How To: A Wearable Device Design That Consumers Actually Want
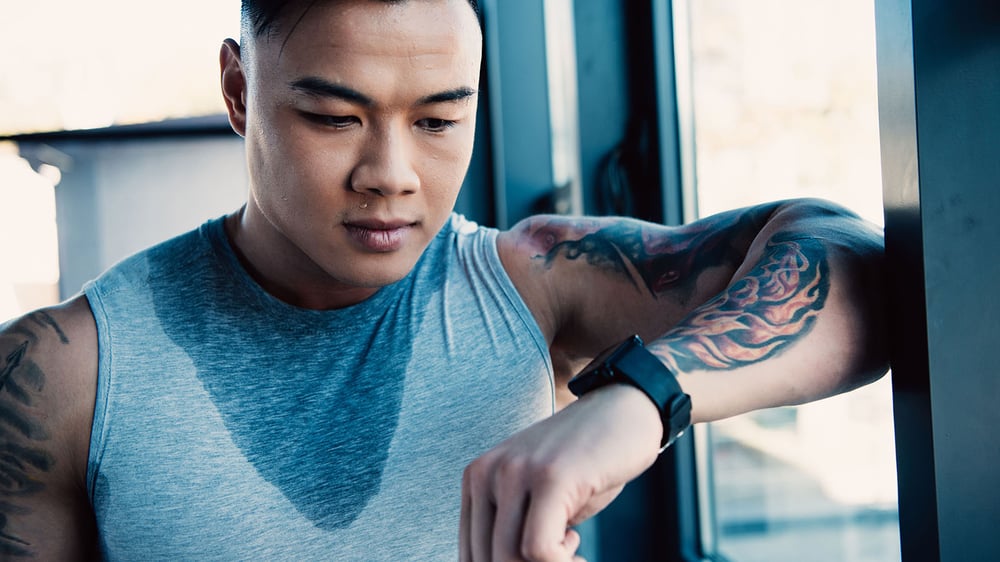
Wearable devices provide insight and convenience to consumers through activity tracking and biometric data that they can easily access through a wearable app. But many wearable product designers have focused too much on producing functional devices without emphasizing the humans that wear them enough. This tendency could be to the detriment of user experience, limit user interaction, and make consumers less likely to purchase from your company again. Here are three quick tips on designing a wearable device that addresses human issues: discomfort and inconvenience, display issues, and lack of ruggedization for real-world usage.
1. Learn How to Make Wearable Technology Truly Wearable
Wearable tech can be challenging for design engineers because the body moves constantly, and humans want to move without constriction. Therefore, designing small, light, and comfortable wearables should be a priority.
For this reason, it is a good idea to begin the design process with a human factors and ergonomics analysis. This scientific discipline seeks to understand and optimize interactions among humans and systems to improve both system performance and the well-being of humans.
Consumers are likelier to wear devices with thinner, smaller, rounded form factors that lay flush on the body, applying minimal pressure. To ensure your product will be comfortable, test usability factors with real users and determine how easy and comfortable it is to move while wearing your product. Don’t forget to consider people’s different body sizes and types. For example, our customer Nike offered their FuelBand in several wristband sizes that the consumer would choose during the purchase process.
Finally, remember to design for every aspect of the use cycle, such as cleaning, bathing, showering, and leisure activities. Make an effort to be conscious of when and how humans clean their wearable devices so you can create a usable, convenient, easy-to-clean device consumers will want to use. Remember that users will not want to remove their devices during routine activities such as bathing and showering (and may not take off their wearables before swimming or entering a sauna), and accommodate this in your product design. The more convenient it is to use your product, the more consumers want it.
Watch our video series about designing reliable consumer electronics devices.
2. Consider the Display On-Device and What it Means for User Experience
To determine the right display for your wearable, ask yourself about the level of interaction required with the wearable. Wearables without display afford more design flexibility, are cheaper, and are simpler to produce. However, no available visual communication with the wearable will limit the level and scope of human interaction with it.
Minimal output displays portray selected information critical to the wearable experience. This type of display is one-directional, so the user can view it but cannot enter any input, limiting interaction. Another option is a full display, which allows for strong device interaction and a wider feature set. Determining which type of display is most appropriate for your users is an important decision that, unfortunately, may entail an aesthetics-functionality trade-off.
No matter which display you choose, you should expect and design wearables that will endure connectivity problems. Try to integrate some core functionality in your product’s offline mode when planning for your wearable UI. At a minimum, ensure the product explains what is happening to the user by incorporating wearable alerts when there is no internet connection to avoid confusion. If you choose a wearable with no display, this could be indicated through the mobile app.
3. Learn How to Design a Wearable Device for the Real World
Designing devices worn on the body can be complicated because they must reliably work in variable operating environments. In other words, they must go where humans go. Humidity, submersion, harsh weather, and corrosive exposure threaten wearable PCBAs. Don’t make the mistake of simply ensuring a device can pass reliability tests in the lab but not designed for the real world. Typically, consumers use Ingress Protection (IP) standards to guide their purchasing decisions, so achieving a certain level of water resistance is necessary.
Download our IP checklist.
Conventionally, product designers have used seals to do this, but this method may not focus as much on user experience as it should. Humans frequently move, exposing these devices to vibration, which can dislodge seals and leave wearables unprotected from corrosion.
Another option is conformal coatings for wearable moisture resistance and corrosion protection. These polymeric films are applied directly to the circuitry as a barrier against many environmental threats. However, wearables have minimized form factors and require these coatings to apply thick layers, which may be too bulky and heavy, causing discomfort and inconvenience.
These legacy methods are often appropriate and do have their place. However, if you are placing more emphasis on users to improve your product experience, it might be worth considering Parylene conformal coatings. HZO’s Parylene can provide protection that meets or exceeds the corrosion protection of other conformal coatings at 50% thickness.
Visit our Consumer Electronics market page
The chart below describes Parylene thickness and the corresponding standards and IP protection levels they meet:
Table 1: Parylene Thickness, Relevant Standards, and IP Protection Levels
Thickness(μm) | Relevant Standards | IP Protection Level |
---|---|---|
0.1 to 5 | UT Type in IPC-CC-830C | IPX3/IPX4 |
5 to 12.5 | UT Type in IPC-CC-830C | IPX4/IPX7 |
12.5 to 25 | IPC-CC-830B | IPX7/IPX8 |
Parylene Conformal Coatings for Wearables From HZO
As a proven method trusted for decades in mission-critical applications, Parylene eases many design headaches and addresses the user-focused issues above. As it provides robust protection at a fraction of the mass of legacy methods, you can make ruggedized wearables that are also truly wearable. Parylene’s superior chemical resistance properties allow your users to clean their products throughout the entire product life cycle safely. Additionally, using Parylene instead of seals can make it easy to design and produce wearables that meet finish, style, longevity, and reliability expectations, leading to consumer purchases.
It is possible to minimize offline disruptions because, unlike the other thick conformal coatings and seals, Parylene is applied in thin layers, facilitating RF signal transmittance.
When you work with HZO, our engineers will create a coating solution around your needs that easily fits into your production. From DFM services to QA, our team of experts will walk you through every step of the protection process, eliminating headaches and simplifying your process. If you want to discuss your project with our team, contact us today.
Improving CGM Electronics Designs with Medical Coatings
How to Make Your Lithium-ion Battery Design More Sustainable
Volume Resistivity - Definition, Measurement, Product Design
Mallory is a veteran writer with over a decade of writing experience and has spent over five years at HZO learning about coating technology from the best minds in the industry. Professionally, Mallory is especially interested in the process of problem-solving and watching how the engineering team develops solutions that ensure business requirements are met. Over her years at HZO, Mallory's writing has been cited in industry whitepapers, including "Parabolic Model for Optimum Dry Film Thickness (DFT) of Corrosion Protective Coatings" and "Universal Approach to Integrating Reduced Graphene Oxide into Polymer Electronics." All of Mallory’s blogs are reviewed for accuracy before publication.
Additional Resources
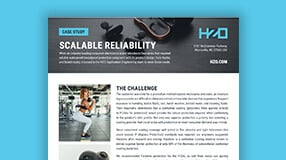
Learn About HZO's Partnership With a Fortune 100 Consumer Electronics Company
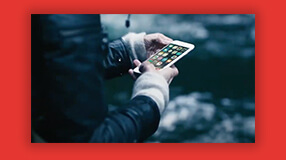
Learn About Why You Need Consumer Electronics Protective Coatings
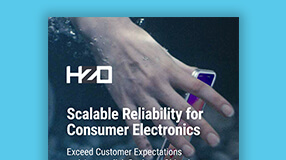
Learn How to Enhance the Reliability of Your Consumer Electronics Product Design
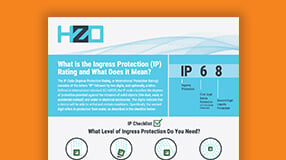