Parylene Coating Properties:
Tables of Values, Types, & Technical Data Sheets
Introduction
Pinhole and defect-free Parylene coatings provide exceptional dielectric strength and superior resistance to chemicals and corrosion. Parylene is one of the best coatings for moisture impermeability, with complete coverage, even on complex substrates. Parylene's many benefits are due to the chemical deposition process and material properties.
Parylene Coating Properties Overview
Parylene Electrical Properties
As a film that coats conductive areas on electronics, Parylene is an excellent dielectric (electrical insulator) coating. Its lack of pinholes and defects enhances capabilities, but its fundamental composition defines Parylene's dielectric properties.
As the table below indicates, Parylene's electrical properties are among the best of the conformal coatings.
Electrical Properties of Conformal Coatings |
||||||||||||||||||||||||||||||||||||||||||||||||
---|---|---|---|---|---|---|---|---|---|---|---|---|---|---|---|---|---|---|---|---|---|---|---|---|---|---|---|---|---|---|---|---|---|---|---|---|---|---|---|---|---|---|---|---|---|---|---|---|
Parylene N | Parylene C | Acrylic | Epoxy | Silicone | Urethane | |||||||||||||||||||||||||||||||||||||||||||
Dielectric Strength (DC (V/mil) | 7000 | 5600 | 1200 | 900-1000 | 1100-2000 | 1400-3000 | ||||||||||||||||||||||||||||||||||||||||||
Sheet Resistivity (Ω·cm) @ 23°C 50%RH | 1.4x1017 | 6-8x1016 | 1013-14 | 1012-17 | 1015-16 | 1011-15 | ||||||||||||||||||||||||||||||||||||||||||
Dielectric Constant (60Hz) | 2.65 | 3.15 | 3.0-4.0 | 3.5-5.0 | 2.7-3.1 | 5.3-7.8 | ||||||||||||||||||||||||||||||||||||||||||
Dielectric Constant (1KHz) | 2.65 | 3.1 | 2.5-5 | 3.5-4.5 | 2.6-2.7 | 5.4-7.6 | ||||||||||||||||||||||||||||||||||||||||||
Dielectric Constant (1MHz) | 2.65 | 2.95 | 3.0-4.0 | 3.3-4.0 | 2.6-2.7 | 4.2-5.2 | ||||||||||||||||||||||||||||||||||||||||||
Dielectric Loss (tan δ) (60Hz) | 0.0002 | 0.02 | 0.2-0.4 | 0.002-0.01 | 0.001-0.007 | 0.015-0.05 | ||||||||||||||||||||||||||||||||||||||||||
Dielectric Loss (tan δ) (1KHz) | 0.0002 | 0.019 | 0.02-0.04 | 0.002-0.02 | 0.001-0.005 | 0.04-0.06 | ||||||||||||||||||||||||||||||||||||||||||
Dielectric Loss (tan δ) (1MHz) | 0.0006 | 0.013 | 0.035-0.056 | 0.03-0.05 | 0.001-0.002 | 0.05-0.07 | ||||||||||||||||||||||||||||||||||||||||||
Dielectric Loss (tan δ) (1GHz) | — | < 0.007 | — | — | — | — |
The volume resistivity and dissipation factors of various Parylene types are detailed below.
Volume Resistivity and Dissipation Factors of Parylene Types |
|||||||||||||||||||||||||||||||||||
---|---|---|---|---|---|---|---|---|---|---|---|---|---|---|---|---|---|---|---|---|---|---|---|---|---|---|---|---|---|---|---|---|---|---|---|
Parylene N | Parylene C | Parylene F (VT-4) | |||||||||||||||||||||||||||||||||
Volume Resistivity, Ω·cm, 23 °C,50% RH | 1.4 x 1017 | 8.8 x 1016 | 1.1 x 1017 | ||||||||||||||||||||||||||||||||
Dissipation Factor (tan δ) (60Hz) | 0.0002 | 0.020 | 0.0002 | ||||||||||||||||||||||||||||||||
Dissipation Factor (tan δ) (1KHz) | 0.0002 | 0.019 | 0.0002 | ||||||||||||||||||||||||||||||||
Dissipation Factor (tan δ) (1MHz) | 0.0006 | 0.013 | 0.0008 | ||||||||||||||||||||||||||||||||
Dissipation Factor (tan δ) (6GHz) | 0.0021 - 0.0028 | 0.0002 - 0.0010 | — |
Parylene Mechanical Properties
Parylene has a relatively high yield and tensile strength compared to other polymer coatings, and wear resistance is substantial. It is a crystalline polymer, resulting in mostly high mechanical strength.
Young's Modulus
The table below shows Young's Modulus and Tensile Strength values for Parylenes C and N, as well as a polyester and a polyimide.
Young's Modulus |
||||||||
---|---|---|---|---|---|---|---|---|
Material | Young's Modulus | Tensile Strength | ||||||
Polyester | 7.1x105 psi MD | 29,000 psi MD | ||||||
Polyimide | 3.6x105 psi | ~29,000 psi | ||||||
Parylene C | 4.6x105 psi | 10,153 psi | ||||||
Parylene N | 3.5x105 psi | 6,526 psi |
Taber Wear Index
Taber wear index values of Parylene C, N, an epoxy, and a urethane are listed below.
Taber Wear Index |
|||
---|---|---|---|
Material | Taber Wear Index | ||
Parylene C | 44 | ||
Parylene N | 9.7 | ||
Epoxy | 38 | ||
Urethane | 55-67 |
Impact Resistance
Impact resistance of two Parylene types, Epoxy, and Urethane can be found below.
Impact Resistance |
|||
---|---|---|---|
Material | Impact Resistance (kg·cm) | ||
Parylene C | >85 | ||
Parylene N | >85 | ||
Epoxy | 35 | ||
Urethane | 23 |
Although Parylenes have good abrasion resistance, they will still be susceptible to scratches because they are polymer films. However, housing a Parylene-coated assembly in an enclosure will ensure that abrasion will be negligible. Additionally, using a thicker coating should extend the product's life.
Parylene Barrier Properties
Parylene coatings are of high purity, so any moisture absorbed or permeated will not contribute to chemical corrosion or become absorbed. Furthermore, the water vapor transmission rates of the Parylenes are among the lowest of polymers.
The table below compares the gas permeability and WVTR (Water Vapor Transfer Rate) of Parylene with other conformal coating types:
Gas Permeability and WVTR of Conformal Coating Types |
||||||||
Polymer | Gas Permeability at 25 °C, (cc·mm)/ (m2·day·atm) | WVTR (g·mm)/ (m2·day) |
||||||
N2 | O2 | CO2 | H2 | H2S | SO2 | CI2 | ||
Parylene C | 0.4 | 2.8 | 3.0 | 43.3 | 5.1 | 4.3 | 0.1 | 0.08 |
Parylene N | 3.0 | 15.4 | 84.3 | 212.6 | 313 | 745 | 29.2 | 0.59 |
Parylene D | 1.8 | 12.6 | 5.1 | - | 0.6 | 1.9 | 0.2 | 0.09 |
Parylene F (VT-4) | - | 16.7 | - | - | - | - | - | 0.28 |
Epoxy (ER) | 1.6 | 4 | 3.1 | 43.3 | - | - | - | 0.94 |
Polyurethane (UR) | 31.5 | 78.7 | 1.81 | - | - | - | - | 0.93 |
Silicone (SR) | - | 19,685 | 118,110 | 17,717 | - | - | - | - |
Corrosion Resistance Properties
In addition to exhibiting low WVTR (Water Vapor Transfer Rate) and gas permeability, Parylene performs particularly well as a barrier to corrosion due to its ability to minimize the influence of these factors:
- Liquid water uptake – Parylene absorbs minimal water
- Coating porosity – Parylene coatings are pore and pinhole-free
- Ionic permeability – Salts do not pass through the coating easily
Polymer | Coating Method | Layer Thickness (μm) | Time Until Total Breakdown |
Parylene C | CVD | 25 | > 30 Days |
Epoxy (ER) | Dip Coating | 100 ± 25 | 6 Hours |
Polyurethane (UR) | Dip Coating | 100 ± 12.5 | 6 Hours |
Silicone (SR) | Dip Coating | 75 ± 12.5 | 58 Hours |
Teflon | Spraying | 75 | 6 Hours |
Parylene Optical Properties
Transparent in appearance, Parylene coatings protect optical lenses, sensors, fiber optic components, electro-optical components, and related products. The films have excellent transmission and low absorption in the near-infrared and visible regions of the electromagnetic spectrum, allowing for desirable performance.
If exposed to UV (Ultraviolet Light/Radiation) in air or oxygenated atmospheres for extended periods, Parylene N, C, and, much later, VT-4 will degrade, which means measures must be taken to limit direct sunlight exposure, or limiting the amount of oxygen near the coating. VT-4 does better with UV exposure than N and C, but dimer (starting material) can cost at least three to five times more than C.
Index of Refraction
Parylene's refraction index is compared with other materials below.
Material | Index of Refraction |
Air | 1.0003 |
Liquid Water | 1.333 |
Parylene C | 1.602 |
Parylene N | 1.585 |
Polyimide | 1.70 |
Polyester | 1.640-1.670 |
Parylene Thermal Properties
The temperature stability values for the parylenes are collected in the table below and are based on industry literature.
Parylene-Type | Long-Term Temperature Limit (°C) Duration = ~10+ Years) | Short-Term Temperature Limit (°C) Duration = ~1 Month | Melting Point Temperature (Tm) |
Parylene N | 60 | 95 | 420 |
Parylene C | 80 | 115 | 290 |
Parylene D | 100 | 135 | 380 |
Parylene VT-4 | 200 | 250 | – |
Parylene AF-4 | 350 | 450 | >500 |
Material | Coefficient of Linear Expansion |
FR-4 |
1.4x10-5/ °C 1.2x10-5/ °C 7.0x10-5/ °C |
Polyester | 1.7x10-5/ °C |
Polyimide | 2.0x10-5/ °C |
Parylene C | 3.5x10-5/ °C |
Parylene F | 3.6x10-5/ °C |
Parylene N | 6.9x10-5/ °C |
Material | Specific Heat |
FR-4 Epoxy Glass no Copper |
0.28 cal/g·°C |
Polyester | 0.28 cal/g·°C |
Polyimide | 0.26 cal/g·°C |
Parylene C | 0.17 cal/g·°C |
Parylene F | 0.25 cal/g·°C |
Parylene N | 0.20 cal/g·°C |
Material | Specific Heat |
FR-4 (through-plane) | 0.29 - 0.34 |
FR-4 (in-plane) | 0.81 - 1.06 |
Polyester | 0.15 |
Polyimide | 0.12 |
Parylene C | 0.08 |
Parylene F | 0.10 |
Parylene N | 0.12 |
Flammability
Both Parylenes C and VT-4 contain halogens with C having chlorine (Cl) and VT-4 having fluorine (F), both of which function as flame retardants. Therefore, these materials self-extinguish almost immediately after a flame is removed. Flammability is typically tested using UL 94 HB for horizontal burn and UL 94 V for vertical burn.
Dry Lubricity
Cold Temperatures
Although oxidation and degradation aren't concerns at these lower temperatures, polymer materials, including Parylene, cool down, they become stiffer, less flexible, and more likely to incur physical damage. However, Parylene films can be flexed multiple times (up to 6 to 9) when cooled down to liquid nitrogen temperatures, while most other coatings will crack on the first or second flex.
Parylene is a low-friction coating that allows easy sliding and is a dry lubricant. The friction coefficient for Parylene coatings is low, ranging from 0.25 to 0.33, so their lubricity is close to Teflon™. Due to this slickness, Parylene is used in medical device applications as a high-flexibility, low-friction coating that resists contamination and discoloration.
Biocompatibility
Parylene conforms to the USP Class VI and ISO 10993 standards and is biocompatible. Parylene is also non-toxic and physiologically non-reactive.
Parylene Types
Parylene coatings come in several types, including Parylene C, N, and F (VT-4) and high-purity; no sodium, ammonium, or chloride ions are generated from or inherent in the coatings.
Parylene N is a hydrocarbon polymer entirely. Parylene C is identical to N except for chlorine atoms covalently bonded along the polymer chain. However, these chlorine atoms are not easily ionized or ionic.
Fluorinated dimers, such as VT-4, are more challenging to manufacture and expensive but benefit from higher ultraviolet (UV) and thermal resistance than N and C. This is due to a greater difficulty oxidizing CH2 connections in the VT-4 polymer since they were replaced with CF2 groups.
Parylene starting materials polymerize through a free radical addition mechanism, that doesn’t create reaction byproducts.
Types of Parylene Compared
Parylene C Properties
Both Parylenes C and VT-4 contain halogens with C having chlorine (Cl) and VT-4 having fluorine (F), both of which function as flame retardants. Therefore, these materials self-extinguish almost immediately after a flame is removed. Flammability is typically tested using UL 94 HB for horizontal burn and UL 94 V for vertical burn.
Parylene F Properties
Parylene F (VT-4) is free from bromine and chlorine halogens and contains fluorine. It exhibits the highest resistance to heat and UV when compared to C and N.
Parylene N Properties
Parylene N is halogen-free and is a unique dielectric material because of a low dissipation factor which changes only slightly with frequency.
The Parylene Process for Each Parylene Type
Each Parylene type's deposition process is affected by its chemical composition. For example, N and VT-4 deposit much more slowly than C. Additionally, it can be more challenging to control a Parylene type's coating uniformity and dispersion within the deposition chamber. Finally, different starter materials have varying costs, availability, and temperature requirements for the deposition chamber.
Properties | ← Decreasing – Parylene Type – Increasing → |
||||
Raw Material Cost | N | C | D | VT-4 | AF-4 |
Deposition Rate | AF-4 | N | VT-4 | C | D |
Temperature & UV Exposure Performance | N | C | D | VT-4 | AF-4 |
Moisture Barrier Performance | VT-4 | N | AF-4 | D | C |
Crevice Penetration | D | C | VT-4 | N | AF-4 |
Dielectric Properties | C | D | N | VT-4 | AF-4 |
Download Parylene Datasheet
Want to understand if Parylene conformal coating specifications properties are suitable for your project? Download the HZO Parylene datasheet; no contact information is required. Meanwhile, please contact us if you would like to speak to a member of our Applications Engineering team.
Additional Resources
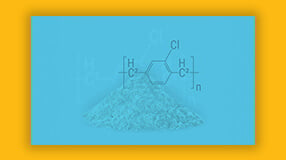
Learn About Parylene Properties With Our Resource Page
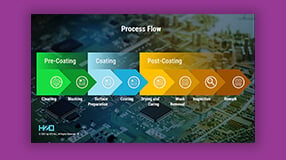
Learn How To Incorporate Conformal Coating Into Your Manufacturing Process
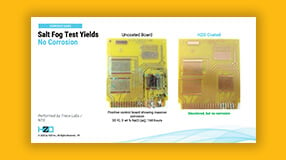
Learn About the Thin Film Coating Properties and Processes In Our Webinar
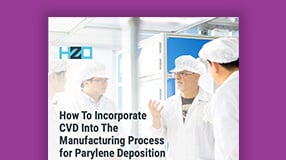
Learn How to Bring Parylene Deposition In-House
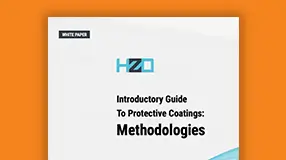