Parylene Coating Process Explained:
How it Works, Variables, Illustrations, Pros & Cons
Increase Electronics Reliability, Performance, and Lifetime in Numerous Applications with a Parylene Coating
Read more about Parylene coating properties.
Meanwhile, other favorable properties (such as high purity, defect and pinhole-free films, and excellent conformality) result from the Parylene coating method.
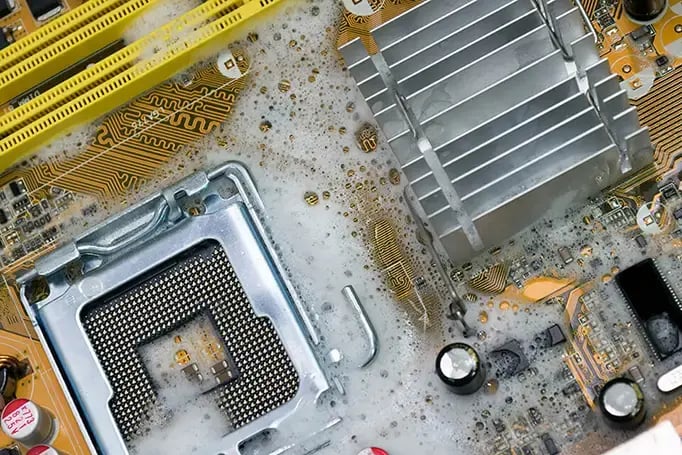
Understanding the Parylene Deposition Process
Parylene is applied with chemical vapor deposition (CVD). When used for Parylene deposition, CVD converts dimer (raw Parylene coating material in powder form) into a gas that deposits onto components, forming coatings that provide excellent corrosion, barrier, and insulation protection. The Parylene chemical vapor deposition process is summarized as follows:
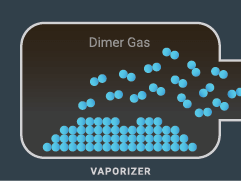
Dimer is loaded into a vacuum chamber to sublimate into a gas without transitioning into a liquid state.
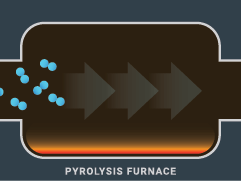
After sublimation, the dimer gas passes through to the next stage of the deposition process by flowing through a pyrolysis chamber.
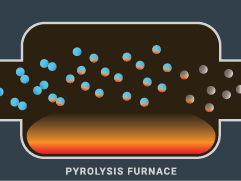
The gas will be heated to a temperature range of 500 to 700° C to split the dimer molecules and create a monomer vapor.
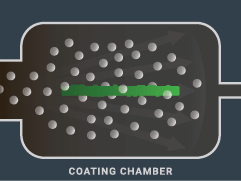
The monomer vapor is then drawn into a depressurized chamber, creating a vacuum.
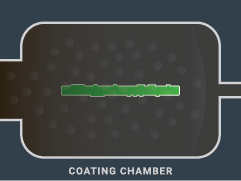
The chamber, held at room temperature, polymerizes the monomer vapor, conformally coating all surfaces it lands on, including edges, crevices, and other topography.
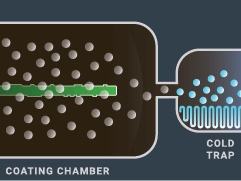
The vacuum pump that draws the Parylene vapor into the deposition chamber also pulls the gas exiting the chamber into a cold trap.
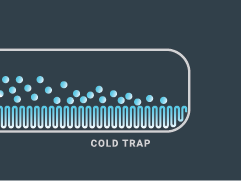
This cold trap will solidify the Parylene for proper disposal.
Parylene N Chemical Change Process
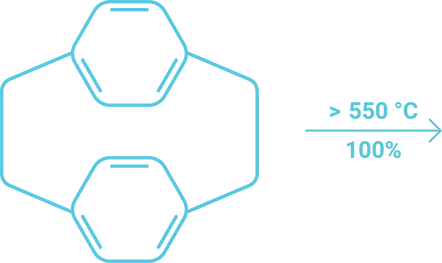
di-para-xylylene
(dimer)
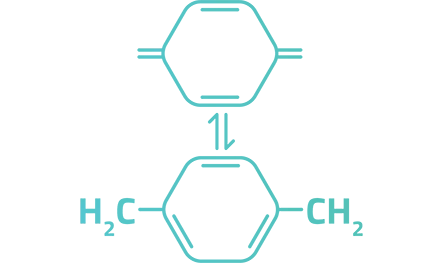
para-xylylene
(monomer)
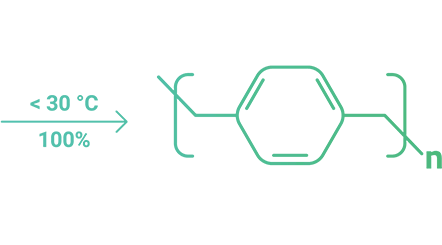
poly(para-xylylene)
(polymer)
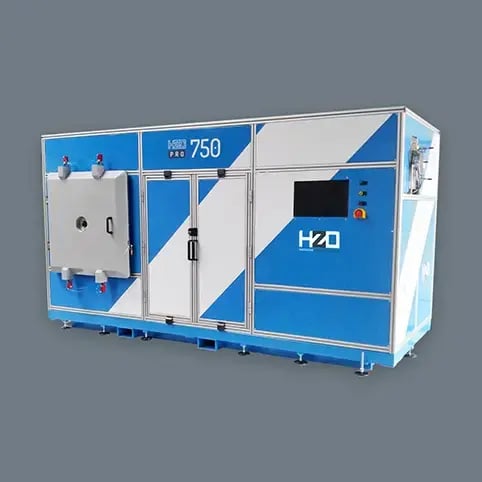
Parylene deposition equipment is critical to any Parylene coating process
Time to consider throughput, chamber size, and footprint.
Parylene Coating Process Overview
Several processes before and after the Parylene coating application are required to complete the film deposition. A general overview of some of these processes is below:
Cleanliness
Parylene coatings keep corrosive elements from degrading the performance of your electronics. If you're targeting PCBA longevity and reliability, it's essential to make sure your boards are clean and dry before you apply any coating. This goes for all coating types, but it's particularly true for vacuum-deposited Parylene coatings.
If you're going to put a high-end coating on your product, you want it to last. Cleaning is the first step to this. The most common types of contamination are fingerprint oils, salts, flux residue, tape, or adhesive residue. These contaminants are introduced through transportation, handling, storage, and the manufacturing of the PCBA itself.
Cleaning and drying the parts prior to coating accomplishes three things: It improves coating adhesion, makes the product more reliable, and extends the device's lifetime. With your PCBs, target performance will determine what level of cleaning you need to do.
The cleaning materials and processes that could be used include aqueous washing, ultrasonic agitation, and vapor degreasers. You can even use simple isopropanol or IPA wipes. It really depends on what level of reliability you're going for, how long you need your device to last, what you're going to expose it to, and just how dirty your manufacturing process is in the first place.
Surface Preparation
Even with conventional cleaning, adhesion may still be an issue with some substrates. After conventional cleaning, treatment with an argon and oxygen plasma mixture may be necessary to have the argon plasma “roughen up” the surface so adhesion promoters can chemically bond.
Adhesion Promotion
Without adhesion promotion, Parylene relies solely on its ability to wrap around features physically, so a Parylene adhesion promoter is often helpful. With adhesion promotion, the coating connects chemically to the product.
Masking
Parylene molecules penetrate any surface area accessible to air during the CVD process. Therefore, all coating keep-out areas must resist Parylene coating application, which requires domain expertise to identify factors that affect masking success. These include masking materials, different areas to be coated, the Parylene type, proper timing, and managing electrostatic discharge.
Our engineers create custom masking plans for electronic products of all shapes, sizes, and functions. Additionally, our masking equipment can automate and semi-automate the process for larger productions.
Demasking
Removing masking materials is as complex as selecting the proper masking method. That said, it is critical to identify potential process improvements and provide training consistently. Tools and techniques, such as automated inspection, ablation, laser scoring, and strain gauge testing, mitigate touchpoints and optimize processes.
As with masking, HZO can use automated demasking for high-volume applications to increase throughput.
Parylene Coating Inspection
After coating, parts should be inspected to confirm they meet project requirements. These may include transmittance and thickness of the Parylene coating measurements, adhesion testing, and cracks in the coatings.
We inspect for component damage and “critical to quality items” at the incoming and outgoing stages and conduct interim inspections to ensure good masking performance.
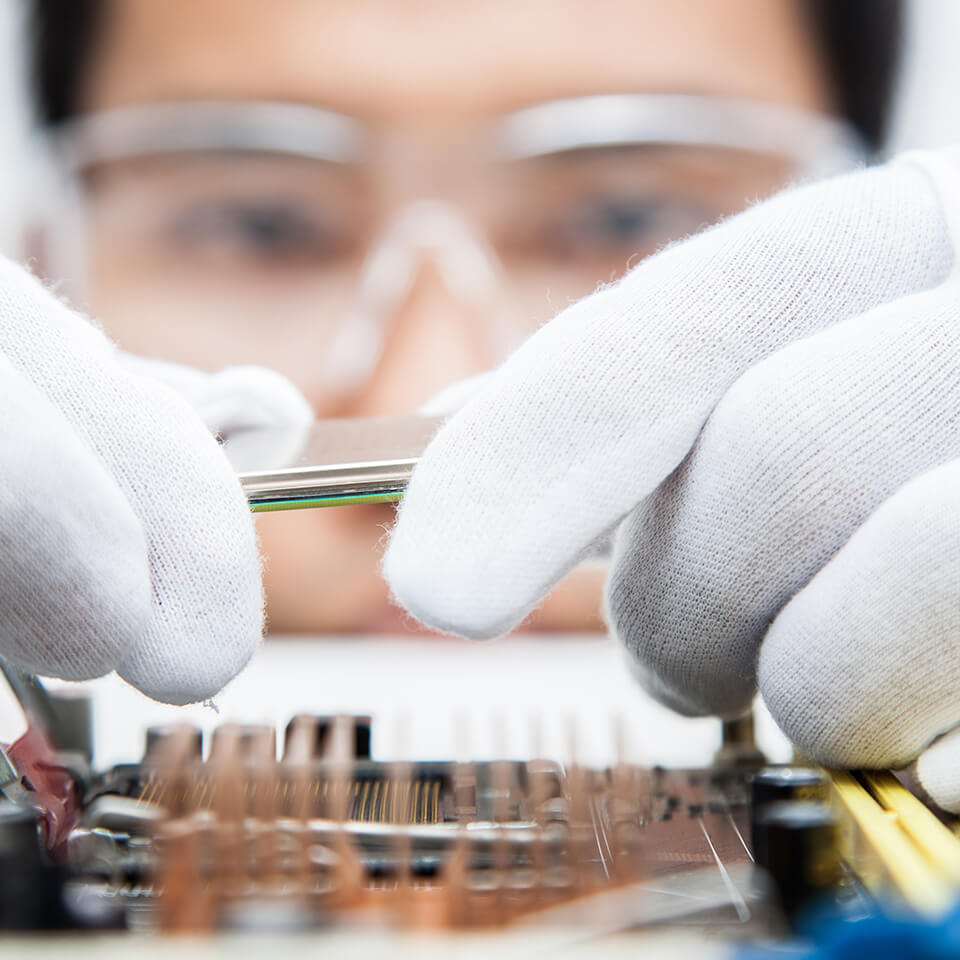
Speak to an Engineer About Parylene
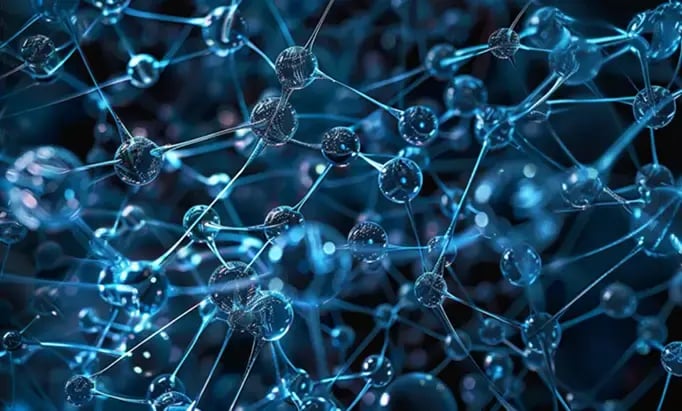
Challenges in the Parylene Coating Process
Delamination
Although chemical vapor deposition is a highly repeatable process that minimizes defects, problems such as Parylene coating delamination may arise with improper implementation.
Rework
Because of the film’s exceptional material properties and chemical resistance, Parylene coating rework and removal can be a struggle. Enlisting a knowledgeable partner to suggest techniques and tools to make rework easier is often necessary.
Long Run Times
Another Parylene coating disadvantage is that CVD is a batch process that can sometimes entail long run times.
How long does Parylene Coating Take?
The answer is that it depends. Parylene types have unique chemical compositions that affect the deposition process. For example, Parylene N deposits more slowly than Parylene C. Additionally, D deposits faster than C, but it can be more challenging to control uniformity within the coating chamber. Parylene film thickness is another variable. Thinner coatings entail shorter coating times.
There are multiple issues to balance when trying to speed the Parylene deposition rate, such as:
- Increasing the deposition rate
- Decreasing the coating time
- Ensuring coating thickness uniformity throughout the chamber
- Ensuring coating quality throughout the chamber
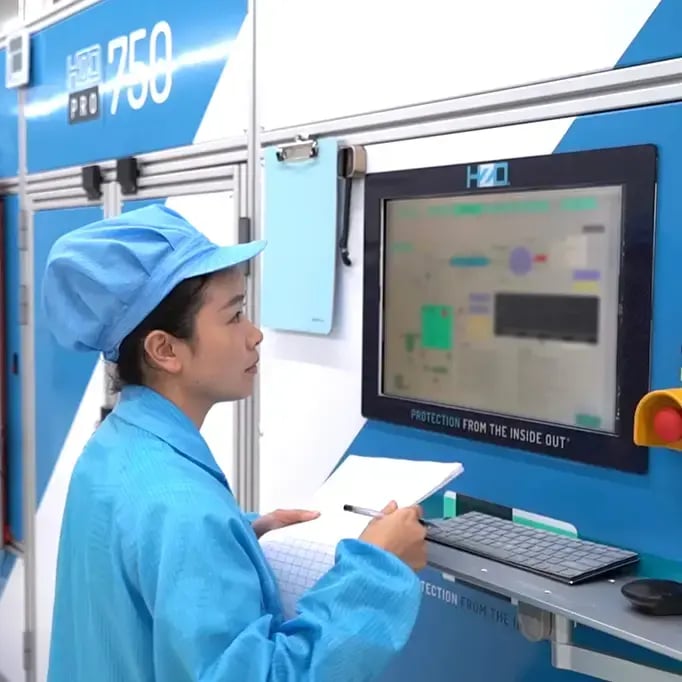
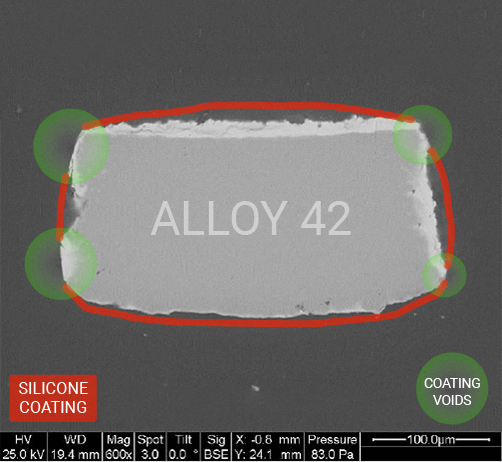
Silicone
Machine Spray Method
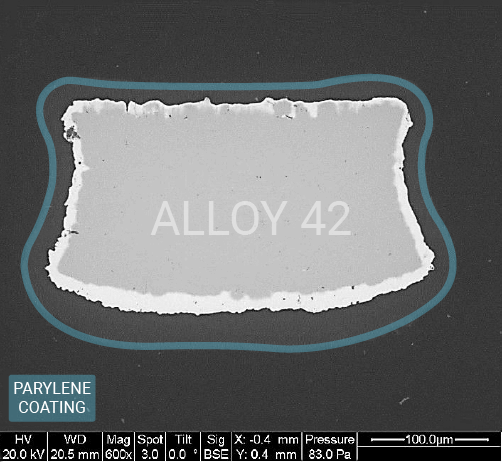
Parylene
Vacuum Deposition Method
Courtesy of CALCE, University of Maryland
Parylene CVD Advantages
Because Parylene deposits as a vapor that wraps around components, even at tight corners, with minimal changes in thickness, ensuring superior coverage compared to traditional conformal coatings.
Silicone coating has been applied in the accompanied image with uneven coverage. The darker surfaces show where the film has settled, while the lighter edges on each of the leads show where it is thinly applied. Parylene is wrapped completely around the part on the right, with even thickness all around.
Parylene Coating with HZO
Despite the many benefits of CVD, the Parylene coating process can present challenges for OEMs who need to ramp up to mass production or cut costs, but this does not have to be the case.
HZO is a Parylene supplier serving all industries with high throughput, turnkey coating solutions that decrease cost and improve quality and speed. Please visit our services page, contact us with questions, or get a quote.
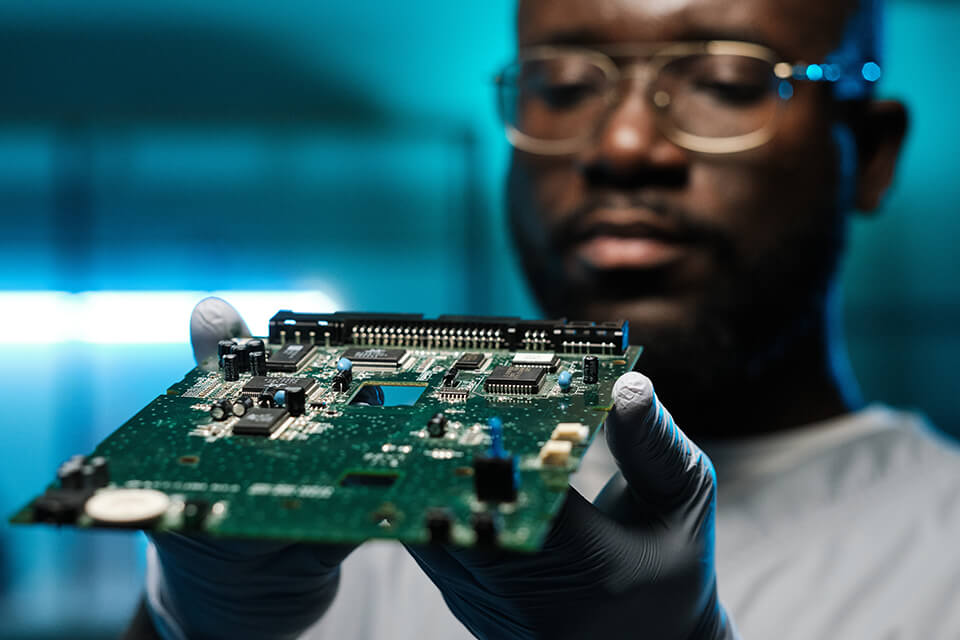
Additional Resources
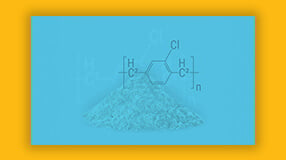
Learn About Parylene Properties With Our Resource Page
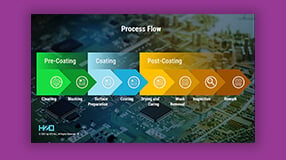
Learn How To Incorporate Conformal Coating Into Your Manufacturing Process
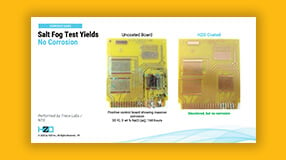
Learn About the Thin Film Coating Properties and Processes In Our Webinar
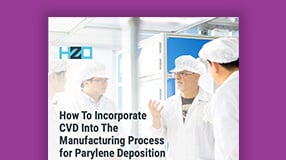
Learn How to Bring Parylene Deposition In-House
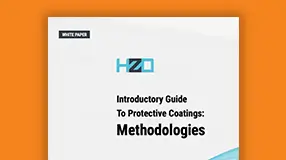