Parylene Coating Removal - Methods & Best Practices for Each
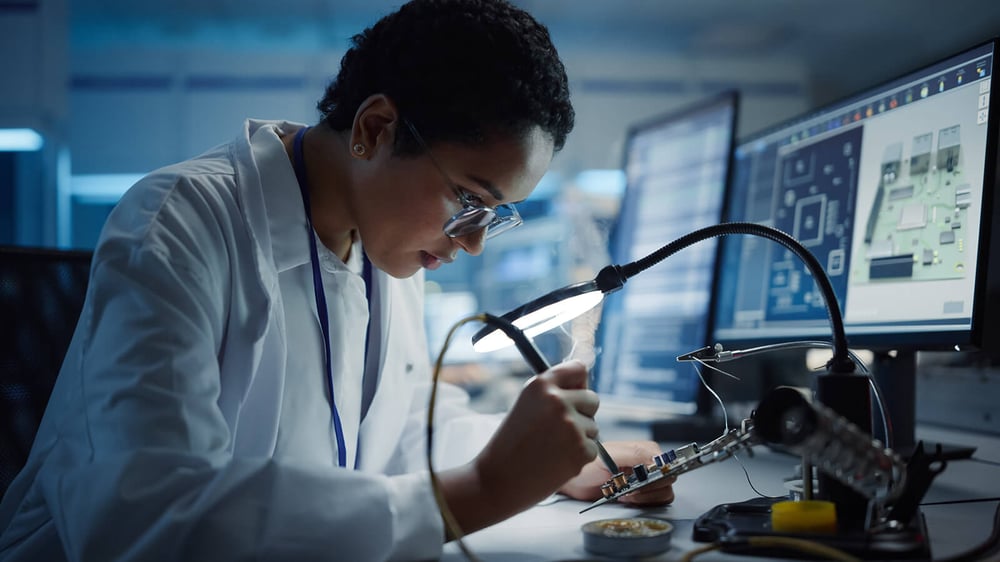
Parylene coatings present unique challenges when it comes to rework and removal. They often outperform other conformal coatings. Parylene has better barrier properties, uniform coverage, and performance in thinner layers.
Learn more about what Parylene is used for.
Additionally, Parylene's chemical resistance can withstand corrosive gases and liquids. It also performs in extreme temperatures and high electrical activity.
Want to know if HZO Parylene meets your specifications?
But, the properties that make Parylene the "gold standard" of conformal coating can also make it hard to remove. Thankfully, you can use methods to remove and rework Parylene when needed.
When Do You Need to Remove Parylene?
From time to time, it is necessary to rework or remove coating. Sometimes, job specifications change or a Parylene vendor incorrectly applies the coating.
What is Parylene Delamination?
One example of poor application is Parylene delamination. This is when the conformal coating separates from the coated surface. This results in an unattached, torn, non-conformal coating and an unacceptable finish. Delamination defeats the purpose of Parylene coatings. It must be avoided at all costs. Even partial lifting can render the protective coating useless.
What Causes Parylene Delamination?
Many causes of Parylene delamination exist. One is demasking, a standard process. It creates a need for high-quality inspections after production. Other causes include:
Coating porosity: A vapor pressure difference creates a risk of moisture intrusion into the substrate. Pressure fluctuations and temperature changes create osmotic pressures. These separate the coating from the component.
Incompatible materials: The Parylene coating must bond with the component surface for successful coverage. When the Parylene and the surface are incompatible, they create incongruous surface energies. This causes minimal bonding.
Contaminated surfaces: Improperly cleaned component surfaces do not support adhesion.
Regardless of the reason, the resulting Parylene removal must be efficient and safe. It must protect the coated substrate's integrity.
The following methods are popular ways to approach Parylene removal.
How Do You Do Mechanical Parylene Removal?
Parylene's strength and uniformity make it tough to remove. So, be careful with mechanical methods. They may damage the final product. However, Parylene is a soft polymer. So, mechanical methods may remove it.
Methods like picking, cutting, and scraping are effective. But, they may damage components, substrates, and delicate track lines. This type of removal requires considerable attention and care. Good spot removal is possible with proper masking. But, mechanical methods may be unreliable for larger surfaces.
How to Remove Parylene with Micro-Abrasion
Micro-abrasion is a process performed with automated or handheld systems. It targets a specific area by blasting the Parylene coating with inert gas or dry air and abrasive media. This removal method is suitable for both whole board and spot removal. It is generally easy to put in place, quick, cost-effective, and environmentally friendly.
Can You Use Thermal Removal With Parylene?
Parylene can withstand high temperatures. But, a high-temperature oven or soldering iron can remove it in small, specific areas. As heat is applied, the coated component rises from the board and lifts off.
This technique may be adequate for small repairs. It is less reliable for large surfaces. But, it can still be effective for some jobs. However, residues and discoloration may occur. Parylene's high melting point may damage heat-sensitive substrates. Thermal removal can be hard to manage. It's not recommended without Parylene experts' help.
Which Chemical Can Remove Parylene?
Parylene is chemically inert, resisting chemical degradation. But, one chemical has been used to strip Parylene from substrates and components. It is a colorless organic compound, tetrahydrofuran (THF), with the formula (CH2)4O. This solvent softens the Parylene coating. It temporarily loosens the bond between the substrate and the coating. At this point, the Parylene can be lifted off with tweezers. THF can remove Parylene, but it may damage the coated part. Use the solvent only for complete coating removal. For the security of the components under the coating, consider other removal methods before using TFH.
Laser Ablation for Parylene Removal
Laser ablation is a process that removes material from a surface by irradiating it with a laser beam. The beam can cut, drill, or mark delicate materials, providing precise removal. At HZO, a laser ablation process converts Parylene to gas or plasma with pulsed laser sources. This method is cost-effective for complex removals. It gives better results. It can also service 3D devices and Parylene-free areas.
Conclusion
There are many effective methods to remove Parylene should the need arise. Each method has its strengths. So, you must know your options. Then, choose the best method for your project.
If you need Parylene removal or want to discuss your project with experts, please message us today. Removing Parylene can be tough. But, a skilled company can simplify and lower the cost of the job. We can help with scalable Parylene equipment and Parylene masking automation. We can also address concerns about the cost of Parylene services.
An Overview of Our Parylene Coating Equipment
What is Parylene? Industry Use Cases, Types, Properties
Parylene Masking - General Concepts Explained
Mallory is a veteran writer with over a decade of writing experience and has spent over five years at HZO learning about coating technology from the best minds in the industry. Professionally, Mallory is especially interested in the process of problem-solving and watching how the engineering team develops solutions that ensure business requirements are met. Over her years at HZO, Mallory's writing has been cited in industry whitepapers, including "Parabolic Model for Optimum Dry Film Thickness (DFT) of Corrosion Protective Coatings" and "Universal Approach to Integrating Reduced Graphene Oxide into Polymer Electronics." All of Mallory’s blogs are reviewed for accuracy before publication.
Additional Resources
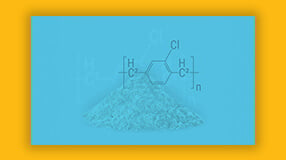
Learn About Parylene Properties With Our Resource Page
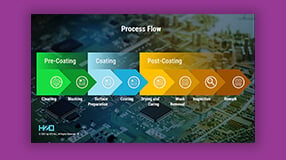
Learn How To Incorporate Conformal Coating Into Your Manufacturing Process
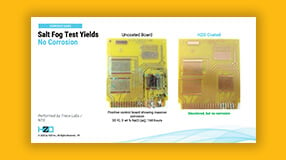
Learn About the Thin Film Coating Properties and Processes In Our Webinar
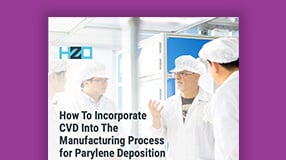
Learn How to Bring Parylene Deposition In-House
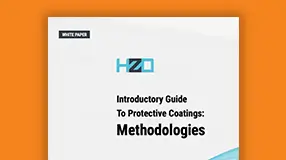