Sweat, Saltwater, and Liquid Submersion Protection at 50% Thickness of Conventional Coatings
HZO coatings can meet any IP rating with a scalable, cost-efficient, turnkey solution.
Meet Specifications with Superior Coating Properties
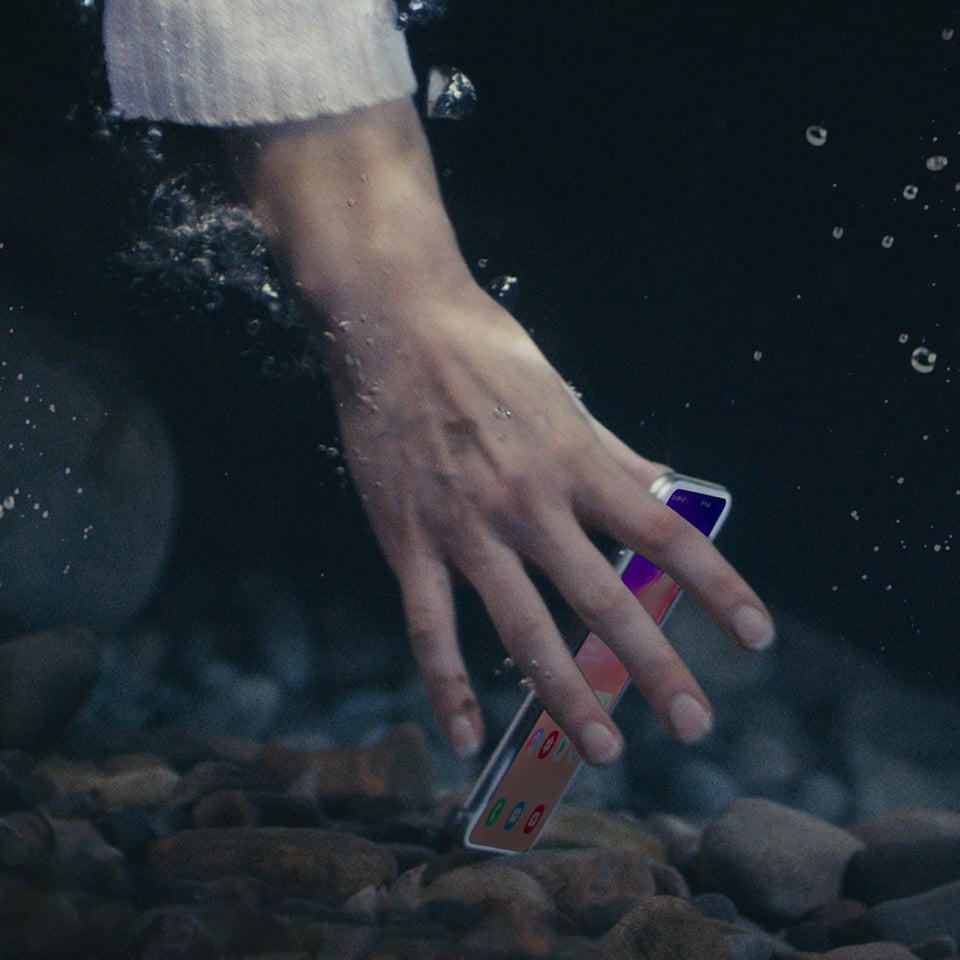
Electrical Properties
ELECTRICAL PROPERTIES | HZO PARYLENE C | ASTM |
---|---|---|
Dielectric strength (V) @ 25.4 um (1 mil) | 5,500 | D149 |
Dielectric strength (V/um) @ 25.4 um (1 mil) | 220 | D149 |
Dielectric constant (60 Hz) | 3.13 | D150 |
Dielectric constant (1 kHz) | 3.01 | D150 |
Dielectric constant (1 MHz) | 2.92 | D150 |
Dissipation factor (60 Hz) | 0.022 | D150 |
Dissipation factor (1 kHz) | 0.017 | D150 |
Dissipation factor (1 MHz) | 0.013 | D150 |
Volume resistivity (23 C, 50% RH, cm) | 6.0 x 1016 | D257 |
Surface resistivity (23 C, 50% RH, ) | 1.0 x 1015 | D257 |
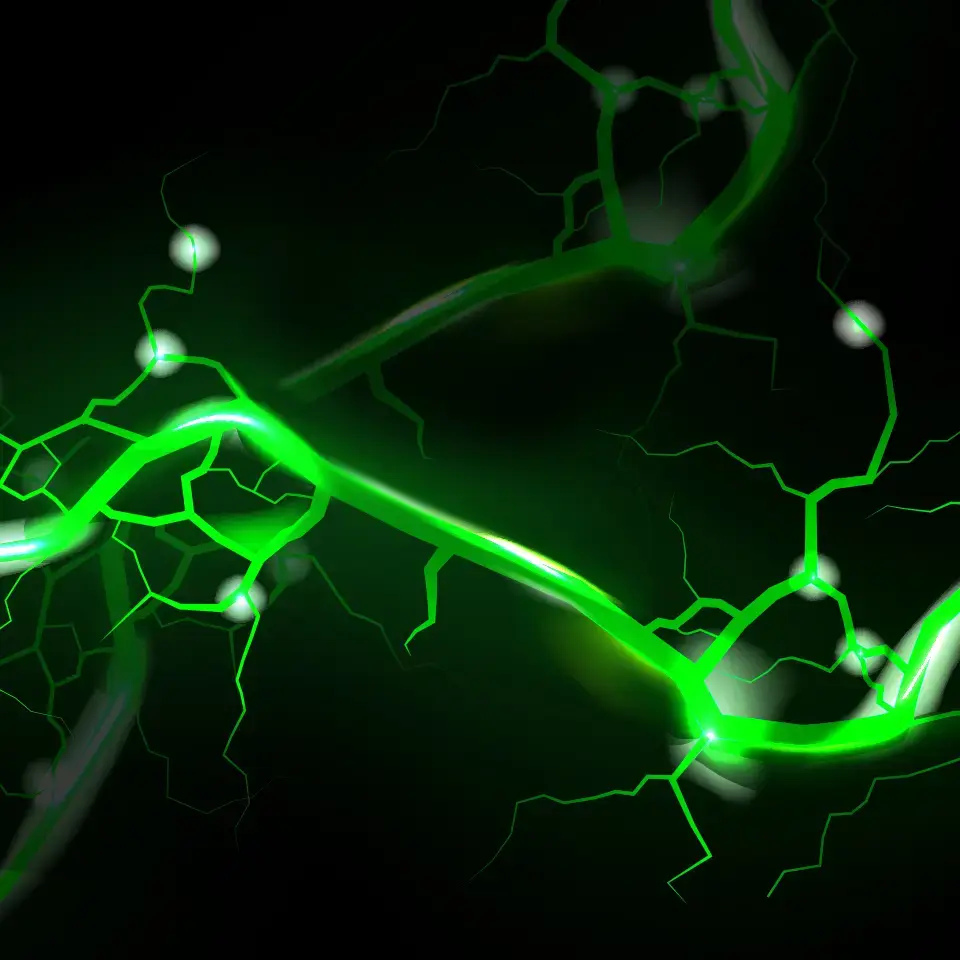
Low dielectric constant with good high-frequency properties
Good dielectric strength
High bulk and surface resistance
Insulation
Barrier Properties
Polymer | Gas Permeability at 25 °C, (cc·mm)/ (m2·day·atm) | WVTR (g·mm)/ (m2·day) |
||||||
N2 | O2 | CO2 | H2 | H2S | SO2 | CI2 | ||
Parylene C | 0.4 | 2.8 | 3.0 | 43.3 | 5.1 | 4.3 | 0.1 | 0.08 |
Parylene N | 3.0 | 15.4 | 84.3 | 212.6 | 313 | 745 | 29.2 | 0.59 |
Parylene D | 1.8 | 12.6 | 5.1 | - | 0.6 | 1.9 | 0.2 | 0.09 |
Parylene F (VT-4) | - | 16.7 | - | - | - | - | - | 0.28 |
Epoxy (ER) | 1.6 | 4 | 3.1 | 43.3 | - | - | - | 0.94 |
Polyurethane (UR) | 31.5 | 78.7 | 1.81 | - | - | - | - | 0.93 |
Silicone (SR) | - | 19,685 | 118,110 | 17,717 | - | - | - | - |
Barrier Protection for Resilient Products
Resistant to:
SWEAT
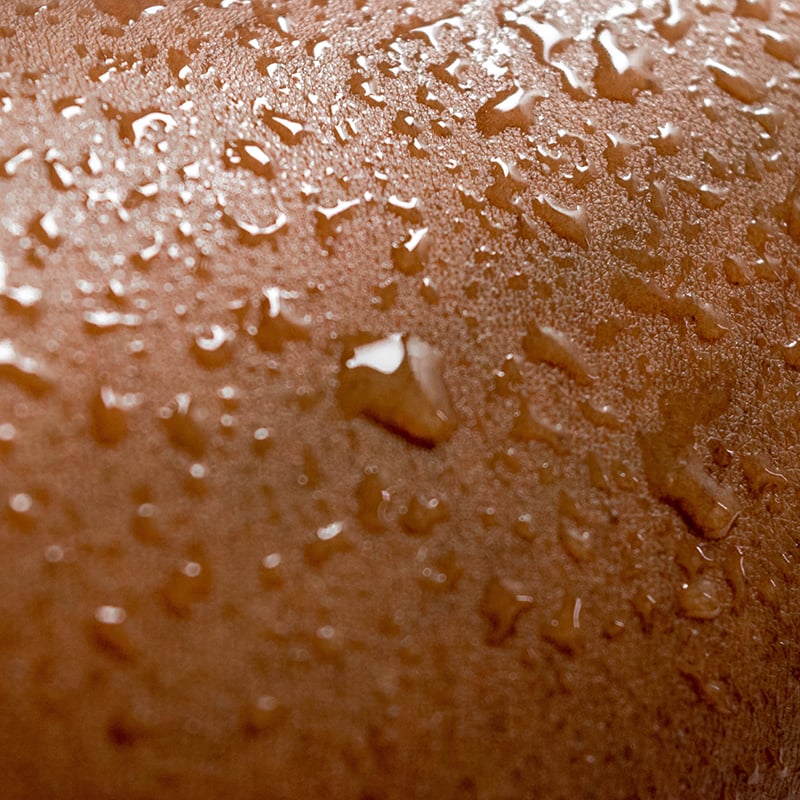
HUMIDITY
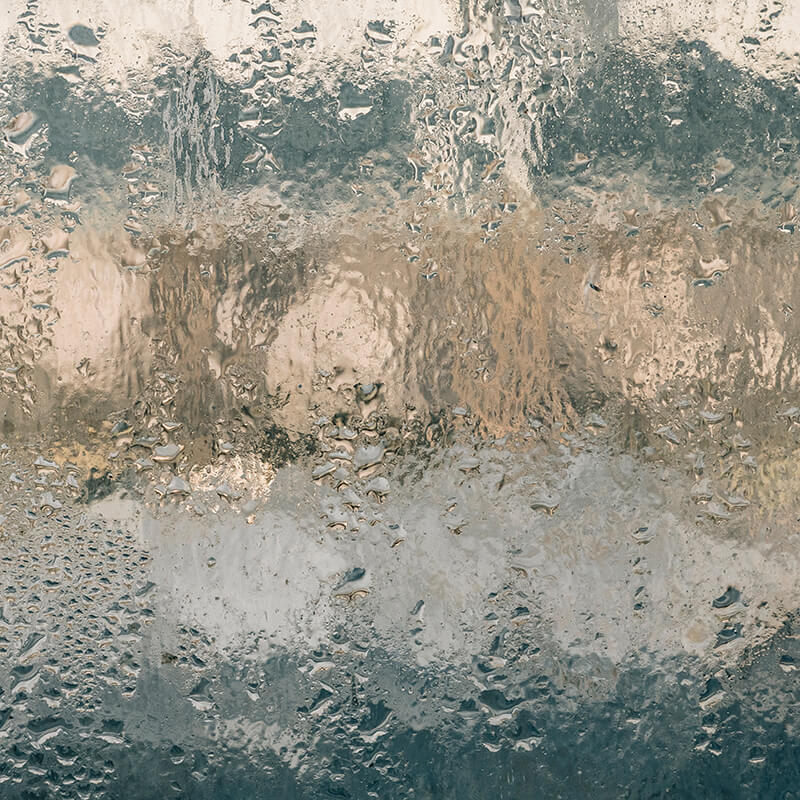
SOLVENTS
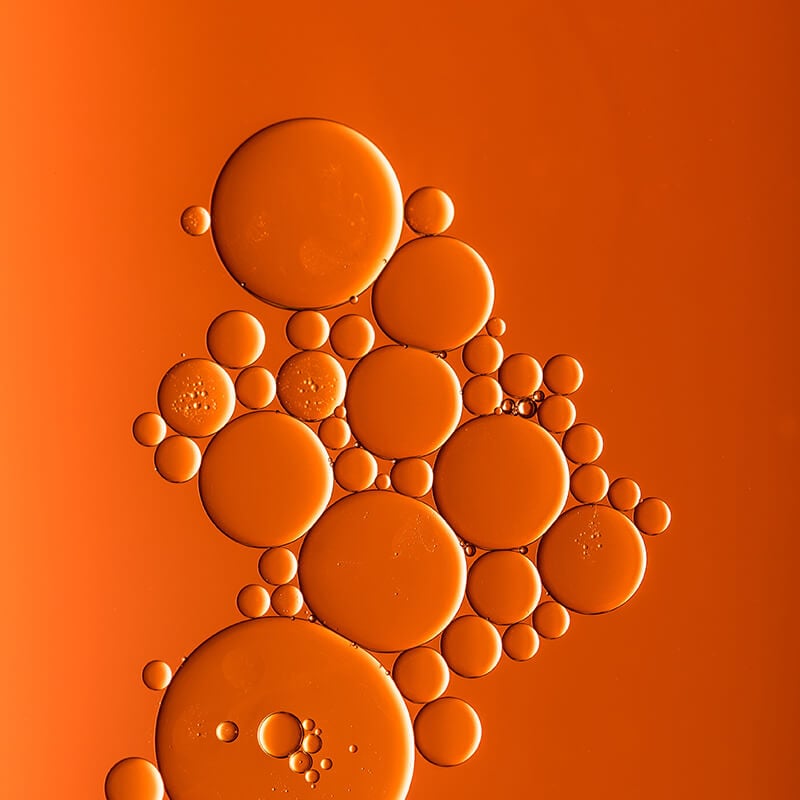
MOISTURE
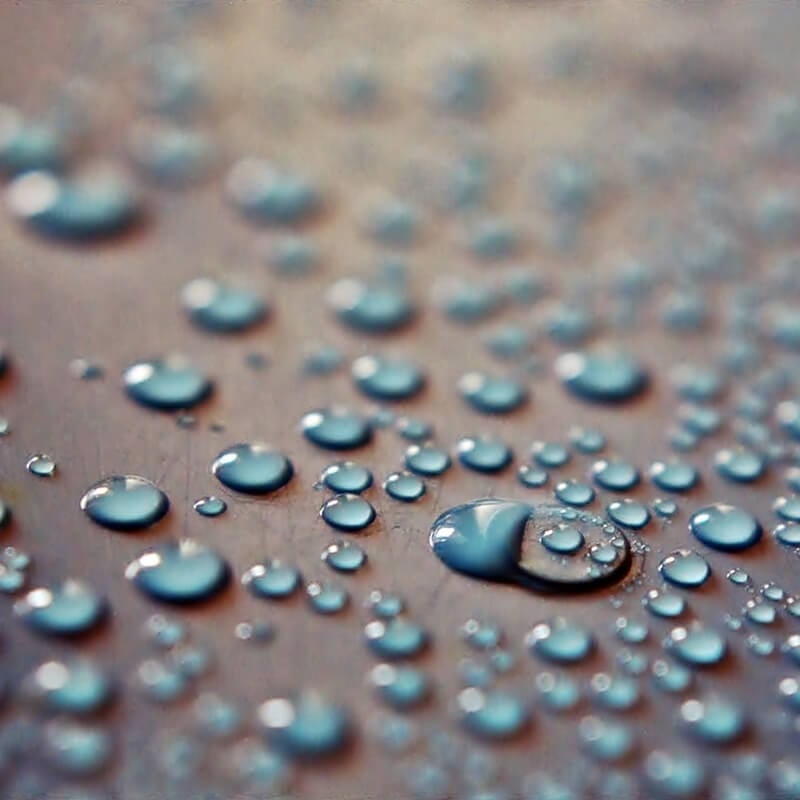
Simplify Reliability
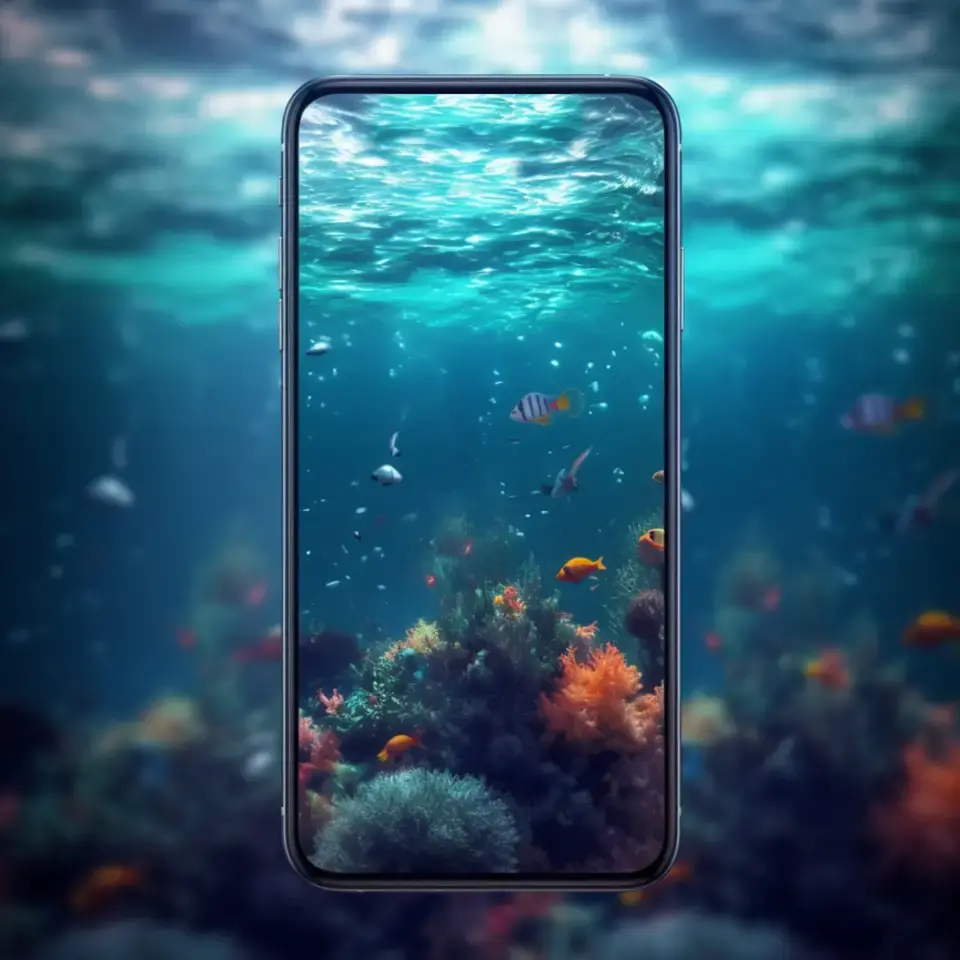
Meet Any IPX Claim
-
Splash or submersion is possible with HZO coatings
-
Tested for over 1,000 hours of submersion
Meet Sustainability Market Claims and Regulations
-
HZO Parylene coatings are UL 94-VO certified
-
HZO has non-halogenated RoHS, REACH and Prop 65 compliant coatings
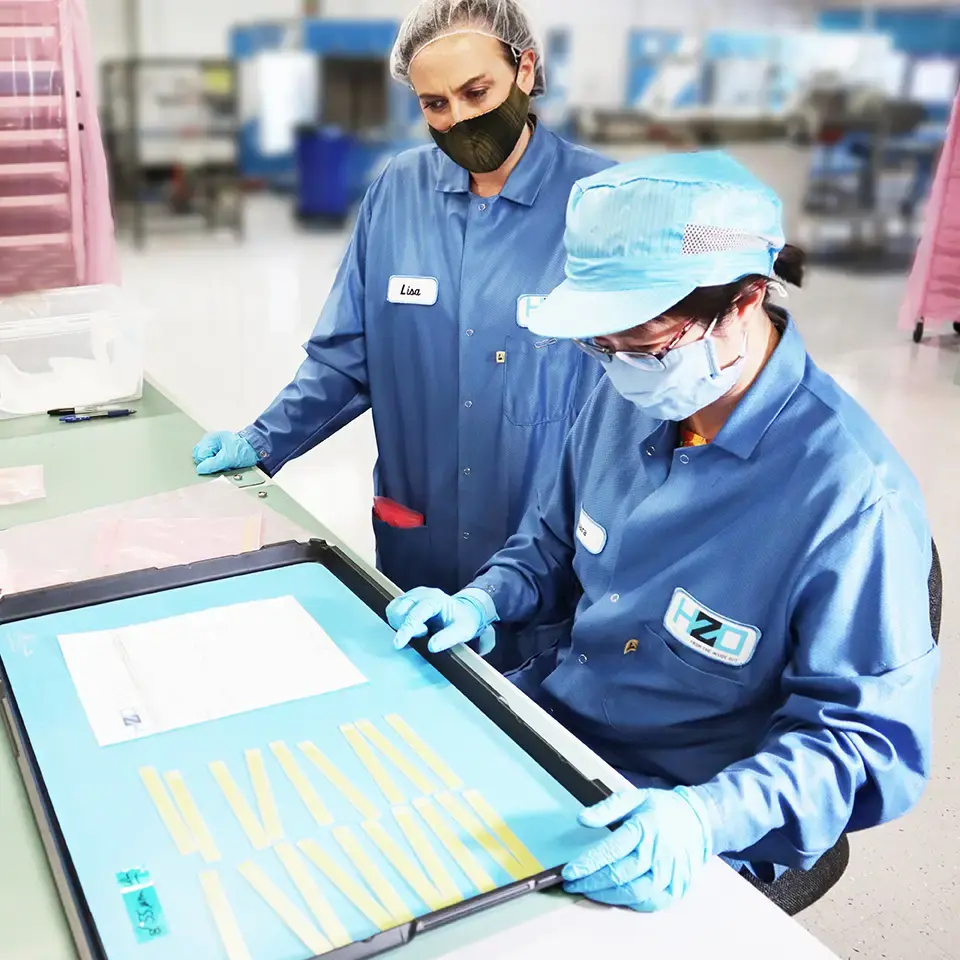
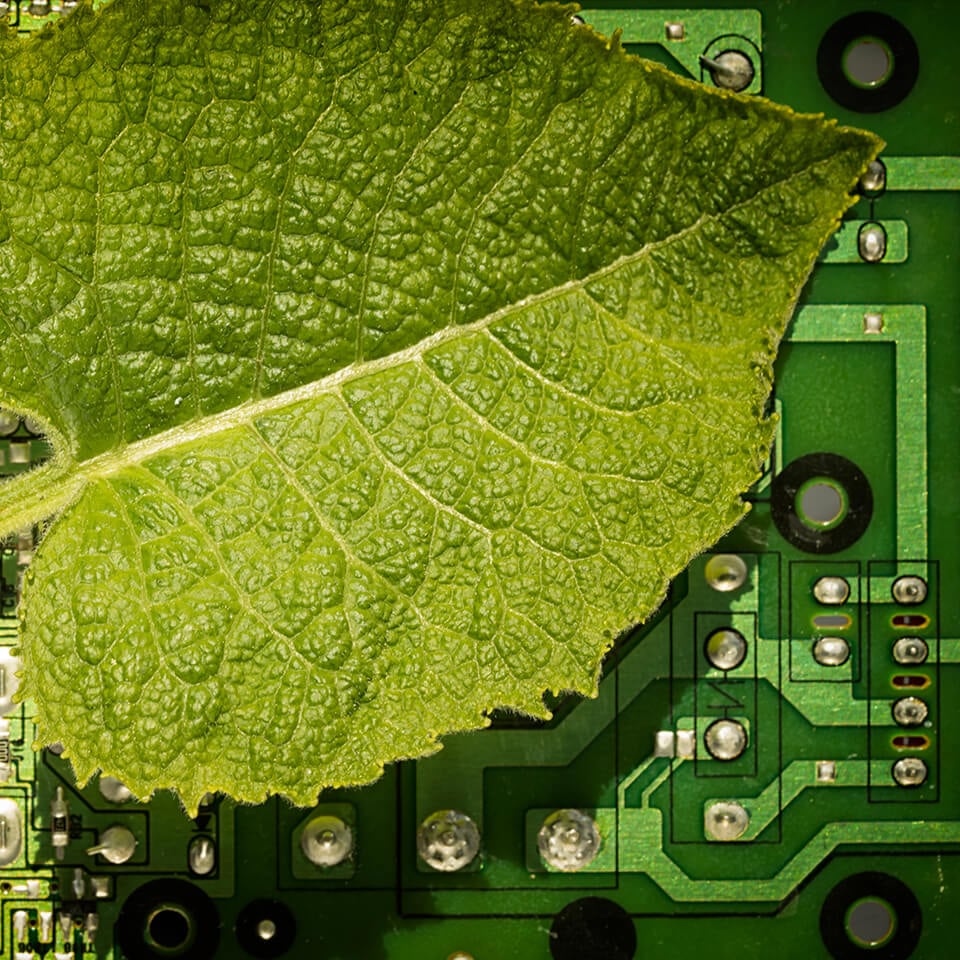
HZO Coatings have:
-
No VOCs
-
No Solvents
-
No Catalysts
-
No Disposal Issues
-
No Pollution Threats
-
No Cure Time
-
Biostable
-
Biocompatible
Reduce eWaste and Promote Reuse and Repair with Long-Lasting Coating Material
Lifetime of HZO Parylene coatings at different temperatures in air (with oxygen).
60 °C | 80 °C | 135 °C | 150 °C | |
---|---|---|---|---|
Parylene C | ~100 years | ~20 years | ~70 hours | ~24 hours |
Parylene N | ~10 years | ~1 year | ~9 hours | ~1 hour |
Coating Properties
Uniform & Pinhole-Free
No voids or gaps for ingress.
Optically Transparent
Excellent Conformality
Can completely penetrate voids as narrow as 0.01mm.
No Catalysts
No initiators in polymerization process. Free from trace ionic impurities.
Minimize Coating Thickness
Thin layers facilitate RF signal transmittance
THICKNESS (μm) | 0.1 TO 5 | 5 TO 12.5 | 12.5 TO 25 |
---|---|---|---|
Relevant Standards | UT Type in IPC-CC-830C | UT Type in IPC-CC-830C | IPC-CC-830B |
Protection Level | IPX3 / IPX4 | IPX4 / IPX7 | IPX7 / IPX8 |
Consumer Electronics Coating Applications
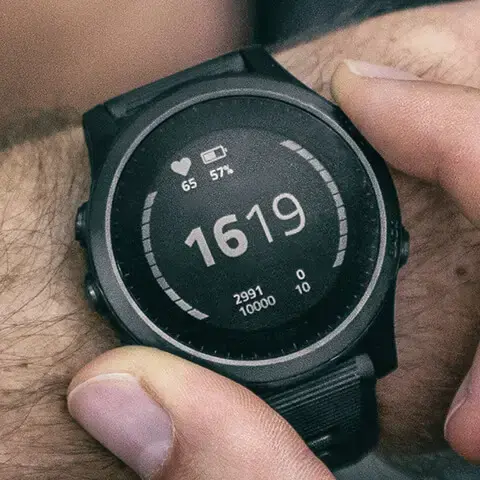
Wearables
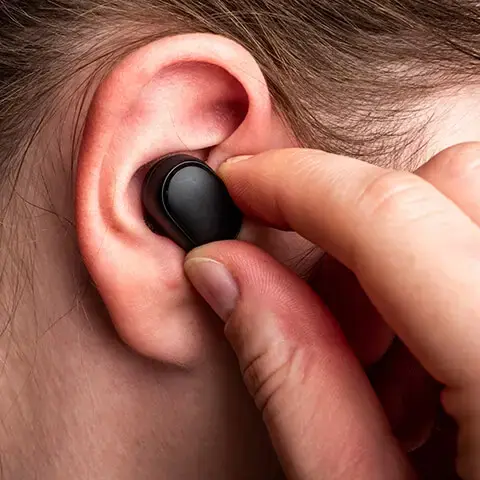
Hearables
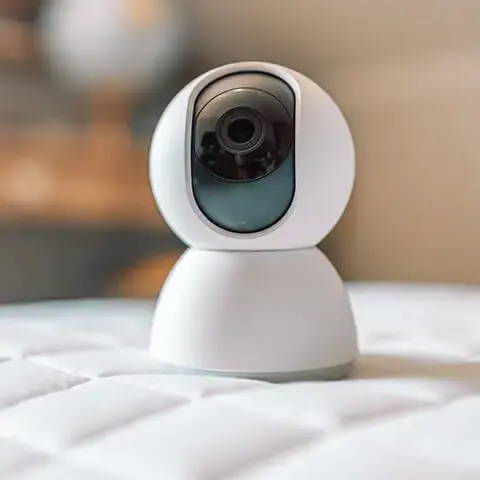
Smart Home
Have an application that isn't listed?
Read about other markets we serve.
Scalability
Mass-Scale Production
Meet mass-scale production within budget or deadline.
Decreased Turnaround
Decrease turnaround time with our equipment designed in-house.
Single Batch
10,000-20,000 hearable components or batteries coated in single batch.
No Catalysts
No initiators in polymerization process. Free from trace ionic impurities.
Coating Process for High Volume Applications
Validation
-
Beginning with provided samples, HZO engineers determine the best coating solution to meet the customer’s protection and manufacturing requirements.
-
HZO engineers work with the customer to integrate their solution into the product’s manufacturing process.
-
Models include coating as a service or direct integration of HZO’s equipment and processes into the production process.

Pre-Production
-
Pre-processing begins with inspection for quality standards and control for product tracking.
-
When required, masking of areas where protection is not needed can be manual or fully automated.
-
High-speed equipment applies masking materials to pre-determined areas of the product’s substrate.
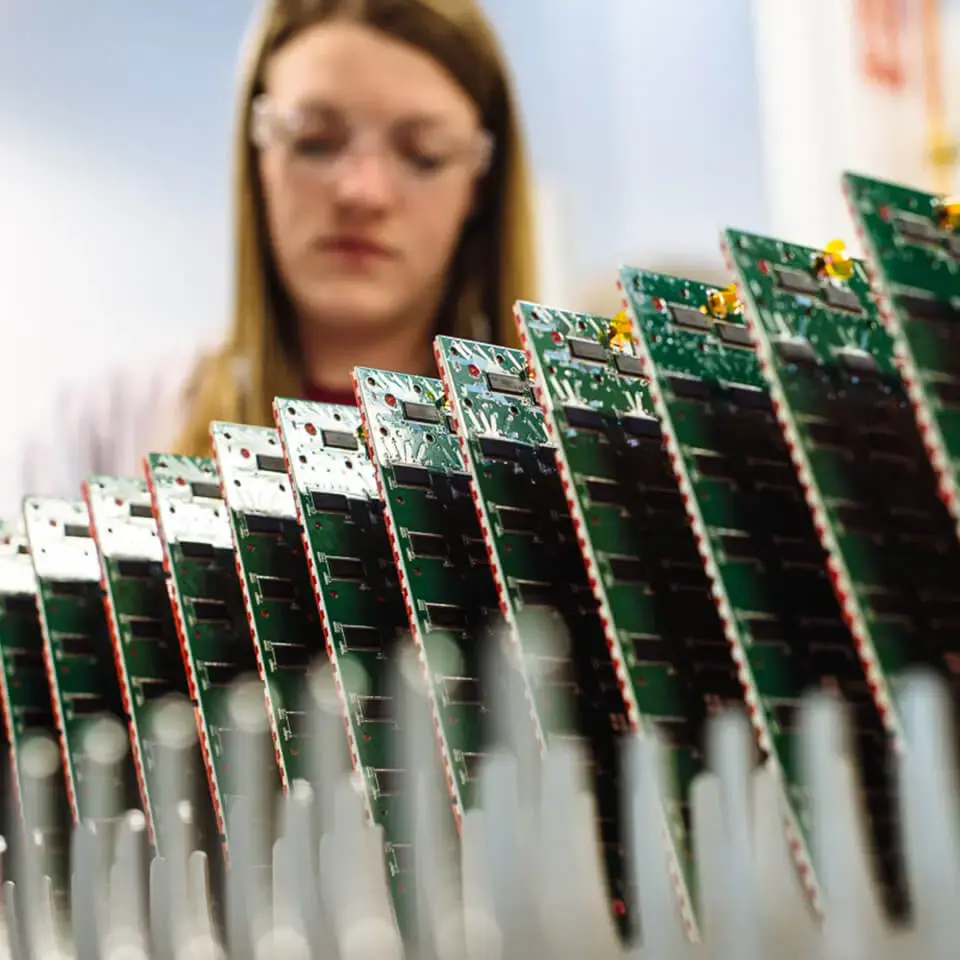
Production
-
The products to be coated are placed inside large HZO coating chambers with a unique cube-shaped design to optimize component throughput.
-
The chemical vapor deposition process begins as the raw material is sublimated into a vapor phase.
-
After pyrolysis, the vapor flows into the vacuum chamber where it is deposited at a low temperature, forming a uniform, nano to microns-thin coating.
-
Typically coating at two times faster throughput than the industry average, the coated components are removed and placed into post-production.
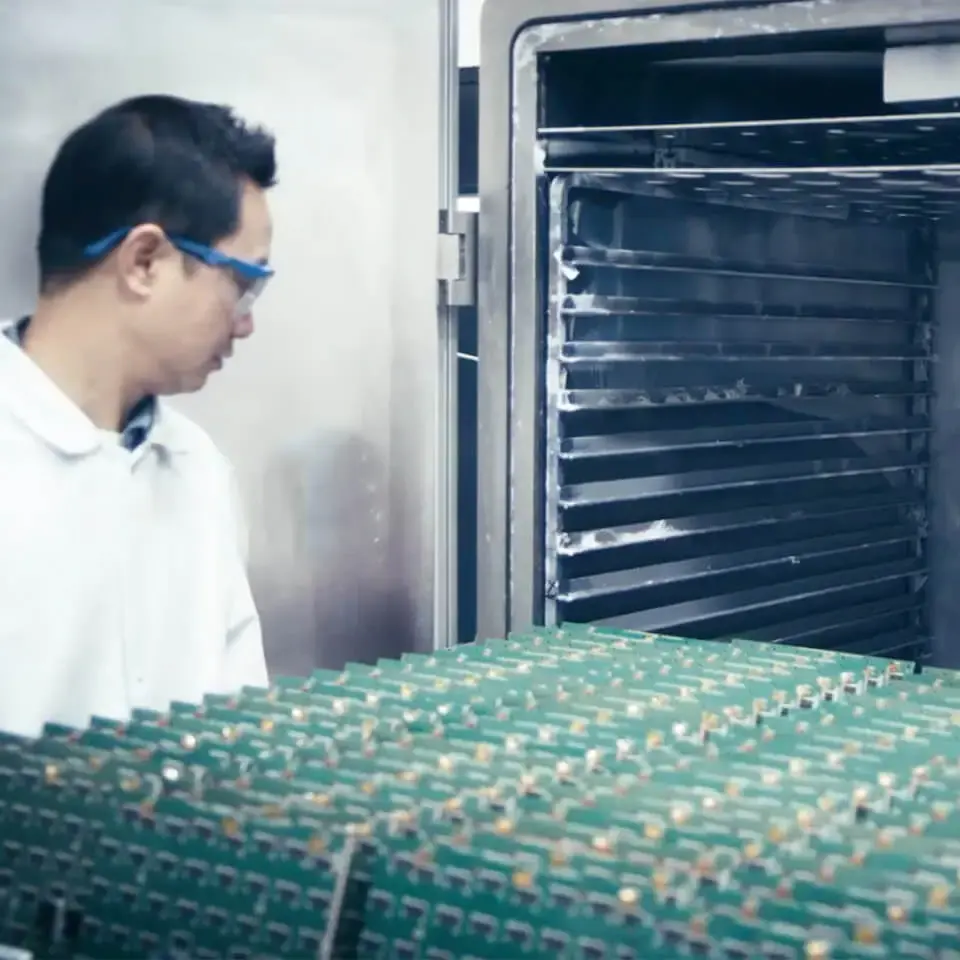
Post-Production
-
After coating, any masking materials are removed with complex accuracy and dexterity, either manually or automated.
-
Laser scoring, ablation, and automated inspection can help mitigate touchpoints.
-
Each product is optically inspected for quality before being sent out.
-
The components are passed along to the next stage in production.

Cost
- IP (intellectual portfolio) backed masking automation reduces labor and costs
- Automate, Semi-automate, and Manual Masking Available
- Rework expertise
Quality
Millions of components coated, no product returns attributed to coating issues
Market Experience
Fortune 100 consumer electronics customers
Are HZO Protection
Solutions Right for You?
Additional Resources
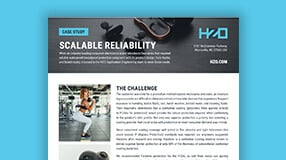
Learn About HZO's Partnership With a Fortune 100 Consumer Electronics Company
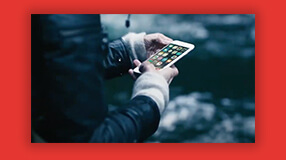
Learn About Why You Need Consumer Electronics Protective Coatings
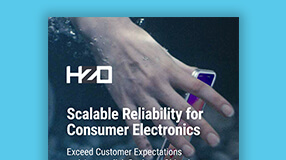
Learn How to Enhance the Reliability of Your Consumer Electronics Product Design
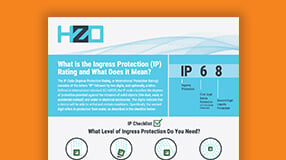