Conformal Coating Removal - How to Get Started W/Reference
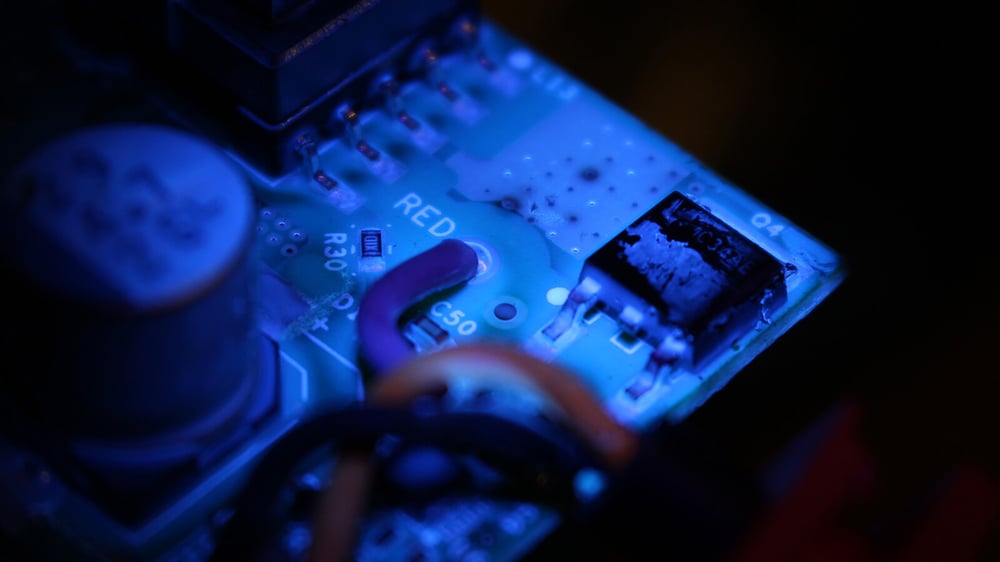
Conformal coatings are polymeric films on printed circuit boards (PCBs) that protect against hazards like moisture, pollution, chemicals, and temperature changes. This layer of material is vital for the longevity and reliability of electronic parts. But sometimes, conformal coating removal or rework is necessary.
There are five primary conformal coating materials: acrylics, epoxies, silicones, urethanes, and Parylene. Each material presents its advantages, limitations, challenges, and application methods. Understanding these details can help operators determine how best to remove each material. This is why we will start with a brief summary of each coating material's properties.
Acrylic (AR) Conformal Coating Properties
- Low moisture absorption
- Relatively short drying times
- Clear protective coating
- Good electrical and physical properties
- Typically brushed, sprayed, or dipped
Epoxy (ER) Conformal Coating Properties
- Very robust
- Excellent chemical and abrasion resistance
- Very rigid conformal coating
- High dielectric strength
- Typically brushed, sprayed, or dipped
Read more about epoxy conformal coating
Silicone (SR) Conformal Coating Properties
- Good humidity and moisture resistance
- Low toxicity
- Easy to apply
- Easy to repair
- Typically brushed, sprayed, or dipped
Properties of Urethane (UR) Conformal Coatings
- Moisture and oil-resistant
- Fungicidal
- Good flexibility
- Can be thinned to achieve a chosen viscosity
- Typically brushed, sprayed or dipped
Read more about polyurethane conformal coating
Properties of Parylene (XY) Conformal Coatings
- Biostable, biocompatible
- Excellent chemical resistance
- Superior conformality
- Exceptional corrosion resistance
- Applied by chemical vapor deposition (CVD)
Learn about Parylene coating
Why Does Conformal Coating Need to be Removed?
- Incorrect application - this may lead to incomplete coverage, bubbles, or excessive thickness. If these defects hurt the circuit board's function or reliability, operators must remove and reapply the coating.
- Need for repairs - during repairs, removal allows for precise soldering and component replacement.
- Rework - this often involves altering circuits, necessitating access that is obstructed by existing coatings.
- Failure analysis - failure analysis can prevent future errors. But, technicians must examine the original circuit materials without obstruction.
Read the definitive paper on electronic protection methods
Before Removing Conformal Coatings - Safety Precautions
Safety is paramount before removing conformal coatings from electronic components. The compounds and methods for stripping conformal coatings can be risky. If proper precautions are not followed, they can harm health.
Essential Safety Measures
Dedicated working environments with adequate ventilation are required. This is non-negotiable. Solvent fumes can be harmful if inhaled in high concentrations. So, a well-ventilated area, using natural means or fume extractors, minimizes inhalation risks. Also, some coating removal techniques create dust or aerosols. So, use suitable air filtration systems.
Flammability is another factor to consider. Several solvents and chemicals employed in the removal processes are highly flammable. To prevent combustion, keep the workspace free of ignition sources, like sparks or open flames.
Electricity poses a significant risk. Turn off and unplug all devices. This will prevent accidents during the conformal coating removal process.
How to Remove Conformal Coating - First Step
Check the coating on the PCB you want to remove. This will help find the best method to remove the conformal coating. You can usually confirm this by contacting your coating supplier. Or, look for a JEDEC or IPC label on the board. Coatings are designated as AR, SR, ER, UR, or XY, indicating which coating you are working with. If there are no labels, you can still identify the material via methods outlined by the IPC below.
Each conformal coating has distinct properties. So, you can test for transparency, solubility, hardness, thermal removal, and thickness. These tests will show you which type of coating you have. For more information, see IPC’s “Coating Removal, Identification of Conformal Coating” guidelines.
Coating Removal Techniques
After identifying your coating, the next step is to choose the removal technique. Popular methods are briefly discussed below:
Peeling Method
For RTV silicone or thick rubber coatings, use a dull blade or knife to slit and peel off the coating.
Chemical Solvent Method
This process effectively removes urethane, acrylic, and silicone coatings. Prep the area with high-temperature tape and apply solvent using a foam swab.
Grinding and Scraping Method
This removal technique can grind away thin, hard coatings with a micro motor or rotary-style tool or soft coatings with a rotary brush.
Thermal Method
Using low-temperature heat, gently burn and melt the coating material.
Micro Sandblaster Method
This technique involves projecting a fine abrasive powder onto the coating to flake off the material.
Which Technique is Best for My Conformal Coating Material?
Urethane Coatings
- Grinding and scraping method
- Solvent method
- Micro-blasting method
Acrylic Coatings
- Thermal removal method
- Chemical solvent method
- Scraping and grinding method
- Micro-blasting method
Epoxy Coatings
- Thermal removal method
- Grinding and scraping method
- Micro-blasting method
Silicone Coatings
- Grinding and scraping method
- Micro-blasting method
- Chemical solvent method
- Thermal method
Parylene Coatings
Parylene coatings are often hard to remove. You can usually use micro-blasting, grinding, scraping, and thermal methods. But at HZO, we have simplified the reworking process using technology. The next blog in this series, will discuss reworking Parylene in general and detail how we simplify the process.
For more information on thin-film coatings for your project, contact us today.
6 Common Conformal Coating Defects & Their Solutions
Epoxy Conformal Coating Evaluation Guide
Conformal Coating vs Potting/Encapsulation - The Pros & Cons
Mallory is a veteran writer with over a decade of writing experience and has spent over five years at HZO learning about coating technology from the best minds in the industry. Professionally, Mallory is especially interested in the process of problem-solving and watching how the engineering team develops solutions that ensure business requirements are met. Over her years at HZO, Mallory's writing has been cited in industry whitepapers, including "Parabolic Model for Optimum Dry Film Thickness (DFT) of Corrosion Protective Coatings" and "Universal Approach to Integrating Reduced Graphene Oxide into Polymer Electronics." All of Mallory’s blogs are reviewed for accuracy before publication.
Additional Resources
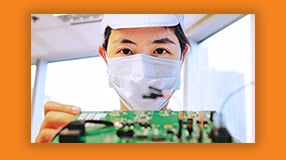
Which is Better For Your Application? Conformal Coating or Potting?
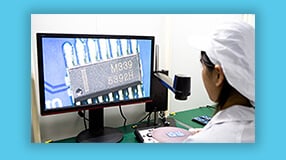
Learn About Common Conformal Coating Defects And How To Fix Them
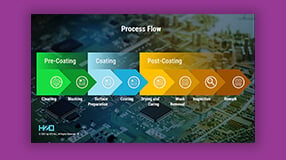
Learn How To Incorporate Conformal Coating Into Your Manufacturing Process
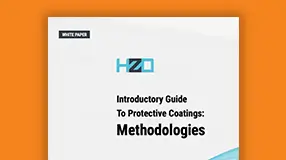