Thin Film Coating Services
Product design is often a struggle to balance multiple goals that can seem conflicting. Reducing time to market, staying within budget, and aligning your products’ form factors with miniaturization trends are vital concerns. Achieving these goals can be a challenge when you must also ruggedize your products to the point that they can operate reliably in harsh conditions. Conformal coatings, particularly Parylene films, applied to circuitry and electronic components can be a solution for protection from harsh environments.
Parylene Conformal Coatings
HZO Guardian™ Series
Parylene is an organic and biocompatible compound that delivers superior protection against all forms of environmental risks. It’s uniquely inert and highly effective at reaching small recesses because of how it forms.
Parylene coating applications take place inside a chemical vapor deposition (CVD) vacuum system, where the products wait inside a room-temperature chamber. After the raw material heats up from a solid to a gas — so much so that the Parylene splits into monomers — the vapors travel to a coating chamber where the molecules cool and polymerize on everything in the chamber. Over time, this builds layers of a polymerized film, microns-thin, and pinhole-free.
Parylene conformal coatings are excellent for applications found in the aerospace, defense, medical device, and industrial products industries. This type of versatility makes it a top choice among OEMs.
Plasma-Based Nanocoatings
HZO Sentinel™ Series
Plasma-based nanocoatings are an ideal choice if you want to protect your electronics from splashes and spills. However, you may want to consider a Parylene coating for complete waterproofing capabilities or to withstand the harshest, most corrosive environments commonly found in industrial settings.
Plasma-based nanocoatings, applied with plasma-enhanced CVD, at micron-thin layers are marginally conformal. Plasma-enhanced CVD works by flowing a precursor gas into the plasma chamber. The gases ionize in an electric field and become plasma, with those ionized materials bonding chemically to the product’s surface and each other to create a barrier. The resulting thickness can range from several nanometers to several micrometers.
Additional Resources
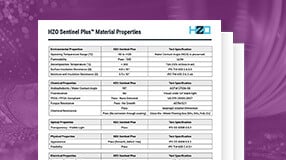
Download HZO's Sentinel Plus™ Nanocoating Material Properties Datasheet
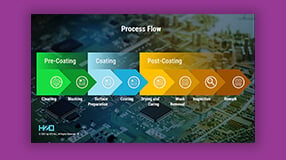
Learn How To Incorporate Conformal Coating Into Your Manufacturing Process
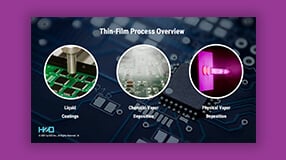
Learn About the Thin Film Coating Properties and Processes In Our Webinar
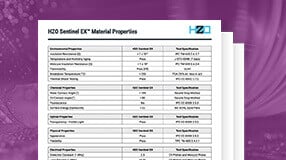
Download HZO Sentinel EX™ Nanocoating Material Properties Datasheet
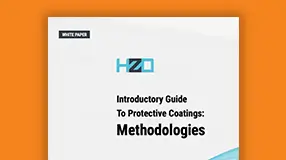