Conformal Coating Types:
Resources and Guide to Get Started
What Are Conformal Coatings?
The global electronic components market was valued at $363.93 billion in 2023 and is projected to grow to $847.88 billion by 2032. With electronic usage on the rise, what will protect these devices from the severe conditions in which they are used? Conformal coatings.
Conformal coatings are materials that insulate and protect electronics from harsh environments. There are five types to consider: acrylic, silicone, epoxy, urethane, and Parylene. Choosing the correct coating is critical. Each has different properties, benefits, and drawbacks. The material you choose will affect many aspects of the coating process and, thus, the manufacturing process.
This guide on conformal coatings helps you choose the best type for your needs. It gives an overview of each material and associated processes.
Click here for additional conformal coating resources
How Do I Choose the Best Conformal Coating for my PCB?
As you read this guide, keep the following questions in mind:
- What environmental threats will be in the operating environment?
- What type of conformal coating standards does the material need to meet?
- Is a particular conformal coating thickness required in the project specifications?
- Are simplicity and cost priorities, or is reliability most important? Is it a combination?
These answers will give you the context you need. They will help you choose the best coating for your project.
Conformal Coating Types - An Overview
Each type has a unique chemical composition that leads to distinct coating properties. The coating materials vary in cost, which can affect your choice in the application process. Additionally, a coating's properties can involve procedures such as removal or repair. For example, a robust, chemical-resistant coating may be harder to remove. Below, we summarize each coating type.
Why Use Acrylic Conformal Coating?
Acrylic films are usually the easiest to apply and work with. Acrylic removal involves a simple process. These coatings are robust, cheap, and transparent. They protect against moisture, fungi, acids, bases, and electricity.
Notable Acrylic Coating Properties
- Clear protective coating
- Relatively short drying times
- Good electrical and physical properties
- Low moisture absorption
Acrylics are one of the simplest conformal coating types to apply, and the films dry quickly. Application methods include brush, spray, and dipping. Acrylics are a good choice for low-cost, quick applications. Their coating process is simple and allows for cheaper application methods.
Watch our on-demand webinar about incorporating conformal coatings into your manufacturing process:
Why Use Silicone Conformal Coating?
Silicone films protect components. They can absorb shock and vibration, relieving parts from physical stress. Silicones excel in extreme temperatures. They are stable at -65°C to 200°C, resisting ultraviolet and ozone degradation.
Notable Silicone Coating Properties
- Good humidity and moisture resistance
- Low toxicity
- Easy to apply
- Easy to repair
Silicone can be applied with dipping and spraying methods or simple flow coating. It is easy to repair, and its excellent heat cycling makes it suitable for automotive, aerospace, and industrial uses. However, moisture may permeate through the coatings, and they can exhibit poor mechanical strength.
Download a technical paper about coating methods:
Why Use Epoxy Conformal Coating?
Epoxy coatings protect against abrasion, corrosion, harsh chemicals, oil, and thermal shock. They also serve various other purposes. For example, thermally conductive epoxy protects circuit boards with heat-generating components. Meanwhile, flame-retardant epoxy is helpful for fire hazard protection.
Notable Epoxy Coating Properties
- Very robust, difficult to remove
- Excellent chemical and abrasion resistance
- Very rigid conformal coating
- High dielectric strength
Epoxies are easily applied and may be a two-part compound or a single compound to be cured with UV or heat exposure. Dip-coating, brushing, or spray methods are suitable for epoxy application. Film shrinkage may occur during polymerization. This can cause issues during coating. The toughness of epoxy may damage products if rework is needed.
Why Use Urethane Conformal Coating?
Urethane, or polyurethane, is a conformal coating that makes tough, hard coatings. They resist solvents and abrasion. These sturdy films block airborne contaminants. They may help reduce tin whisker growth.
Notable Polyurethane Coating Properties
- Moisture and oil-resistant
- Fungicidal
- Good flexibility
- Class F temperature rating (160°C/320°F)
Urethane films can be applied by dipping, spraying, or brushing. Curing is required to complete the coating after application. Curing may take an hour to several days. This adds another step to the polyurethane coating process.
Why Use Parylene Coatings?
Parylene coatings are transparent, biocompatible barriers. They resist corrosion and are thinner than other coatings. Parylene's properties make it ideal for mission-critical applications.
Notable Parylene Coating Properties
- Biocompatible, biostable, “green polymer”
- Insoluble to common chemicals and conditions
- High dielectric strength
- Dry film lubricity
Parylene Coating Vs. Conformal Coating
Parylene, unlike acrylics and other coatings, is deposited by chemical vapor deposition (CVD). This vacuum deposition process requires specialized equipment. Its limited capacity may raise costs and production times. Also, the CVD method of Parylene coats anything it touches in the chamber. This typically requires a masking process.
On the other hand, Parylene films do not require curing. Unlike other coating methods, the CVD process has no VOCs, solvents, catalysts, or waste. If reliability is a priority over cost and efficiency, Parylene is a good choice. You can also find Parylene coating suppliers specializing in low-cost, mass production, like HZO.
Acrylic (AR) Coating Properties | Epoxy (ER) Coating Properties | Silicone (SR) Coating Properties | Urethane (UR) Coating Properties | Parylene (XY) Coating Properties |
---|---|---|---|---|
Low moisture absorption | Very robust | Good humidity and moisture resistance | Moisture and oil resistant | Biostable and biocompatible |
Relatively short drying times | Excellent chemical and abrasion resistance | Low toxicity | Fungicidal | Excellent chemical resistance |
Clear protective coating | Very rigid conformal coating | Easy to apply | Good flexibility | Superior conformality |
Good electrical and physical properties | High dielectric strength | Easy to repair | Can be thinned to achieve a chosen viscosity | Exceptional corrosion resistance |
Typically brushed, sprayed, or dipped | Typically brushed, sprayed, or dipped | Typically brushed, sprayed, or dipped | Typically brushed, sprayed, or dipped | Applied by chemical vapor deposition (CVD) |
How to Choose a Conformal Coating Method
If you have chosen your material, the next step is to select from the available application methods.
To choose the best coating method, consider:
- Throughput requirements
- Required performance
- Capital investment
- The complexity of the substrate to be coated
The most popular coating methods are summarized below.
Brush Coating for PCBs
Brush coating is the easiest and cheapest application method and requires minimal maintenance. Equipment is inexpensive. There may be less need for masking due to the controlled nature of this technique. However, the quality and results of the brush conformal coating depend on the operator and tools. So, they may vary in quality and conformability. Contamination issues may also be a concern.
Brush Coating Advantage |
---|
Straightforward and low startup costs
|
Suitable for low-volume, high-mix production
|
Suitable for rework or touchup application
|
Can protect against airborne FOD
|
Very good for small parts where masking needs are challenging
|
Brush Coating Disadvantage |
---|
Difficult to control the material thickness
|
Easy to create voids and bubbles
|
The brush can be the cause of residual FOD (bristles)
|
Operator experience dependent
|
Part to part variability
|
Spray Coating Application for PCB
The spray coating technique can be manual or automated and is faster than brush coating. Spraying can give consistent results if it combines the right settings including pattern, solvent dilution, and nozzle pressure. Yet, PCB spray methods can entail more masking time than brushing methods. Spraying is cheaper than other methods, but needs humidity and temperature control, which can raise startup costs.
Spray Coating Advantage |
---|
System is not complicated
|
Reasonable implementation costs
|
Aerosol is suitable for rework
|
Angled spray may provide a better coating on high topography assemblies
|
Spray Coating Disadvantage |
---|
Need to contain excess over-spray or any harmful vapors
|
Material wastage/loss in the process
|
Usually much higher in VOCs as dilution is needed for spray
|
Thin material may require multiple coat/cure cycles to get desired thickness
|
Dip Coating
Dipping, like spraying, may be automated or manual. It is an effective way to coat components that are not too irregular or bulky in shape. The dip coating method fully encapsulates electronics. It is an efficient, low-cost process for high-volume applications. With proper implementation, dipping produces repeatable film thickness and uniform coverage. But, to avoid contamination, the material in the coating dipping machine must be purged and replaced periodically, increasing cost and complexity.
Dip Coating Advantage |
---|
System not complicated
|
Relatively not expensive
|
Reused material/process savings
|
Dip Coating Disadvantage |
---|
Open to environmental impacts – temperature/humidity
|
Material viscosity must be monitored
|
Coating reservoir can become contaminated
|
Chemical Vapor Deposition (CVD)
Of the listed coatings, CVD is used only with Parylene. The CVD process is done under vacuum. It uses specialized equipment, including a coating chamber. All surfaces can be coated evenly, no matter the chamber position. The coating deposits the same relative thickness on the objects. This vapor phase coating process also leads to pinhole-free coatings that are absent of defects. Masking and demasking are typically required, but no curing is necessary.
Chemical Vapor Deposition (CVD) Advantage |
---|
Uniform coverage on all surfaces
|
Excellent material properties
|
No harmful vapors during process
|
Chemical Vapor Deposition (CVD) Disadvantage |
---|
Batch-mode
|
Material/equipment can be expensive
|
Requires specific processes for rework
|
The conformal coating you choose will also affect other parts of the coating process. We have included an overview of many of these processes for a holistic understanding.
Conformal Coating Thickness Measurement
Coating material impacts thickness due to different material properties. For example, Parylene can pass IPC CC-830C at 50% of other coatings' thickness. Other coatings must be thicker to meet the standards. Accurately meeting the requisite thickness is crucial. If the coating is too thin, components remain vulnerable to the environment. But, if it is too thick, the insulating properties of the coating may render specific parts non-functional.
How to Measure Conformal Coating Thickness:
Several methods measure conformal coating thickness, including:
-
Manual measurement
-
Measuring wet coating with a coating thickness gauge
-
Measuring dry coating with calipers to measure the PCB before and after coating
Conformal Coating Inspection
After the coating, inspect the components. Check for customer and coating standards. The conformal coating type may affect the inspection process. Different materials may be used to meet various standards and thicknesses. They may also need to meet different reliability levels.
Read the IPC A 610 standards for conformal coating inspection here.
Conformal Coating Masking and Demasking
Masking prevents coatings on components that must remain uncoated to function. For example, connectors. Successful masking requires: selecting the right materials, tailoring the masking process to the coating application, and using the best techniques. After the coating is done, the masking is removed. This is the demasking process. Masking and demasking can be more complex and critical with certain coating materials. Additionally, some application methods require more masking and demasking time than others. Thus, the best masking processes are tailored to the material.
Conformal Coating Removal
Sometimes, the coating must be reworked due to poor adhesion, bad materials, repairs, or other reasons. Removal can add cost and complexity to the coating process. The type of coating you choose will affect the best removal methods.
Techniques include:
-
Peeling
-
Chemical Solvent
-
Grinding and Scraping
-
Thermal
-
Micro Sandblaster
Conformal Coating Cure
Conformal coating curing cross-links the film to give it peak properties. Curing is different from conformal coating drying. The latter means the coated component can be handled. Coating types require different drying and curing methods, with one exception. Due to its CVD coating process, Parylene does not require drying or curing.
Methods include:
-
Moisture
-
Conformal coating UV cure
-
Oxidative
-
Heat
-
Catalytic cure mechanisms
-
Condensation
Conclusion
This guide has covered the basics you need to get started with conformal coatings. But, it has only scratched the surface of all you must know. We recommend “Coating Materials for Electronic Applications: Polymers, Processing, Reliability, Testing (Materials and Processes for Electronic Applications,” written by James Licari as an excellent in-depth resource. It is an excellent, in-depth resource. Also, you can browse our resource center. You can read more, download a technical paper, or listen to an on-demand webinar by one of our engineers about coatings.
Additional Resources
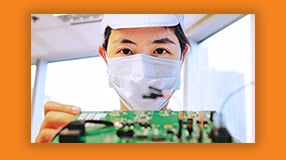
Which is Better For Your Application? Conformal Coating or Potting?
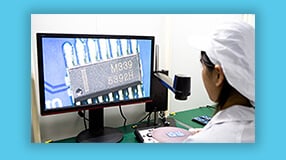
Learn About Common Conformal Coating Defects And How To Fix Them
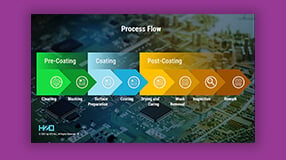
Learn How To Incorporate Conformal Coating Into Your Manufacturing Process
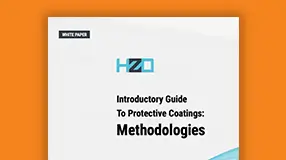