Conformal Coating for Drones - Which is Best?
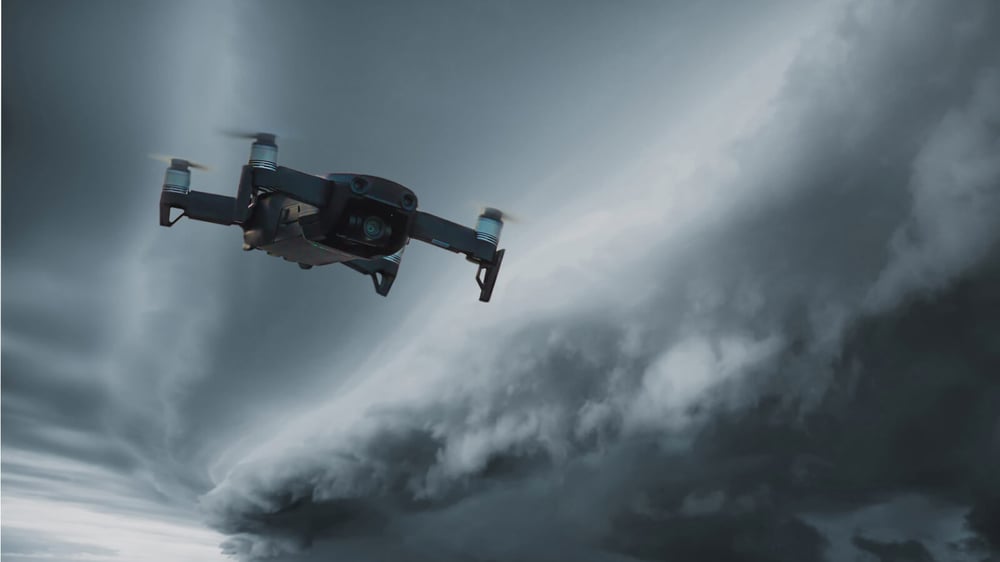
As technology advances, so do the capabilities of drones, which are available in various sizes, weights, and shapes. The technological advancements in drone specifications, mapping software, cameras, and sensory applications are expanding how different markets use these remote-controlled flying devices, increasing their prevalence.
As such, there is a growing need to improve operational endurance in harsh weather conditions and enable longer missions in unpredictable environments, as sensors within the drones that measure atmospheric parameters and gas concentrations must safely and reliably function. For example, drones operating in underground mines must be waterproof, dustproof, and shockproof and resist pressure, temperature, and humidity. Conformal coatings can meet these requirements if applied and chosen correctly.
To choose which conformal coating is best as you design drones, you will need a thorough understanding of the application environment and associated electronic reliability challenges. You must also understand the properties of each conformal coating material to determine if these properties will meet your application requirements.
Although you may not plan on considering Parylene due to perceived challenges with scalability or cost, it may be the best conformal coating for your project. The film has long been used in the aerospace industry for its exceptional properties that significantly increase electronic reliability within aircraft.
Beneficial Parylene Coating Properties for Drones
Thinner and Lighter
The coating weight you choose can be critical to battery life, with lighter films increasing your drone’s lifespan. HZO Parylene coatings have passed IPC CC-830C tests at 50% thinness of other conformal coatings, proving the coatings can provide as much, if not more, insulation flexibility, flammability, thermal shock, dielectric withstanding voltage, and moisture resistance at a fraction of the weight and mass of alternatives.
Excellent Conformality, Pinhole, and Defect-free
Parylene coatings are ultra-thin, lightweight, and due to the chemical vapor deposition (CVD) application process, the thin films are highly conformal, wrapping around every edge available. The vapor deposition process is performed under vacuum, with specialized equipment, including a coating chamber. As a result, all surfaces are coated evenly with the same thickness all around the objects being coated. This vapor phase coating process also leads to pinhole-free coverage free from defects.
Download a drone brochure
Beneficial Parylene Conformal Coating Barrier Properties for Drones
As aircraft that need to withstand more extreme temperature and pressure conditions encountered in aerospace applications, drones can benefit from Parylene’s impressive barrier properties, particularly those that protect electronics from the repercussions of corrosion.
Water vapor transmission rate (WVTR) and gas permeability indicate barrier effectiveness for corrosion resistance. The chart illustrates that Parylene C’s WVTR and gas permeability properties are remarkably low.
Table: Barrier Properties of Conformal Coatings
Polymer | Gas Permeability at 25 °C, (cc·mm)/(m2·day·atm) | WVTR,(g·mm)/(m2·day) | ||||||
---|---|---|---|---|---|---|---|---|
N2 | O2 | CO2 | H2 | H2S | SO2 | CI2 | ||
Parylene C | 0.4 | 2.8 | 3.0 | 43.3 | 5.1 | 4.3 | 0.1 | 0.08 |
Parylene N | 3.0 | 15.4 | 84.3 | 212.6 | 313 | 745 | 29.2 | 0.59 |
Parylene F (VT-4) | – | 16.7 | – | – | – | – | – | 0.28 |
Epoxy (ER) | 1.6 | 4 | 3.1 | 43.3 | – | – | – | 0.94 |
Polyurethane (UR) | 31.5 | 78.7 | 1,181 | – | – | – | – | 0.93 |
Silicone (SR) | – | 19,685 | 118,110 | 17,710 | – | – | – | – |
Download the HZO Parylene datasheet to find out more about Parylene Properties
Read an in-depth discussion of Parylene properties here
HZO Parylene Conformal Coatings for Drones
Although Parylene’s coating properties present an ideal solution to drone reliability design challenges, it has historically been used in mission-critical scenarios, such as military applications or medical implants. However, as drones become more capable and critical across markets, can you afford to compromise on your conformal coating?
Learn about all of our thin film application areas, including medical device coatings, IoT, consumer electronics, automotive coatings, and industrial coatings.
HZO is a coating supplier that makes Parylene more scalable and cost-efficient through proprietary equipment and processes. If you desire the level of reliability that Parylene can provide but are unsure if it will fit within your budget or business model, please reach out to speak to one of our Applications Engineers. Our team can evaluate your project, determine if Parylene is a suitable solution, and advise how to move forward.
Solving Weather & Water Challenges For Smart Farms | HZO
Improving CGM Electronics Designs with Medical Coatings
Parylene Conformal Coatings - Parylene Conformality Explained
Mallory is a veteran writer with over a decade of writing experience and has spent over five years at HZO learning about coating technology from the best minds in the industry. Professionally, Mallory is especially interested in the process of problem-solving and watching how the engineering team develops solutions that ensure business requirements are met. Over her years at HZO, Mallory's writing has been cited in industry whitepapers, including "Parabolic Model for Optimum Dry Film Thickness (DFT) of Corrosion Protective Coatings" and "Universal Approach to Integrating Reduced Graphene Oxide into Polymer Electronics." All of Mallory’s blogs are reviewed for accuracy before publication.
Additional Resources
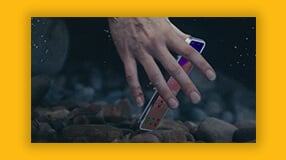
Learn More About the Benefits of Protective Consumer Electronics Coatings
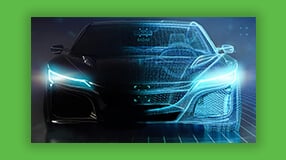
Learn About the Benefits of Protective Automotive Coatings
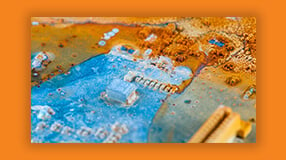
Learn About the Benefits of Protective Industrial Coatings
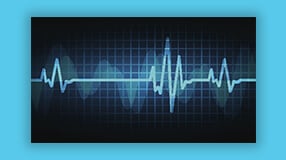
Learn About the Benefits of Protective Medical Device Coatings
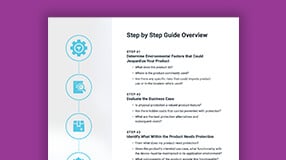