Parylene Biocompatibility - Parylene Compared, Analyzed For Medical
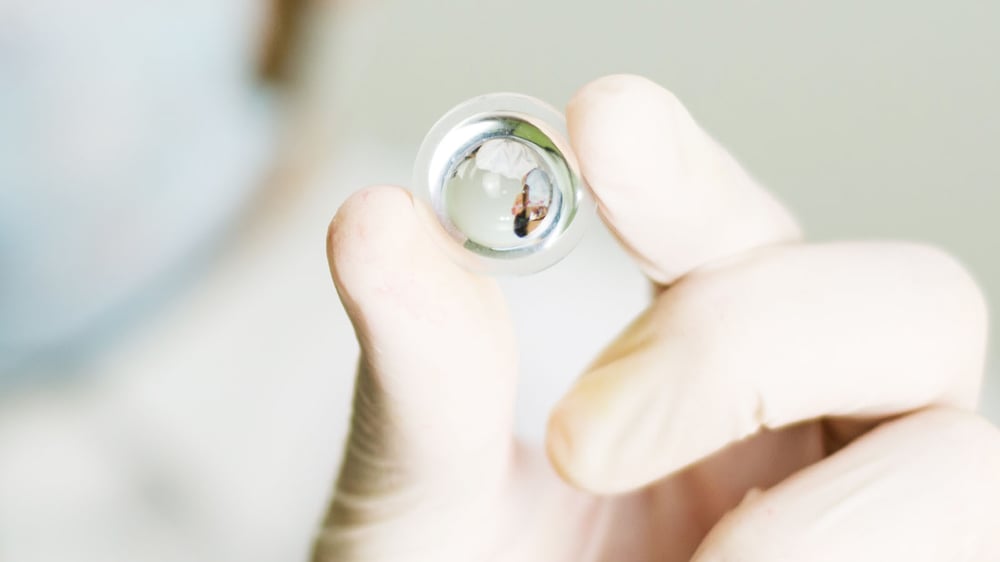
Biocompatibility is vital to medical device safety. It ensures implants and other devices can be used in and on the body with minimal adverse reactions. Medical devices must be highly biocompatible, as they often contact the body's internal tissues and fluids.
Parylene's biocompatibility is crucial for its use in medical devices. Additionally, Parylene is physiologically non-reactive and isn't toxic.
Parylene's Biocompatibility
Medical professionals and device makers rely on strict biocompatibility testing for safety. They follow established standards, especially ISO 10993 and the USP VI Standard.
A complete analysis of Parylene shows it is biocompatible. It meets the strict standards for medical device use. Third-party sources have tested the material, and it causes no harm to tissues or body fluids. Parylene's chemical inertness makes it compatible. It provides a safe interface between the device and human tissue.
Why is Parylene Biocompatible?
Parylene's chemistry and structure make it biocompatible. It meets the USP's highest, Class VI, biocompatibility standards. Parylene has passed the USP's strict tests, described here. Also, it has a proven track record of reliable performance in the medical device industry.
Biocompatible Parylene Coatings Last
Decades of use show Parylene coatings maintain their performance and integrity. Bodily fluids, varying pH levels, and enzymes do not reduce their effectiveness. Parylene-coated medical devices are vital. They provide reliable, long-lasting protection and function.
Parylene's uniform, pinhole-free coating does more than protect. It provides a reliable interface between the device and the body. So, encapsulated medical components can serve patients for as long as they are used. The difference is not just in Parylene's inertness. Parylene can also resist the harsh conditions of the human body.
Below, you can see a Parylene-coated Raspberry Pi computer running underwater in HZO’s lobby. As of the date of publication, this computer has been running fully submerged in tap water for over two years now:
Parylene Versus Other Biocompatible Materials
Parylene often stands out for its unique properties. So, it is a good biocompatible material for medical uses. But, a range of alternatives exists. They include silicone, Teflon, and various medical-grade metals and polymers. Each material has a unique set of traits best in certain conditions.
Parylene is known for its great chemical resistance. It can also form pinhole-free coatings at a micron-level thickness. This lets devices work reliably in the harsh human body. Parylene coatings are ultrathin. They keep the feel and function of the underlying material. This is a big advantage over bulkier options like silicone rubber or polyurethane.
Parylene vs. Stainless Steel
Consider Parylene versus stainless steel, which is a common choice for implants. Stainless steel is strong and fatigue-resistant. But it can't match Parylene's ability to conform to complex shapes. The difference shows in applications needing a seamless coat over complex parts. Here, Parylene's conformal nature gives a uniform layer. It fully isolates the parts from the body's fluids and tissues.
Parylene vs. Teflon
Unlike Teflon, a popular biocompatible material, Parylene is PFAS-free. It is REACH and RoHS compliant, and its ability to maintain physical integrity under sterilization methods boosts its comparability.
The Limitations of Biocompatible Parylene
However, Parylene is not without its limitations. Parylene has great barrier properties and electrical insulation. But, its mechanical strength is not as good as that of metals or ceramics. This property requires careful thought in load-bearing implant uses where strength is vital. Also, the Parylene application process uses chemical vapor deposition. It's very effective but may complicate the manufacturing workflow. Simpler methods, like dip or spray coating, are used for silicone and latex.
Read about how to incorporate Parylene into your process
Other materials may have specific advantages, like higher tensile strength or elasticity. But, Parylene's combination of properties often justifies its selection. It depends on the intended use, performance, and regulatory standards. Manufacturers must balance performance and material costs. They also consider the complexity of application methods for producing and using medical devices.
Learn more in our webinar, Parylene: Pros, Cons, and Practicalities
Why is Parylene Used in Medical Applications?
Parylene is a very popular protective coating in the medical industry. In 2023, the parylene market was valued at $98.38 million; by 2030, it is expected to grow to $118.52 million. Why is Parylene so widely used? The answer lies in its powerful protective properties.
Parylene is highly resistant to moisture, chemicals, and other environmental factors. The coatings protect medical devices in and on the body at 50% of the thickness of conventional conformal coatings, reducing product bulk and weight. Also, Parylene has very high dielectric strength, up to 7,000 V/mil. This ensures that electrical components can function uninterrupted by external stimuli.
Parylene's conformal coating attributes ensure a uniform, pinhole-free application. It adheres to every contour of the complex geometries in medical devices. This ensures complete encapsulation with no areas left vulnerable. Parylene's coating uniformity greatly improves device protection.
- Chemical Resistance: Parylene surpasses many materials in its resistance to corrosive bodily fluids.
- Dielectric Strength: Parylene N has an extremely high dielectric strength of 7,000 V/mil
- Biocompatibility: Parylene causes minimal tissue reaction. It compares well to common biocompatible materials.
- Barrier Protection: Parylene's seamless coatings provide unmatched barrier protection. Porous materials, like silicone foams, cannot match it.
Common Uses for Parylene in Medical Settings
Parylene coatings have established their utility in a wide range of medical devices. They improve protection and longevity. Here are some use cases for Parylene:
- Cardiac assist devices use Parylene. Its thin, uniform coating reduces thrombogenicity without harming the device's inherent functionality.
- Parylene-coated needles and cannulas have less friction. This makes them easier to insert, which is more comfortable for patients.
- Parylene coatings improve stents. They prevent corrosion and reduce friction, aiding in their insertion and long-term performance in the body.
Diverse biomedical applications capitalize on Parylene's biocompatibility. It is present in both in vivo and in vitro environments. These include surgical instruments, cochlear implants, and diagnostic equipment sensors.
Partner with HZO for Your Next Medical Project
Do you have any questions about Parylene or what it can do for your next project? Please reach out to our team. We’re standing by to answer your questions and help you determine your next step.
Parylene Conformal Coatings - Parylene Conformality Explained
An Overview of Our Parylene Coating Equipment
How Much Does Parylene Coating Cost? - All Things Considered
Mallory is a veteran writer with over a decade of writing experience and has spent over five years at HZO learning about coating technology from the best minds in the industry. Professionally, Mallory is especially interested in the process of problem-solving and watching how the engineering team develops solutions that ensure business requirements are met. Over her years at HZO, Mallory's writing has been cited in industry whitepapers, including "Parabolic Model for Optimum Dry Film Thickness (DFT) of Corrosion Protective Coatings" and "Universal Approach to Integrating Reduced Graphene Oxide into Polymer Electronics." All of Mallory’s blogs are reviewed for accuracy before publication.
Additional Resources
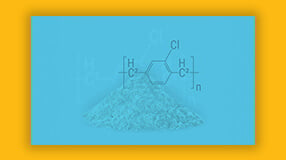
Learn About Parylene Properties With Our Resource Page
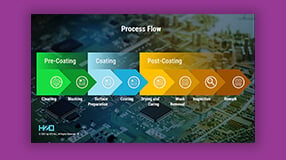
Learn How To Incorporate Conformal Coating Into Your Manufacturing Process
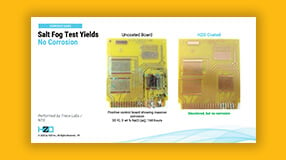
Learn About the Thin Film Coating Properties and Processes In Our Webinar
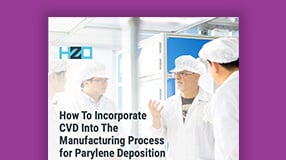
Learn How to Bring Parylene Deposition In-House
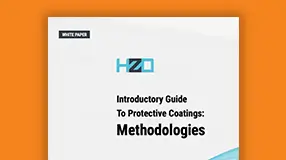