PECVD Coating Services
PECVD coatings are an indispensable technology that has revolutionized numerous industries. PECVD, which stands for Plasma-Enhanced Chemical Vapor Deposition, is a thin film deposition process that creates high-quality coatings with remarkable versatility. HZO offers proprietary PECVD coatings and other PECVD coating services specialized to meet application or industry-specific performance standards.
What are the benefits of HZO PECVD Coatings?
Lightweight & Minimal Thickness
PECVD processes produce extremely thin, highly dense, and pinhole-free coatings.
Cost
The PECVD coating process can require minimal to no masking, driving down cycle time and potential labor costs. Connect-through coatings are possible.
Expanded Potential
PECVD coatings boast more adaptability, allowing for a broader range of substrates that can be coated.
Reliability
PECVD nanocoatings provide resistance against corrosives that can compromise the integrity and function of vital devices.
What is the PECVD Process?
Plasma-Enhanced Chemical Vapor Deposition (PECVD) is a specific variant of chemical vapor deposition (CVD) that utilizes plasma to enhance the deposition process. In PECVD, the precursor gases are energized by an electric field, creating a plasma state. This plasma state enhances the necessary chemical reactions and facilitates the deposition of thin films.
PECVD coatings, in particular, offer unique attributes due to the plasma-enhanced process. These coatings exhibit excellent adhesion, uniformity, and precise control over film thickness. PECVD coatings find applications in various industries, including semiconductors, solar cells, and optical coatings.
The PECVD coating process can vary depending on chemistry, equipment, and desired properties. PECVD processes are complex and require careful control of multiple parameters to achieve the desired film quality and characteristics.
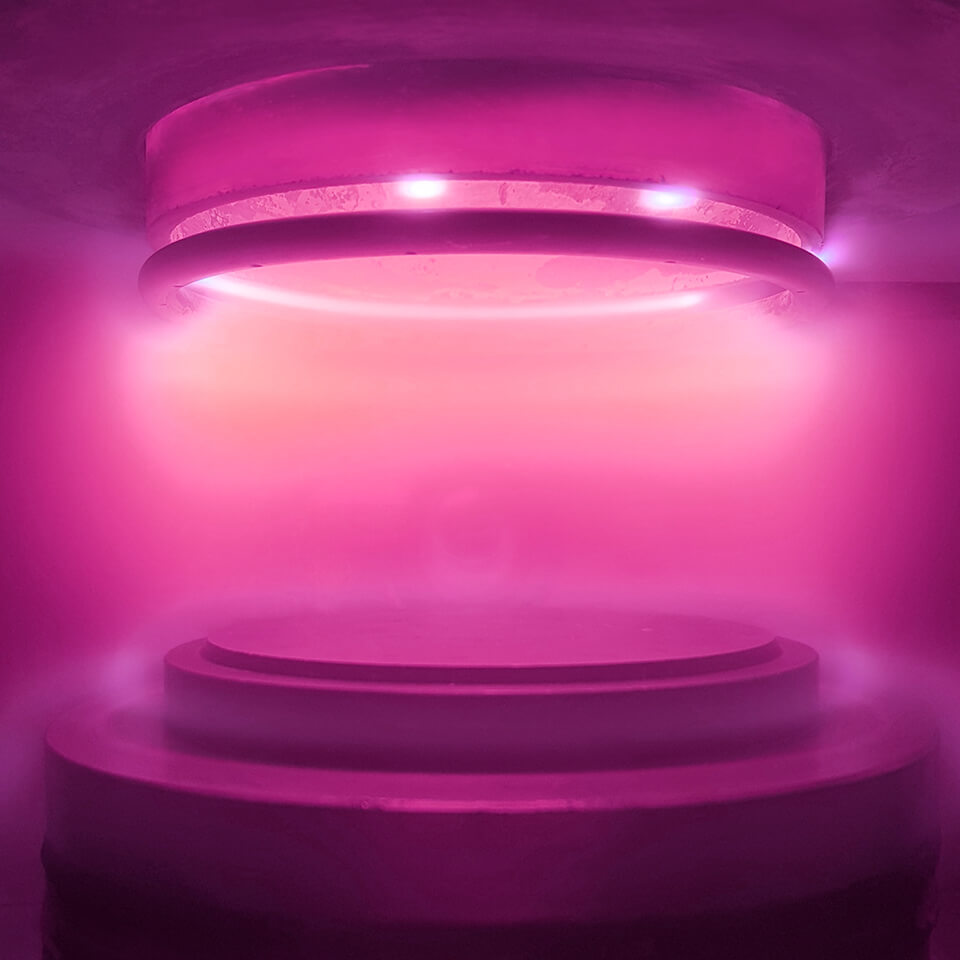
PECVD Process At A Glance
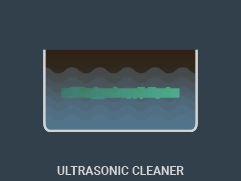
Preparation
The substrate is cleaned of contaminants with solvent, ultrasonic, or plasma cleaning methods, and then loaded into the PECVD chamber by an HZO technician for secure positioning.
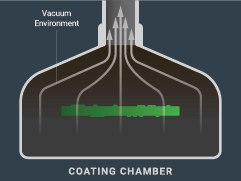
Pump Down
The chamber is evacuated to create a vacuum environment. The pressure is lowered to minimize unwanted reactions and impurities during the coating process.
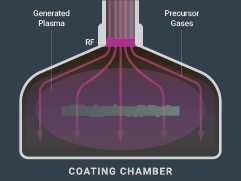
Plasma Generation
Precursors are introduced and energized to create a plasma that breaks the precursors into radicals and ions for chemical reactions necessary for film deposition.

Film Deposition
The plasma's reactive species bond with the substrate, chemically forming a thin material layer through attraction and bonding.
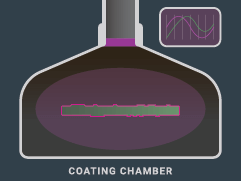
Control & Monitoring
HZO technicians control and monitor gas flow, pressure, temperature, and RF power to ensure a consistent deposition process for the desired film.
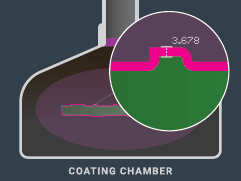
Thickness and Uniformity
Deposition continues until achieving the desired thickness, depending on precursor concentration, pressure, and energy, with process optimization ensuring uniform substrate coverage.
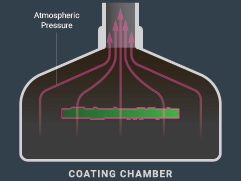
Completion
After coating, plasma and precursors cease and the chamber is neutralized to atmospheric pressure for substrate removal.
Coating Properties
-
Adheres to a variety of substrates, including plastic and metal
-
No additional curing or post-processing required after deposition
-
Dense, pinhole free coatings
-
Adheres to a variety of substrates, including plastic and metal
-
Low dielectric constant
-
Halogen-free variety is available
-
V0 Rating in Flammability per UL94
-
Provides protection against wide range of known harsh environments
-
Free of solvents, residues, and catalysts
-
Minimal coating thickness for improved thermal management and weight
-
Multiple chemistries can be used in series for more robust protection
-
Single layer or multilayer chemistry adds to versatility of choices
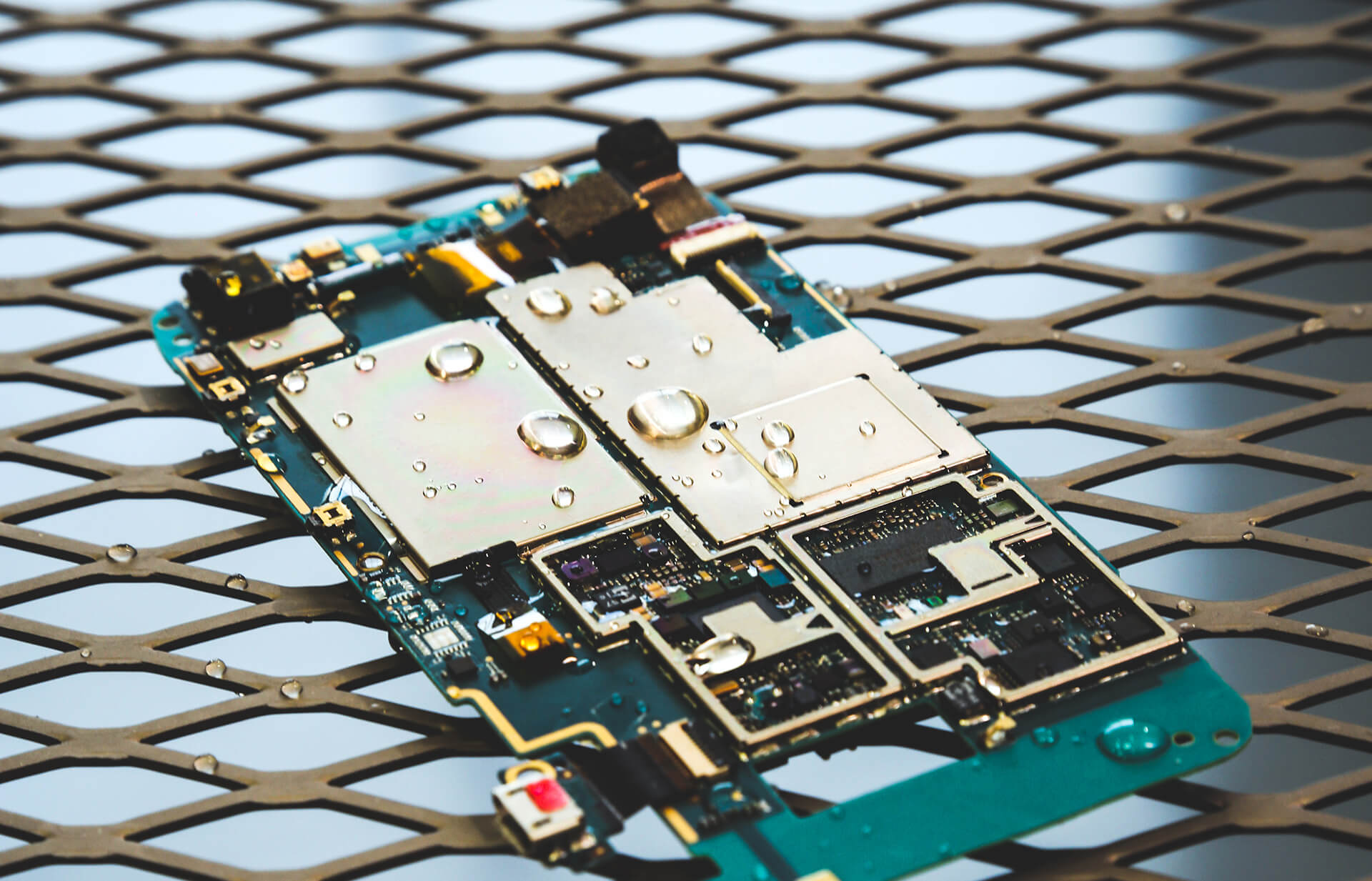
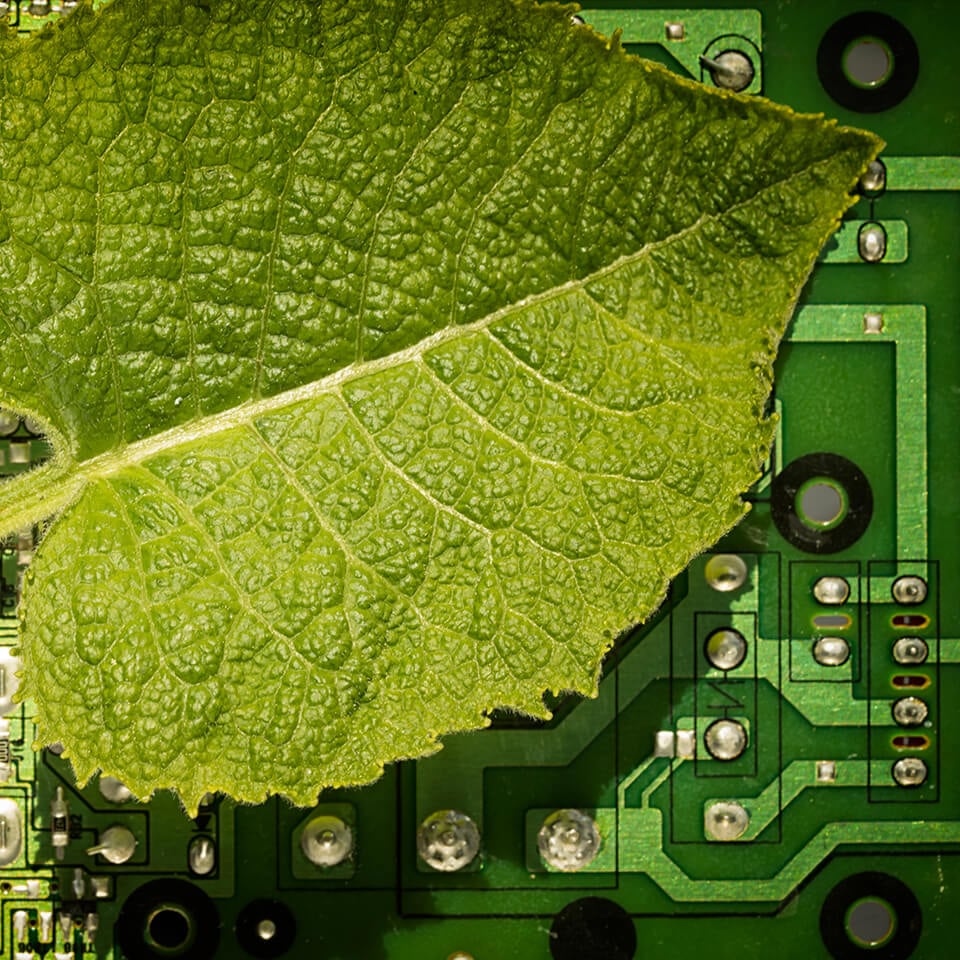
Meets Sustainability Regulations
There are no initiators or catalysts in our PECVD polymerization process. Therefore our plasma coatings are free from trace ionic impurities and are also REACH, RoHS, and California (CA) Proposition 65 compliant. PFOA/PFOS-free and halogen-free options are available.
-
Minimized cost and labor
-
Oleophobic (oil-repellant)
-
Hydrophobic (water-repellant)
-
Halogen-free varieties available
Are HZO Protection
Solutions Right for You?
Additional Resources
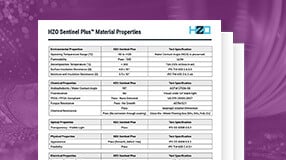
Download HZO's Sentinel Plus™ Nanocoating Material Properties Datasheet
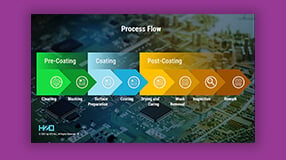
Learn How To Incorporate Conformal Coating Into Your Manufacturing Process
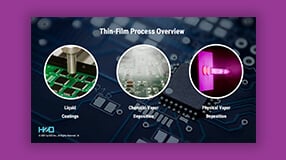
Learn About the Thin Film Coating Properties and Processes In Our Webinar
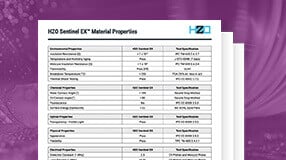
Download HZO Sentinel EX™ Nanocoating Material Properties Datasheet
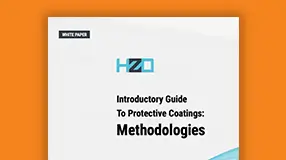