What is Parylene? Industry Use Cases, Types, Properties
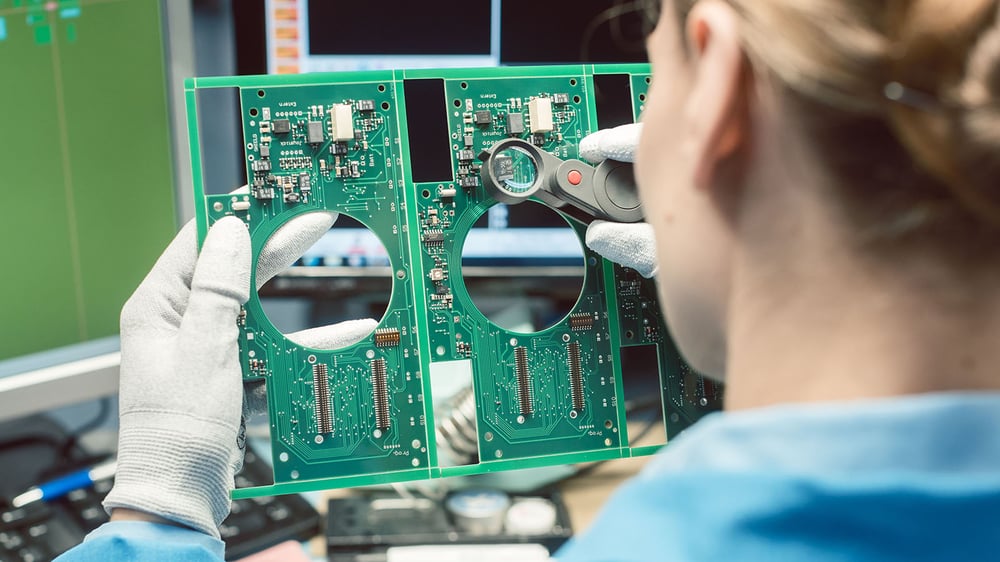
What is Parylene? Is it Right For My Project?
Parylene forms high-performance thin-film coatings. There are several types, like Parylene N, C, and D. Each has unique chemical traits for different uses. Across all types, Parylene has excellent dielectric strength and unmatched barrier properties. The coatings resist corrosive gases, moisture, and solvents, ensuring product longevity.
Parylene coatings provide seamless coverage that is defect- and pinhole-free. The CVD process polymerizes and deposits them onto components at around room temperature. The coatings are free of defects and pinholes, which are ideal for critical applications where reliability and performance matter. Parylene is used in medical devices, aerospace parts, and advanced electronics for these reasons.
Why Do Engineers Use Parylene Coating?
Parylene is a unique conformal coating. Its properties give it superior performance in many applications. Parylene coating is recognized for its impressive dielectric properties, providing exceptional electrical insulation. It can work well in many electrical and electronic contexts, protecting against short circuits and other hazards.
Parylene also exhibits robust chemical resistance, preserving components in corrosive environments. Chemical agents find it hard to penetrate Parylene's molecular structure. This ensures the longevity and reliability of coated devices.
Another notable attribute is Parylene's moisture and vapor protection. Parylene forms a seamless barrier when applied, defending against water and moisture ingress. Preventing such contamination is vital to keeping components functional. This is especially true for those in high-humidity areas or subject to sudden temperature changes.
Then there is Parylene's thermal stability. Parylene's composition lets it withstand extreme temperatures. The coating keeps its physical and chemical properties across a wide range. Parylene can endure both the bitter cold of cryogenics and the intense heat of aerospace engines.
Parylene's versatility makes it more than just a protective coating. It is a strategic ally for industries where durability and performance are vital. Parylene-coated components work well. They are safe from environmental damage. Thus, using Parylene as a protective solution is not just a preference. It is a choice based on its proven ability to protect and preserve.
What Industries Use Parylene?
In electronics protection, Parylene is a shield against moisture and threats. The coating protects sensitive circuits from humidity, corrosive gases, and contaminants. Everyday devices, from smartphones to satellites, benefit from such defense. It ensures they work and last longer.
Why is Parylene Used in the Medical Industry?
Within the medical industry, Parylene's biocompatibility and chemical resistance make it indispensable. Parylene creates a barrier between the device and the body, making medical treatments safer and more reliable.
Why is Parylene Used in Aerospace?
Parylene can make UAVs more lightweight, improving battery performance. Also, Parylene protects PCBs and components from humidity, weather hazards, and pollution.Why is Parylene used in the Automotive Industry?
Parylene improves the reliability of electronics exposed to high temperatures and abrasive conditions. Its chemical resistance helps automotive electronics withstand oils, cleaning fluids, and antifreeze. Parylene is also a green coating compliant with Prop 65, REACH, and RoHS.
Watch a video about why automotive OEMs use Parylene:
Why is Parylene used in LED Systems?
Parylene keeps LED brightness and color consistent over time and protects outside displays from weather damage. The thin coatings make it easier to mount displays as well.
Parylene for Military Applications
In the military, Parylene coatings protect advanced defense equipment. They ensure mission-critical applications remain reliable in tough conditions. Parylene meets the MIL-I-46058C specification.
Why is Parylene Used for Consumer Electronics?
Parylene makes gadgets more durable. It helps them resist wear and tear from daily use. Consumer electronics manufacturers can use Parylene coatings to meet any IP rating.
What Are the Parylene Types Used for?
Different applications need different Parylene types. Each has unique properties, suitable for various uses. Manufacturers might choose Parylene N for electronics needing a dielectric layer. Parylene C is better where moisture and gas ingress are concerned. Parylene D, though less popular, can withstand high temperatures Parylene N and C can't.
Parylene N
Parylene N can penetrate and coat minute spaces effectively. This feature creates coatings that can evenly cover complex shapes on electronic parts. Parylene N has no chlorine atoms in its molecular structure, and the coating has a high dielectric strength.- High dielectric strength
- Excellent crevice penetration
- Good for delicate electrical components
Parylene C
Parylene C has a chlorine atom, altering its properties. This change gives Parylene C lower moisture and gas permeability. With enhanced barrier properties, Parylene C protects medical devices from bodily fluids and sterilization.- Superior moisture and gas resistance
- Good for corrosion protection
- Often used for medical equipment
Parylene D
Also, we encounter Parylene D. It has two chlorine atoms in its structure. This constitution gives Parylene D greater thermal stability than Parylene N and C, useful in high-temperature applications. But, Parylene D is less commonly used than its counterparts. Its applications can be specific and rare.- Greater thermal stability
- Good for high-temperature environments
- Narrower range of applications
Why Choose Parylene Over Other Conformal Coatings?
Parylene has distinct differences from other coatings like silicon and epoxy. Parylene's unique chemical vapor deposition process gives it a 100% conformal coating. This provides a strong barrier against moisture, chemicals, and extreme temperatures. This contrasts with silicone coatings. They are usually applied by brushing, dipping, or spraying. These methods can cause inconsistencies in coating thickness and performance.
Durability, too, distinguishes Parylene from other coatings. Parylene's strong molecular structure makes it durable under stress. This gives it a long lifespan. Meanwhile, epoxy coatings are strong but can become brittle over time. They also lack Parylene's ability to stay elastic and flexible in varying temperatures.
When you need ultra-thin, uniform coatings, Parylene is often best. It can coat at micron-level thicknesses without compromising coverage or protection. This lets manufacturers meet design specs without adding weight or changing dimensions. Also, Parylene's biocompatibility makes it vital for medical device coatings that will contact bodily tissues or fluids.
Silicone and epoxy coatings work well in many uses. But, they may not meet the strict standards in aerospace and medical industries. There, even the smallest failure can have catastrophic results. In such cases, choosing Parylene proves its unmatched performance in critical uses.
Bottom Line – Is Parylene Right for My Application?
Should you use Parylene for your next project? First, ask yourself how much you value reliability and performance. Then, answer the question.
Consider Parylene when failure is not an option.
Parylene may also be your best bet when you need lightweight protection. This includes aerospace and automotive markets that must support fuel efficiency.
Some products do not need such strong barrier properties and corrosion resistance. It's not necessary to ruggedize all devices. In these cases, it would raise costs, delay new products, and serve no purpose.
It is not always necessary to achieve critical, reliable protection. But when it is, Parylene coatings are the best defense. Have questions? Speak to an engineer.
Watch the webinar about Parylene’s proven corrosion resistance.
An Overview of Our Parylene Coating Equipment
Parylene Coating Removal - Methods & Best Practices for Each
Parylene Conformal Coatings - Parylene Conformality Explained
Mallory is a veteran writer with over a decade of writing experience and has spent over five years at HZO learning about coating technology from the best minds in the industry. Professionally, Mallory is especially interested in the process of problem-solving and watching how the engineering team develops solutions that ensure business requirements are met. Over her years at HZO, Mallory's writing has been cited in industry whitepapers, including "Parabolic Model for Optimum Dry Film Thickness (DFT) of Corrosion Protective Coatings" and "Universal Approach to Integrating Reduced Graphene Oxide into Polymer Electronics." All of Mallory’s blogs are reviewed for accuracy before publication.
Additional Resources
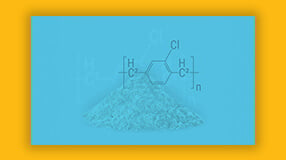
Learn About Parylene Properties With Our Resource Page
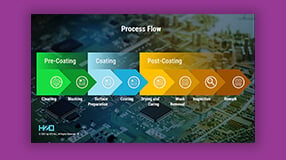
Learn How To Incorporate Conformal Coating Into Your Manufacturing Process
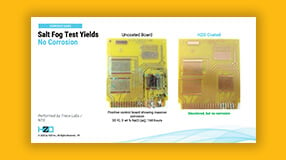
Learn About the Thin Film Coating Properties and Processes In Our Webinar
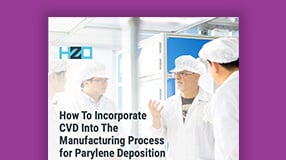
Learn How to Bring Parylene Deposition In-House
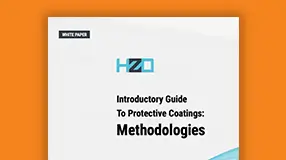