Preserving Power: Protective Coatings for EV Battery Corrosion
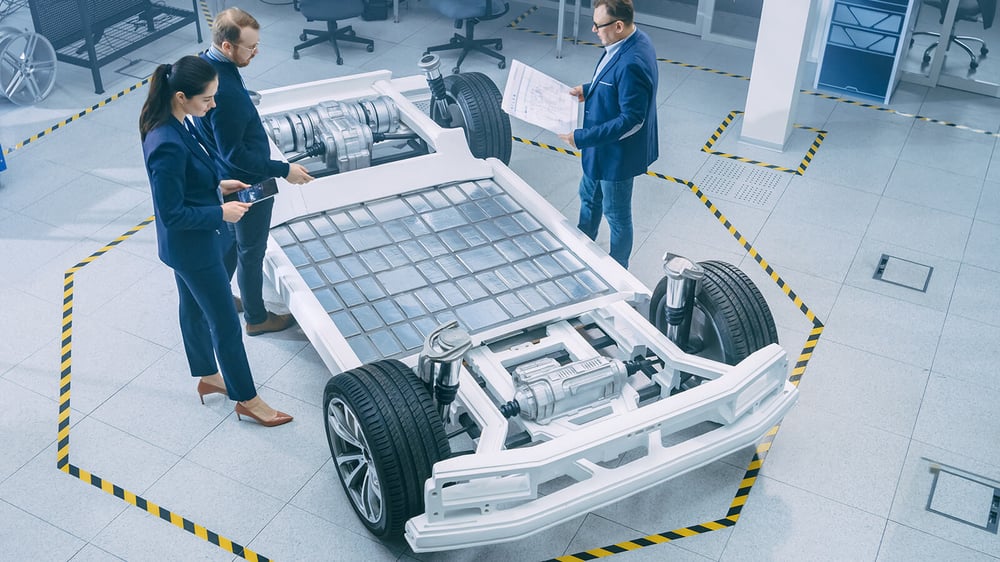
EV batteries promise to revolutionize transportation as we know it, but is it all positive? The future of electric vehicles is riding on the dependable operation of these energy storage vessels, so their reliability is vital. Unfortunately, like all mechanical and chemical processes, battery technology isn’t foolproof and is susceptible to failure, especially in the hazardous environments in which they perform. To better understand EV battery weaknesses and address them, it’s key to understand their origins and what steps are being taken today to safeguard against potential failure points, no matter the circumstance.
Check out HZO's Automotive Brochure
How Old is the Electric Car?
The electric car is synonymous with the future of transportation. However, few may realize that its inception dates to 1881, four years before Karl Benz designed and built the first practical internal combustion vehicle. When consumers were polled in 1900 at the National Automobile Show in New York, the design was so popular that they voted electric vehicles the top choice over steam and combustion engines.
So why did the combustion engine ultimately win the race to mass adoption? Because of the same technical challenges facing EVs today: batteries. Early 20th-century battery technology was no match for the stored energy found in gasoline, nor could the average consumer purchase these primitive batteries due to price constraints.
EVs are Gaining Speed
However, in the early 21st century, battery technology has significantly improved, and the cost is within an affordable range. Finding solutions to these legacy problems has led to a staggering projected growth rate of 1,177% for EVs globally from 2020 to 2030.
Ensuring a Long Road Ahead
With this projected growth comes the compounding headache of ensuring the batteries operate reliably. Millions of drivers, commuters, and enthusiasts blindly rely on their vehicle’s battery to function as intended, no matter the driving conditions.
What are the potential points of failure in today’s batteries, including the rechargeable lithium-ion (Li-ion) batteries used to power EVs? Two natural threats can stop a battery, and therefore the vehicle it is powering, in its tracks: corrosion and strong electrical activity.
- Corrosion: Corrosion is a common enemy to virtually all electronic components, and battery systems are no exception. This natural process occurs when a refined metal is converted to a more stable form, such as its hydroxide, sulfide, or oxide state, leading to the material’s deterioration.
- Strong electrical activity: Strong electrical activity, including short-circuiting, can wreak havoc on EV battery technology. Where corrosion can be a slow killer, short-circuiting can instantly damage sensitive battery circuitry and components, potentially causing irreversible harm to the vehicle and its occupants.
These threats can be addressed safely and thoroughly through protective conformal coatings such as Parylene.
Protecting battery components with Parylene coatings
Corrosion and intense electrical activity can be prevented by properly coating susceptible components within the battery ecosystem. Parylene is a microns-thin conformal coating applied using chemical vapor deposition (CVD), a polymerization process unique to the material, responsible for its pinhole-free and truly conformal properties. Not only does Parylene provide a barrier against corrosive liquids to the parts it is applied to, but the material itself is a strong dielectric, capable of withstanding strong electrical activity. Parylene coatings provide ideal protection to EV battery components, including circuitry, busbars, and cold plates.
Download HZO’s Parylene datasheet
- Battery Circuitry: Every PCB is susceptible to corrosion when left to the elements. EV batteries exposed to typical automotive environments, including rainwater, salt, corrosive chemicals, and more, are no exception. Parylene coatings adhere tightly to the complex topography of a PCB, minimizing the risk of any exposure to corrosive liquids and gases.
- Busbars: Busbars distribute power from high-energy battery packs to e-motors, e-axles, and other assemblies and components. If a battery busbar fails, power cannot be efficiently distributed to other vehicle functions, including the drivetrain or e-axles. The vehicle may also not be able to charge. For consistent operation, busbars require a dielectric coating, such as Parylene, with excellent adhesion, corrosion, and chemical resistance combined with mechanical, thermal, and electrical properties.
- Cold Plates: Overheating can lead to thermal runaway if a cold plate fails, resulting in fires and explosions. Cold plates require protective coatings that strongly adhere to the substrate, can be used in operating temperatures from-40°C to +180°C, and provide excellent heat, oil, and moisture resistance to prevent overheating. These components also require a dielectric coating that protects against water, deionized water, Glycol and water solutions, and dielectric fluids. Parylene coatings can fill these needs.
Testing Parameters: Temperature – 35°C, Concentration – 5% NaCl by weight, Duration – 168 hours
HZO Parylene for EV Battery Component Protection
The electric car has come a long way since its advent in 1881, and we’re barreling towards mass adoption in the next ten years. It’s critical, however, that these vehicles perform as expected to preserve the precious cargo on board. EV batteries are susceptible to failure in the service environments they find themselves in and require proven protection while minimizing weight and cost.
Watch a webinar on improving electronic performance in harsh service environments
It’s crucial for engineers and design teams to not only find a solution to ensure reliability on the road but find an application partner capable of applying the coating consistently and effectively. HZO has gone through the PPAP process, so you can be assured that we have met the associated manufacturability and quality standards laid out by our automotive customers. We have also demonstrated the aptitude to meet the necessary specification requirements and produce parts that consistently meet these requirements during the actual production of parts for these clients.
HZO has a unique ability to coat large, complex boards and components due to proprietary coating and automation equipment, handling parts in large qualities, and producing repeatable quality coatings with high yield rates. Our customer-focused solutions can be delivered with several flexible end-to-end business models as our team of dedicated engineers and SMEs walk clients through every step of the way of the coating process. Are you interested to see how we could help with your EV battery protection needs? Request a quote today.
ADAS Design and Validation for the Real World - Automotive Coatings
Engineered Reliability: Conformal Coatings for ECUs
How to Make Your Lithium-ion Battery Design More Sustainable
Multi-skilled marketing director with more than 18 years’ experience in growing the customers and brands of diverse companies. Ability to meet diverse marketing challenges by utilizing experience, skills, and creativity. Expertise in demand generation, content, branding, design, and communications.
Additional Resources
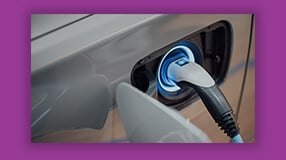
Coating Electric Vehicle Charging Stations For Safer, Tougher Reliability
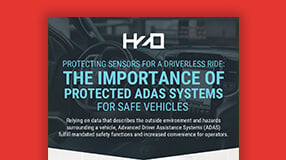
See a Visualization of the Benefits of Protective ADAS Coatings
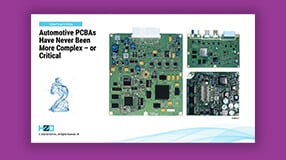
Achieve Automotive Reliability in Harsh Service Environments
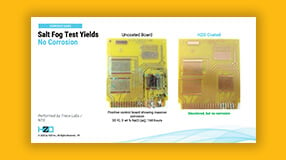