Young's Modulus of Polymers - Measurement, Calculation
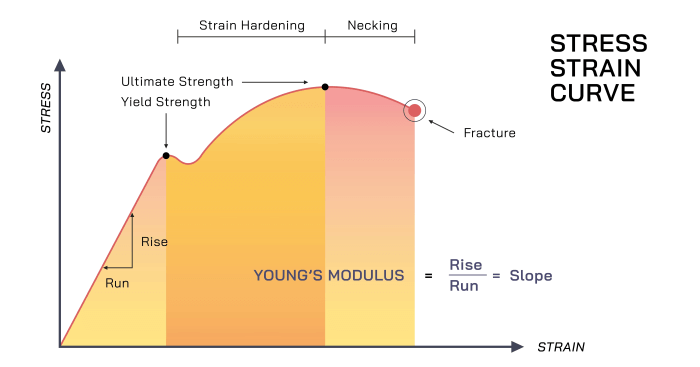
Young's Modulus is an important property, allowing engineers to select coating materials based on their desired stiffness. Understanding and manipulating the elastic Modulus of polymers is crucial for applications where strength, flexibility, or a combination of both is required.
What is Young's Modulus of Polymers?
Young's Modulus, also known as the elastic Modulus, is a fundamental property that characterizes the mechanical behavior of a material. It quantifies the relationship between stress (force per unit area) and strain (deformation) when a material is subjected to an external force or load.
For polymers, Young's Modulus determines how much the material will stretch or compress in response to applied stress. It measures the rigidity of the polymer chain structure. When comparing Young's Modulus between polymers and other materials such as metals and ceramics, polymers typically have lower values. This is because polymers have a more flexible molecular structure, allowing them to undergo more significant elastic deformation under applied stress, in contrast to metals and ceramics with more rigid atomic structures.
Factors Influencing Young's Modulus
Understanding the factors influencing Young's Modulus allows engineers to choose polymer materials with desired mechanical properties for specific applications. The following factors influence Young's Modulus of Polymers:
- Molecular structure and chain flexibility: The arrangement and size of polymer chains determine their flexibility and, consequently, their Young's Modulus. Polymers with longer and more linear chains tend to have higher Young's Modulus values.
- Degree of cross-linking and polymerization: Cross-linking refers to forming chemical bonds between polymer chains, increasing their rigidity and thus increasing Young's Modulus. Higher degrees of cross-linking result in higher Young's Modulus values.
- Temperature and environmental conditions: Young's Modulus of polymers can vary with temperature and environmental conditions. The presence of moisture, for example, can affect the intermolecular forces within the polymer, leading to changes in Young's Modulus.
Measurement and Calculation of Young's Modulus
Measuring and calculating Young's Modulus is crucial to understanding the mechanical behavior of polymers. This value provides valuable insight into how a polymer will respond to applied stress and strain, making it essential in product design.
There are various experimental techniques used to measure Young's Modulus in polymers. These include:
- Tensile testing and stress-strain curves: This technique involves subjecting a polymer sample to tension until it reaches its breaking point. The resulting stress-strain curve provides essential data for determining Young's Modulus.
- Extensional methods: Uniaxial and biaxial extension tests measure Young's Modulus in specific directions. These methods help evaluate the anisotropic nature of polymers.
- Other characterization techniques: Techniques such as nanoindentation and dynamic mechanical analysis can also be employed to measure Young's Modulus in polymers.
Calculation methods for Young's Modulus
Hooke's Law and stress-strain behavior interpretation play vital roles when calculating Young's Modulus:
- Hooke's Law and its application to polymers: Hooke's Law states that the stress applied to a material is directly proportional to the strain it produces. This linear relationship allows for the calculation of Young's Modulus.
- Interpretation of stress-strain behavior and determination of Modulus: By analyzing the stress-strain curve obtained from experimental data, the Modulus can be determined using mathematical methods tailored for polymers.
Role in Material Selection and Design
Young's Modulus helps engineers determine the stiffness and elasticity of polymers. Knowing Young's Modulus values allows them to select the appropriate material for a specific application. The higher the Young's Modulus, the stiffer the material will be, resulting in better resistance to deformation. This stiffness is crucial in applications where the polymer needs to withstand heavy loads or maintain its shape for a long time.
Some examples of how design engineers use Young's Modulus to select materials in different industries are listed below.
- Automotive and aerospace applications: Young's Modulus is essential in designing components such as automotive body parts, airplane wings, and fuselages. It helps engineers ensure the materials can withstand the required forces and maintain their shape during operation.
- Medical and healthcare applications: Young's Modulus is a consideration when developing medical devices, prosthetics, and implants. The Modulus ensures that the materials provide the necessary support, flexibility, and performance for patient safety and comfort.
- Consumer goods and packaging: Young's Modulus comes into play in designing everyday products such as bottles, containers, and packaging materials. It helps determine the polymers' rigidity, flexibility, and impact resistance, ensuring they meet the specific requirements of the intended applications.
- Industrial applications: Engineers can use the measure of stiffness or rigidity of a material to predict how polymers will behave under various conditions common in harsh industrial environments.
Relationship Between Young's Modulus and Product Performance and Durability
Because Young's Modulus directly affects a polymer's behavior under different loads and stresses, engineers can make informed decisions about material selection, design structures that can withstand specific loads, and ensure the safety and reliability of polymer-based products.
The knowledge of Young's Modulus allows for optimizing material properties, such as flexibility and strength, to meet the unique requirements of various industries. Whether in the automotive, aerospace, or medical field, an understanding of Young's Modulus enables the development of innovative solutions that are tailor-made for specific applications.
If you are an engineer involved in product design and would like guidance in selecting a suitable coating material for your application, please contact our team today. Alternatively, if you want to learn more about thin film properties, including elongation yield, elongation at break, or tensile strength at yield, browse our site.
Dielectric Constant of Insulator Materials: Formula, Table of Values
Transparent Polymers - Applications, Material Selection
What is the Index of Refraction? Measurement, Definition & More
Mallory is a veteran writer with over a decade of writing experience and has spent over five years at HZO learning about coating technology from the best minds in the industry. Professionally, Mallory is especially interested in the process of problem-solving and watching how the engineering team develops solutions that ensure business requirements are met. Over her years at HZO, Mallory's writing has been cited in industry whitepapers, including "Parabolic Model for Optimum Dry Film Thickness (DFT) of Corrosion Protective Coatings" and "Universal Approach to Integrating Reduced Graphene Oxide into Polymer Electronics." All of Mallory’s blogs are reviewed for accuracy before publication.
Additional Resources
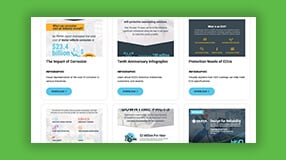
Understand the Capabilities of Thin Film Coatings With Our Resource Page
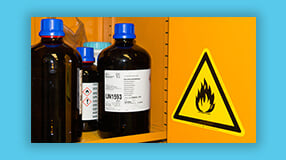
Understand UL94 Rating - Testing, How to Choose a Material, and More
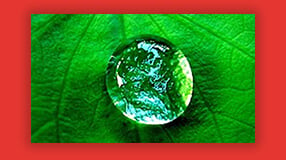
What's the Difference Between Hydrophobic Coatings and Hydrophilic Coatings?
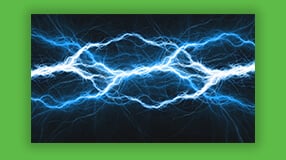
Dielectric Constant of Insulator - Materials, Formula, Table of Values
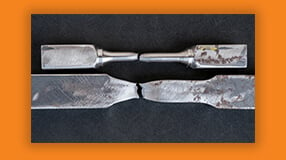
Tensile Strength at Yield - Testing, Definition, Material Selection
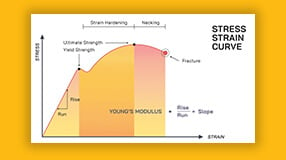
Young's Modulus of Polymers - Measurement, Calculation, Material Selection
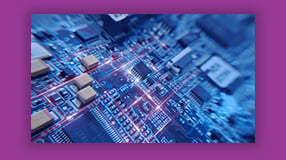
Volume Resistivity - Definition, Measurement, Implications For Product Design
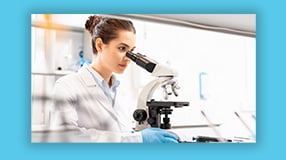
Polymer Glass Transition Temperature – Material Properties, Impact
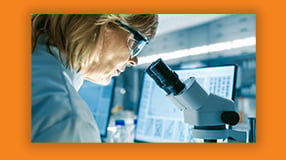
What is Coefficient of Linear Expansion? Formula, Units & More
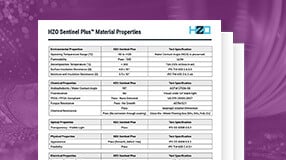
Download HZO's Sentinel Plus™ Nanocoating Material Properties Datasheet
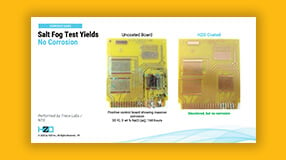
Learn About the Thin Film Coating Properties and Processes In Our Webinar
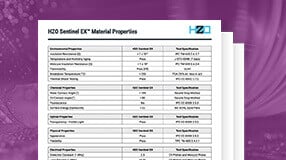
Download HZO Sentinel EX™ Nanocoating Material Properties Datasheet
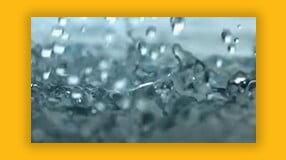
The Difference Between "Hydrophilic and Hydrophobic" Coating Properties
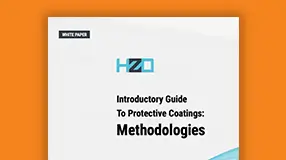
Learn about Protective Coating Methodologies With Our White Paper
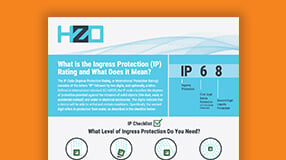