ADAS Design and Validation for the Real World - Automotive Coatings
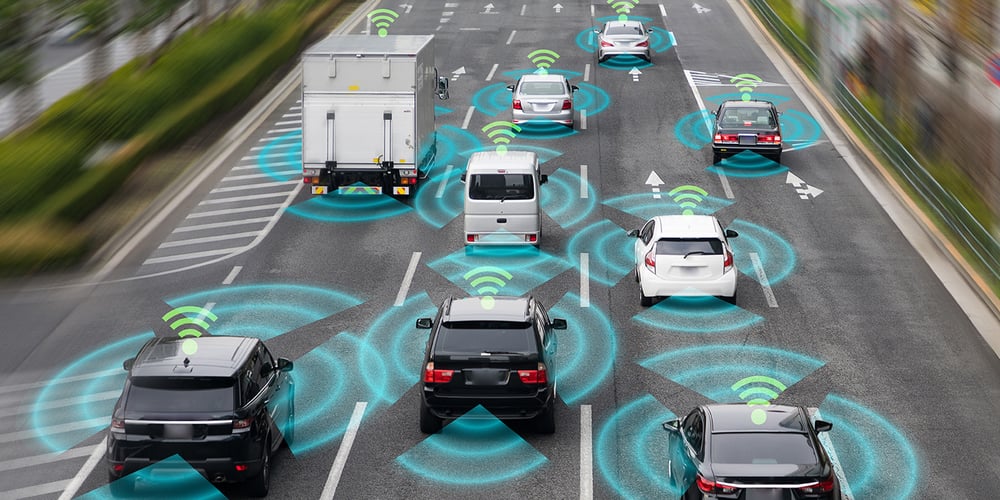
When consumers purchase a vehicle with ADAS safety features, they believe they have a layer of protection to be entirely relied on. In reality, though, without a methodical, effective ADAS component design that accounts for real-life situations, these features are no more than crutches.
In addition to the ethical argument that safety should be an underlying principle of ADAS design, liability concerns create a business case for ADAS components that dependably function in the typical automotive service environment.
As ADAS designers evaluate the risk of harm, they may ask about the probability of exposure to an element or situation that could cause failure. They may ascertain how severe the resulting damage may be and determine how controllable the issue is if it should occur.
The risk of harm is high in instances such as premature ADAS component failure due to harsh environments. ADAS PCBAs and components will inevitably encounter corrosive elements, humidity, thermal shock, water ingress, and other environmental factors that compromise electronics. If this ADAS component should fail as a result, consumers relying on a safety feature could incur severe damage and liability, and in terms of controllability, there is not much that can be done upon critical component failure.
ADAS component reliability through harsh environments is a high-risk issue. Therefore, design engineers must prioritize safeguarding ADAS components from failing in these circumstances and verifying their safety in real-life situations. Testing and validation can become problematic when legacy methods such as gaskets and seals bolster ADAS reliability.
Possible Issues with ADAS Testing Protocols and Traditional Reliability Methods
Issues with ADAS reliability testing protocols may include:
● Testing must confirm that a system will handle situations that can be predicted and that ADAS will reliably work under unknown circumstances.
● Proper validation and verification can entail testing many conditions, particularly as vehicle design shifts towards fully autonomous vehicles.
● Testing for scenarios on a test track may be impractical when methods such as seals and gaskets are used for ADAS reliability.
For example, to test that a seal will continue to prevent ingress while exposed to vibration, you might have to wait for weather conditions to occur naturally, including snow, rain, or humidity. Although you can use equipment to mimic these weather conditions, this will add to testing complexity.
It's Possible to Simplify ADAS Reliability
As noted, seals and gaskets can become dislodged in many situations, which would have to be recreated and accounted for to validate and verify ADAS component reliability if they are the primary protection method. This unpredictability raises complications during the design and validation process.
Furthermore, as more features are built into vehicles, more components will need to fit in. The bulk of seals, potting, and traditional conformal coatings can lead to more design challenges. These conventional methods can also complicate lightweighting efforts as they add unnecessary weight.
HZO’s proven, trusted Parylene coatings solve these testing and design challenges. These conformal coatings come in several types, including Parylene N, Parylene F (VT-4), and Parylene C, demonstrating excellent performance in mission-critical applications for decades, in part due to uniform coverage, barrier properties, and less stress on mechanical structures.
HZO Coatings for Automotive Corrosion Protection
We’ve proven that our coatings can deliver as much – or more – flexibility, fungus resistance, flammability, dielectric withstanding voltage, thermal shock, moisture, and insulation resistance at a fraction of the mass of conventional coatings, passing the IPC CC-830C test at 50% of the film thinness. Unlike seals and gaskets, Parylene does not stop providing protection when exposed to unpredictable situations, such as drops and falls. The coating is well studied and, when appropriately applied by engineers who understand the parameters of an application, will withstand the lifecycle of the product it is enabling.
Class | Type | Specimen – Average Coating Thickness [μm] | |||
---|---|---|---|---|---|
1 | 2 | 3 | 4 | ||
XY | Parylene N | 25 | 25 | 23 | 23 |
XY | Parylene C | 31 | 30 | 30 | 32 |
XY | Parylene F | 46 | 36 | 43 | 29 |
AR/UR | Acrylic | 73 | 73 | 69 | 72 |
SR | Silicone | 102 | 99 | 114 | 154 |
AR/UR | Acrylated Polyurethane | 91 | 91 | 107 | 107 |
Below, you can see how our coatings performed in automotive validation tests.
Contents | Requirements | Test Results |
---|---|---|
Operations Test | Operate for 24 hours at 23 Degrees C | Operate for 24 hours at 23 Degrees C |
Coating Property | No Pinhole and Uncoated Area | No pin hole and uncoated area Coating thickness 225±3 [μm] |
Electrical Test | Dielectric withstanding voltage: Over 1.5 [kV] Insulation resistance: Over 10 [GΩ] IPC-B-25A standard test board pattern Dv |
Over 1.5 [Kv] Over 10 [GΩ] |
Corrosion Test | Salt spray (35 °C, NACI, 96 hours): No corrosion on chip leads |
No corrosion on chip leads |
Enhanced Component Reliability and Increased Resistance to Fluids and Oils
The automotive operating environment includes exposure to chemicals such as oil, antifreeze, standing water, and cleaning fluids. HZO Parylene coatings offer dependable protection for various leak, environmental, splash, and submersion test requirements.
Protection Characteristics | Unprotected PCB | Mechanical Seal | Silicone/Acrylic Coatings | Parylene Coating |
---|---|---|---|---|
Protection Barrier | None | Good, but can be compromised with drops & temperature. | Good, but can be thick & porous depending on the application. | Excellent. Can peel if not properly applied. |
Hydrophobic | No | No | Yes | Partial |
Thickness | N.A. | Millimeters | μm – Millimeters | 2μm – 50μm |
Protection Against Water | Poor | Good – Ingress Poor – Penetration | Good | Excellent |
Salt/Chemical Protection | Poor | Poor | Varies | Excellent |
Durability | Low | Varies | Varies | High |
Submersion Test Time to Failure | Seconds (IP Rating N.A.) | Varies | Varies | Days to Weeks (IPX7 – IPX8) |
When used as a redundant solution along with legacy methods, our coatings can provide more robust, reliable protection and the ability to reduce sealing, thereby minimizing spacing and weight issues. As the visual below indicates, a mechanical seal can easily be breached. With HZO’s Parylene protection, moisture ingress is not an issue.
Contact HZO for Automotive Component Coatings
If you are interested in Parylene and would like to speak to our industry-leading applications engineering team, please reach out with a message or fill out a quote form to understand your application needs and provide a tailored solution.
Preserving Power: Protective Coatings for EV Battery Corrosion
Engineered Reliability: Conformal Coatings for ECUs
6 Common Conformal Coating Defects & Their Solutions
Mallory is a veteran writer with over a decade of writing experience and has spent over five years at HZO learning about coating technology from the best minds in the industry. Professionally, Mallory is especially interested in the process of problem-solving and watching how the engineering team develops solutions that ensure business requirements are met. Over her years at HZO, Mallory's writing has been cited in industry whitepapers, including "Parabolic Model for Optimum Dry Film Thickness (DFT) of Corrosion Protective Coatings" and "Universal Approach to Integrating Reduced Graphene Oxide into Polymer Electronics." All of Mallory’s blogs are reviewed for accuracy before publication.
Additional Resources
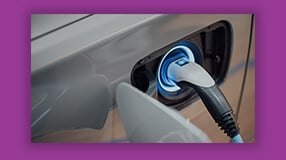
Coating Electric Vehicle Charging Stations For Safer, Tougher Reliability
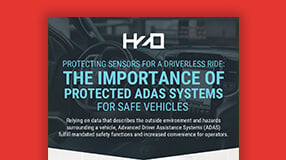
See a Visualization of the Benefits of Protective ADAS Coatings
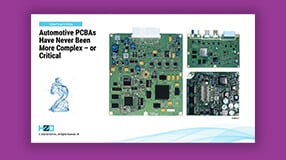
Achieve Automotive Reliability in Harsh Service Environments
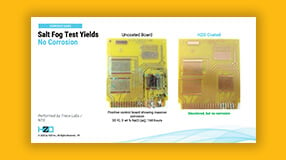