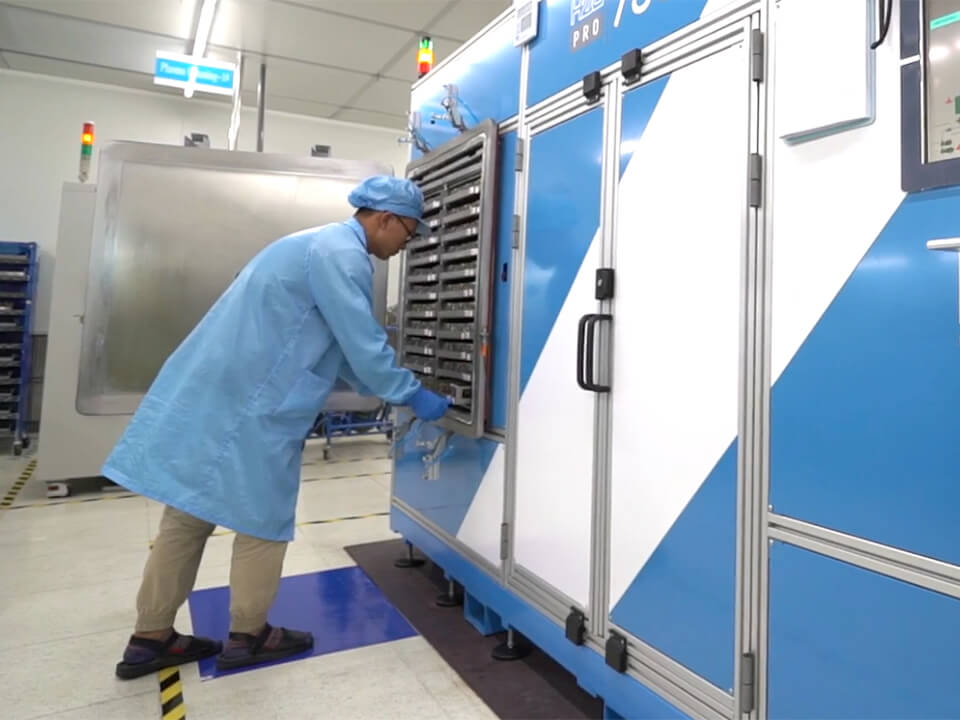
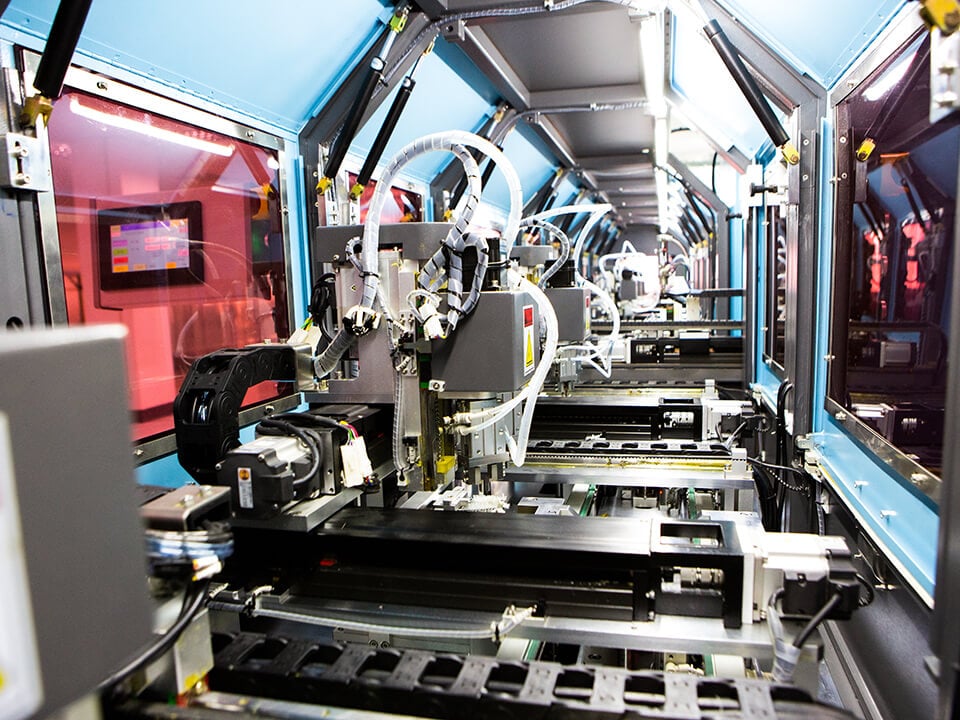
Demasking
The removal of masking materials is as nuanced as choosing the proper masking technique. Therefore, consistently identifying process improvements and continual training are critical to our performance. As with our masking process, we can use automation with demasking to increase throughput for high-volume applications. Laser scoring, ablation, and automated inspection help mitigate touchpoints, while strain gauge testing will ensure that the product is not subject to undue force.
Quality
Quality is key to everything we do, from initial customer communications to inspection criteria through handling and reporting out. At all stages, our fully trained staff handle your product with due care and attention to achieve the best possible outcome.
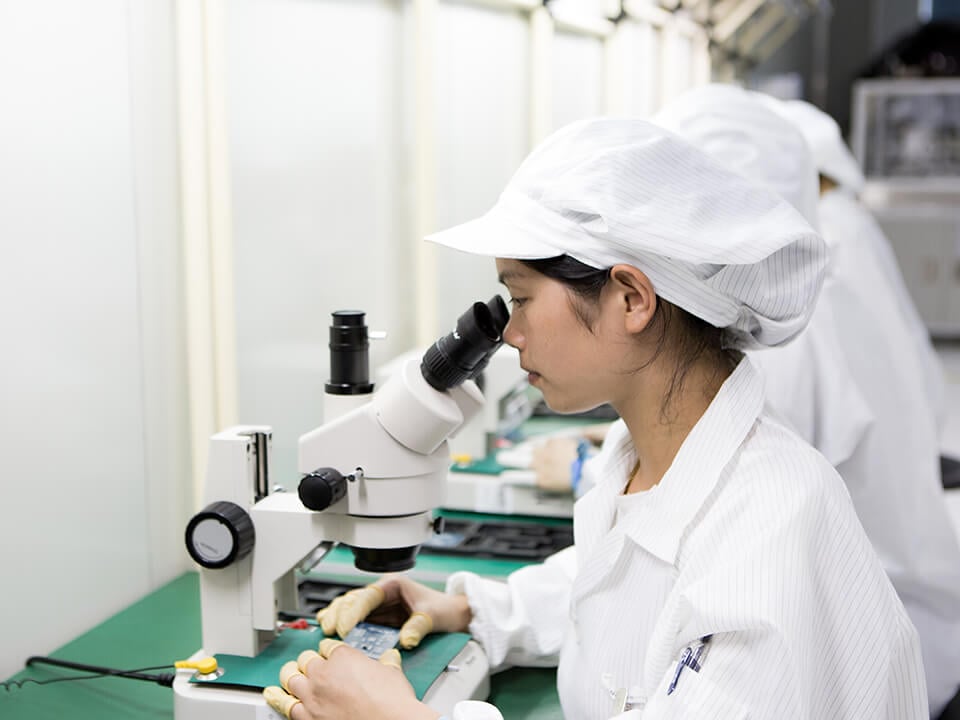
Material
We secure a steady supply of the highest quality coating materials at the most competitive prices so that you can avoid surprises associated with material cost or stock. Our engineers have the required skills to select the appropriate material upon considering your business requisites including:
-
Application requirements – What standards must the component meet? What environmental risks are expected in the operating environment? Must the coated component pass testing prior to our partnership or to qualify for sale in an industry? How long must the component reliably operate?
-
Budget – Is reliability or cost a priority? What is the production volume? Will automation be required?
-
Market considerations – Does the product need to meet marketing claims, such as IP ratings? Is there a warranty period? Is brand equity a concern?
-
Design parameters – What tolerance is required? How durable must the product be? How complex is the substrate to be coated?
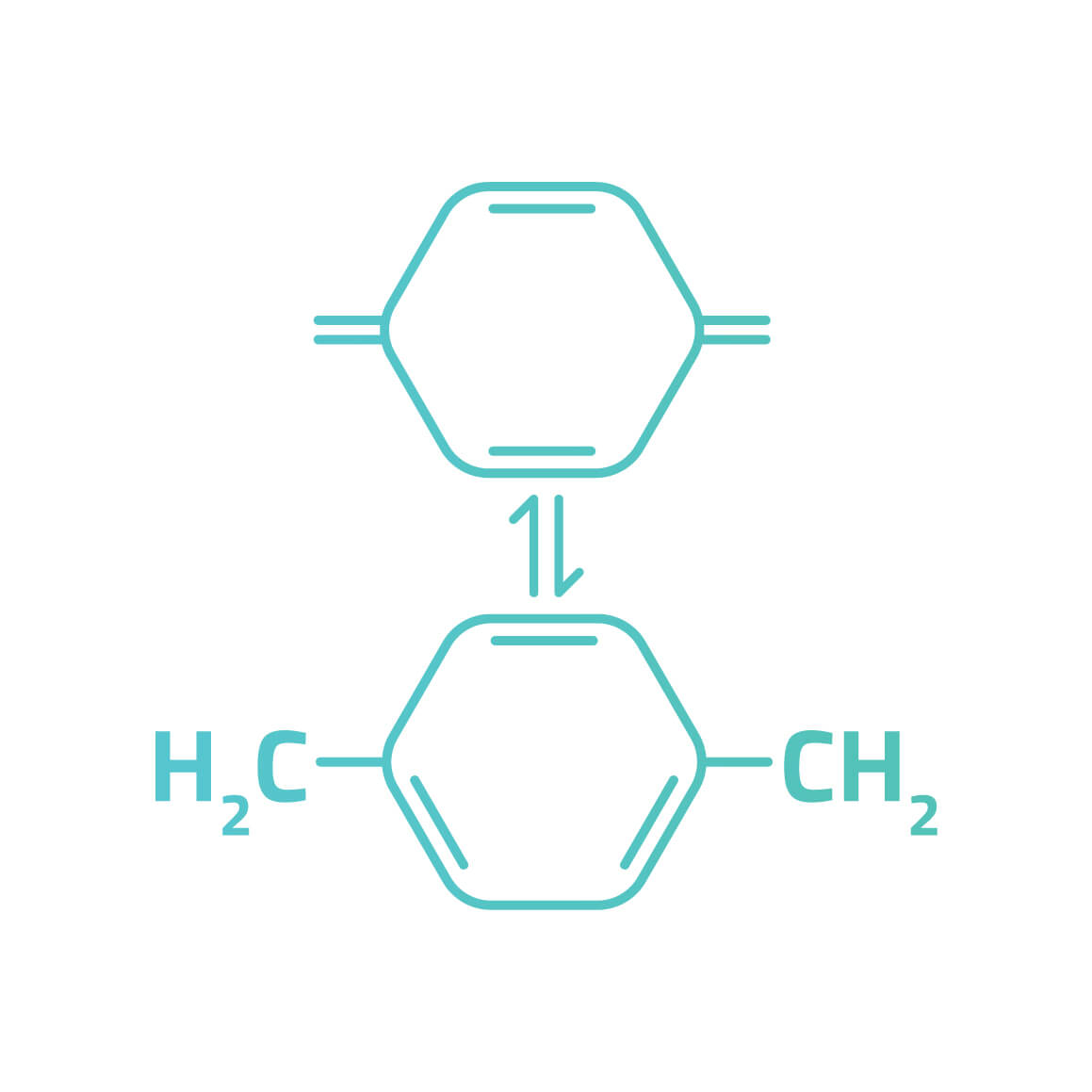
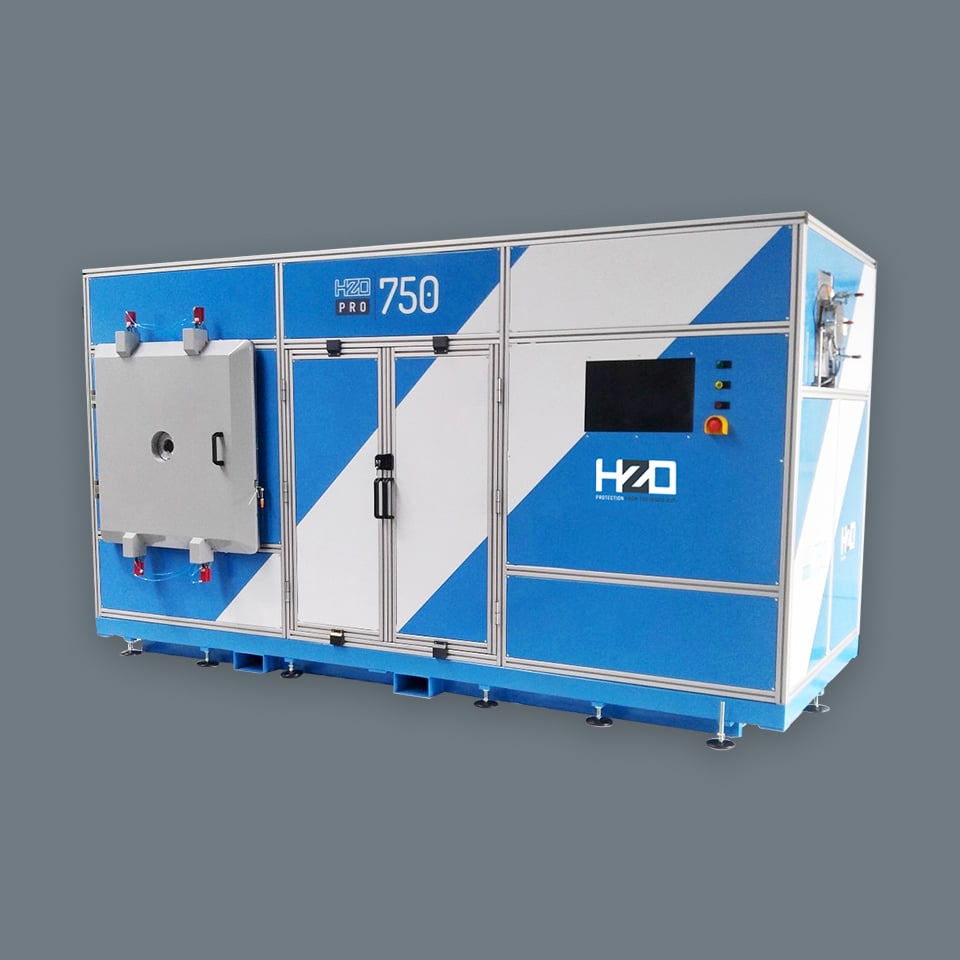
Equipment
Our coating chambers are optimized for performance, capability, scale, and efficiency. HZO’s experts have:
-
Maximized coating efficiency by increasing the size and shape of our Parylene deposition chambers.
-
Improved coating consistency with patented heating, cooling, and in-chamber processes.
-
Automated pre and post-production processes for predictable throughput.
-
Written software and built controllers that continually measure and optimize temperature, pressure, and other critical data points.
Our coating machinery and materials have been honed to the point where we can handle the most complex of circuitry, sub-assembly or devices, whether we coat in your facility or ours. Our experience allows us to operate:
-
Without damage to the chip, printed circuit board (PCB), printed circuit board assembly (PCBA), or device
-
Without overstressing the components
-
To the exact tolerances and measurements required
What Our Turnkey Solution Means for You
What does it mean when we bring together the best people, processes, materials, and equipment in the industry?
- Outstanding quality: Informed by industry know-how, our quality assurance team ensures no component gets left behind for exceptional coating coverage.
- A shared objective of improving your product: We have a vested interest in your success instead of a fragmented approach to coating, which may lead to a loss of focus.
- Accountability: Our dedicated team proactively addresses issues with personalized service and designated account contacts.
- Shorter production times: Our established protocols and systematic approach to project workflow boost efficiency, making it easier to get back on track if there is a setback.
- Optimized systems: We continuously evaluate our turnkey solution to improve the manufacturability, yield, and performance of products.
- Regulatory compliance: We ensure that our equipment and processes comply with environmental and safety regulations.
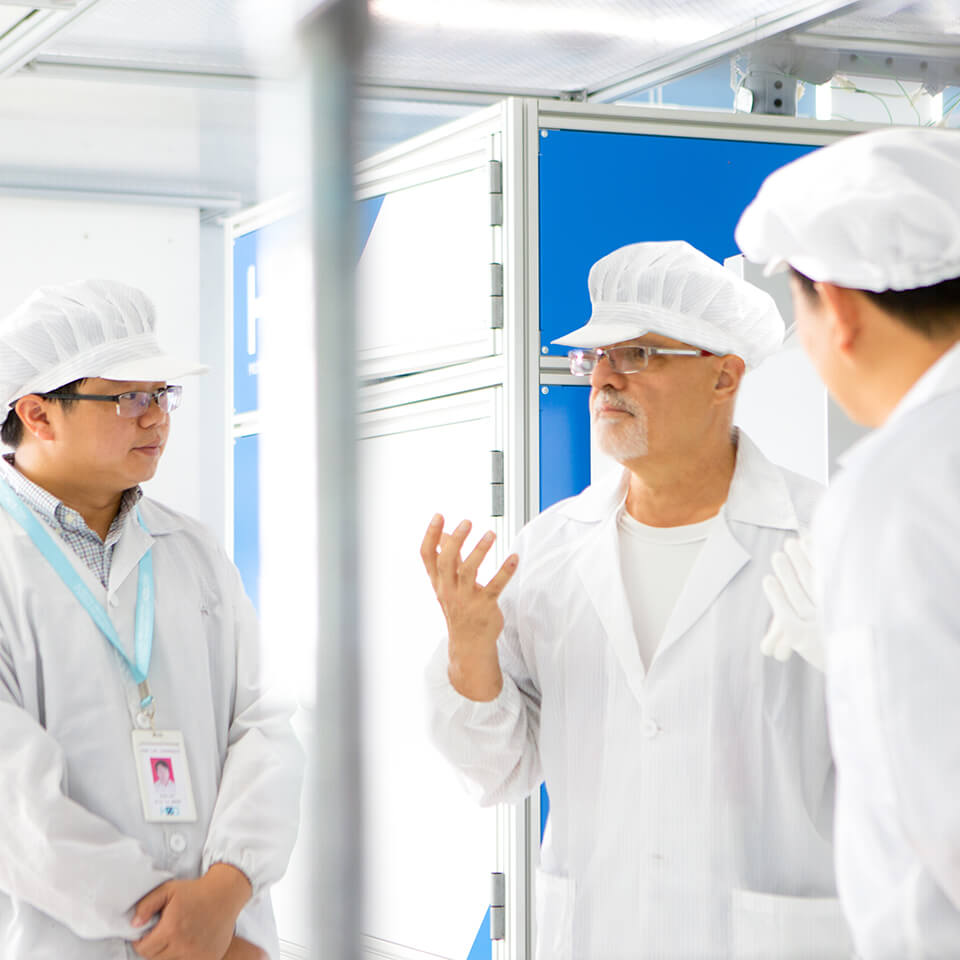
Are you interested in learning more about HZO’s turnkey solution and how it can help you achieve your business objectives? Contact us today for a DFM consultation.
Additional Resources
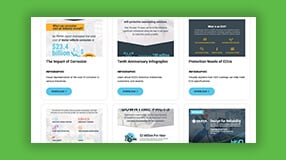
Understand the Capabilities of Thin Film Coatings With Our Resource Page
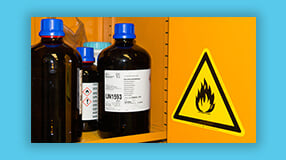
Understand UL94 Rating - Testing, How to Choose a Material, and More
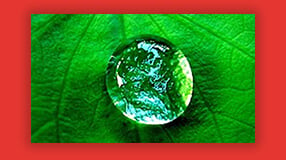
What's the Difference Between Hydrophobic Coatings and Hydrophilic Coatings?
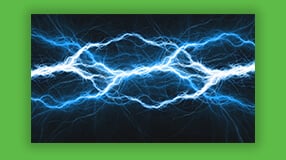
Dielectric Constant of Insulator - Materials, Formula, Table of Values
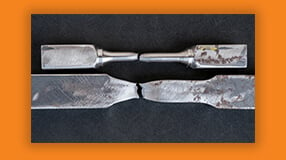
Tensile Strength at Yield - Testing, Definition, Material Selection
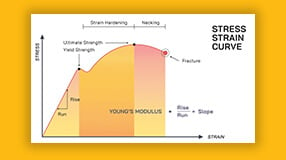
Young's Modulus of Polymers - Measurement, Calculation, Material Selection
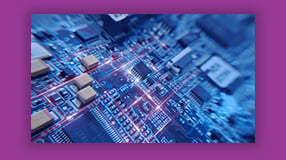
Volume Resistivity - Definition, Measurement, Implications For Product Design
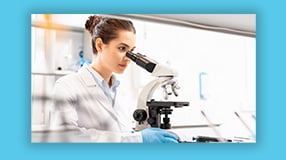
Polymer Glass Transition Temperature – Material Properties, Impact
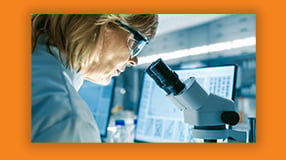
What is Coefficient of Linear Expansion? Formula, Units & More
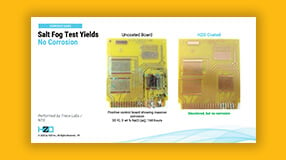
Learn About the Thin Film Coating Properties and Processes In Our Webinar
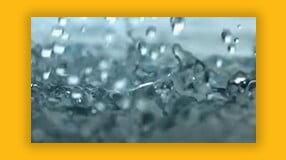
The Difference Between "Hydrophilic and Hydrophobic" Coating Properties
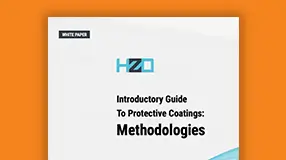
Learn about Protective Coating Methodologies With Our White Paper
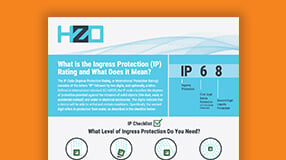