6 Common Conformal Coating Defects & Their Solutions
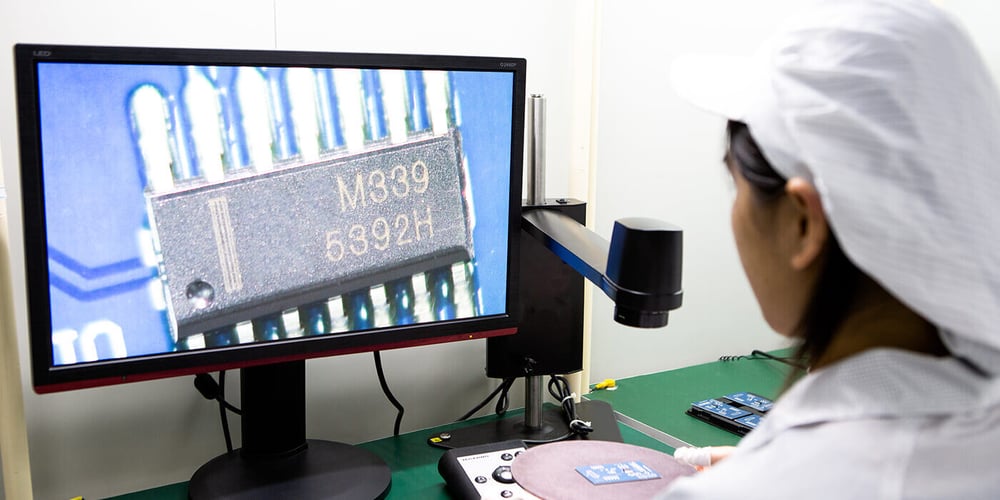
When we say that a chain is only as strong as its weakest link, we aren’t talking about polymer chains – we’re talking about conformal coating defects. Regardless of the type, a single coating defect can affect the long-term reliability of a PCBA or component and must be repaired or removed. This can be costly and labor-intensive.
Therefore, it’s best to avoid defects from occurring in the first place. The following is a list of common defects and how to keep them from cropping up during your conformal coating application.
Learn how to remove conformal coating
The 6 Most Common Conformal Coating Defects and Solutions
Capillary Flow
Capillary flow, also known as scavenging, occurs when a conformal coating migrates from one area of a PCBA to another, leaving behind an inconsistent, uneven finish on the surface.
Common causes for capillary flow include:
- The application of too much coating
- Conformal coating with low viscosity or high surface tension
- Low surface energy of component being coated
To avoid capillary flow from occurring:
- Ensure that the PCBA is entirely clean before coating.
- Use solvent-based coatings instead of water-based, and decrease the use of thinners to increase viscosity.
- Before coating, heat the board to decrease dry time.
Learn more about epoxy conformal coating
Cracking and Ripples
Cracking and ripples can compromise a conformal coating film, exposing a substrate or PCBA to potential contaminants.
Common causes for cracks and ripples include:
- Coating that is too thick
- Thermal shock
- Coating that has been cured too quickly
To avoid cracks and ripples:
- Always apply the coating at an appropriate thickness.
- Allow for extra drying time at room temperature.
- Consider selecting a coating with a broader effective temperature range.
Dewetting
De-wetting is when a conformal coating will not evenly coat the surface to which it is being applied.
Many things cause dewetting, including:
- An uneven coating application
- An improper mixture of two-part materials
- Residue on the coating surface
- Variations in Surface Tension and Surface Energy
To avoid dewetting, thoroughly clean the material being coated before application.
Learn more about polyurethane conformal coating
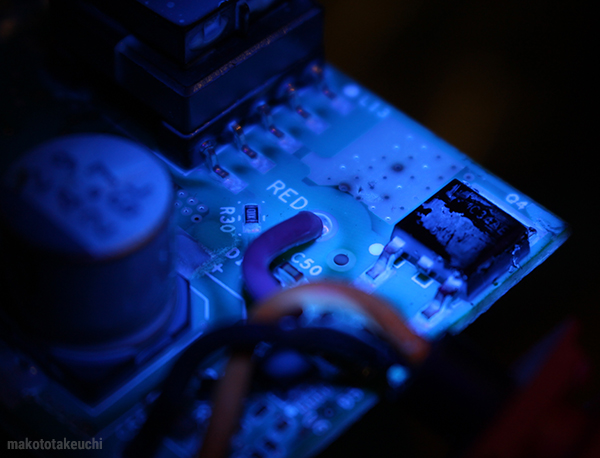
Delamination
Delamination occurs when a coating has lifted away from the substrate. This hinders protection because the area below the coating is left exposed.
Delamination has many causes, including:
- Too thick of a coating
- Coating not adhering to the previous coating layer
- Contamination on the coating surface prevented a good bond to the surface
To prevent delamination:
- Reduce the thickness of the coating.
- Thoroughly clean the substrate before coating.
- Apply a “primer material” that can bond with the substrate and material used for conformal coating.
Orange Peel
Orange peel is when a coating appears dull, resembling the skin of an orange.
It is caused by conditions including:
- A substrate that is too hot
- Improper coating mixture or solvent ratio
- A local environment that is too dry during application
- A second coat has been applied before the first coat is dry
To avoid orange peel:
- Apply coating at the specified thickness.
- Reduce the viscosity of the coating.
Learn more about conformal coating vs potting
Air bubbles, Pinholes, and Foam
Bubbles occur when pockets of air get trapped under a conformal coating layer. Foam is an extreme form of bubbling, and sometimes bubbles burst through the conformal coating, forming a pinhole.
Bubbles, pinholes, and foam happen when:
- A coating is too viscous
- The coating is too thick
- Application equipment has not been setup correctly
To avoid air bubbles, pinholes, and foam:
- Use a lower viscosity conformal coating
- Ensure the coating is applied at the recommended thickness.
- When applying the coating, do so with thin coats.
Why This Doesn’t Happen at HZO
At HZO, we use a conformal coating application method called chemical vapor deposition (CVD) that circumvents these conformal coating issues. Using CVD, we produce uniform, pinhole-free conformal coatings every time. Contact us today to speak to an expert if you want to hear more about our proven technology and processes.
Conformal Coating Removal - How to Get Started W/Reference
Epoxy Conformal Coating Evaluation Guide
Conformal Coating vs Potting/Encapsulation - The Pros & Cons
Mallory is a veteran writer with over a decade of writing experience and has spent over five years at HZO learning about coating technology from the best minds in the industry. Professionally, Mallory is especially interested in the process of problem-solving and watching how the engineering team develops solutions that ensure business requirements are met. Over her years at HZO, Mallory's writing has been cited in industry whitepapers, including "Parabolic Model for Optimum Dry Film Thickness (DFT) of Corrosion Protective Coatings" and "Universal Approach to Integrating Reduced Graphene Oxide into Polymer Electronics." All of Mallory’s blogs are reviewed for accuracy before publication.
Additional Resources
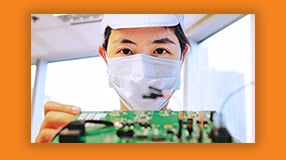
Which is Better For Your Application? Conformal Coating or Potting?
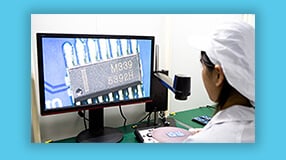
Learn About Common Conformal Coating Defects And How To Fix Them
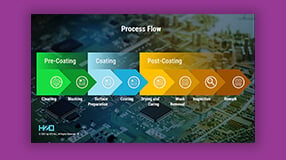
Learn How To Incorporate Conformal Coating Into Your Manufacturing Process
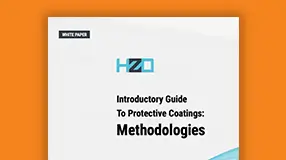